|
Magazine |
|
About |
|
SUMMIT |
|
Contacts |
|
Home |
|
|
|
|
| |
|
|
 |
#3' 2003 |
print version |
ELEKTROSTAL HEAVY MACHINE-BUILDING PLANT SELLS COMPLETE SETS TO THE WEST |
|
Andrei Karunos
The supply to the USA of a roller race shop equipment by the Elektrostal Heavy Machine-Building Plant (EZTM) can by right be named one of the most successful export contracts concluded by Russian machine-builders lately. This enterprise ranks third among the national makers of equipment for metals and tube/pipe industries. Moreover, EZTM is the only Russian producer of oil film bearings.
s early as in the 1950s in the town of Elektrostal near Moscow first oil film bearings were made. At that time the problem with the spare parts for the US mills of postwar lend-lease supply arose. The EZTM design and process engineers started the production of bearings of the required and quite new standard types intended for equipment of their own make as well as for light section and wire rod mills made in East Germany.
It must be noted that, by the time the negotiations on the supplies to the US started, the traditional equipment of EZTM make has been operating in over 40 countries worldwide. Export deliveries began with supplies to East Europe followed by India where the USSR built steel plants, and further on EZTM supplied bar and section mills to Ceylon, Indonesia, Egypt, etc. Western specialists also appreciated the equipment of EZTM make: ten rockright mills were bought by Japan, and the Italians purchased a licence for manufacturing mills of this type.
In 1993, at the Panamerican Exhibition of Metal-Producing Equipment in Cleveland, the first meeting of EZTM specialists with one of the top managers of Timken (USA) took place. This company, along with FAF Kugelfischer Georg Schafer AG (Germany) and SKF (Sweden), is the world leader in the manufacture of bearings.
The US side got interested in the EZTM exposition professionally and invited the Russian colleagues to visit its enterprises where some bottlenecks were demonstrated to them with a request to give their offers.
Yuri Vinogradov, Chief Engineer of EZTM, recollects: "Later on we realized that it had been a kind of technical intelligence". Apparently, the future US partners wanted to make certain of the capabilities of the Russian mechanical engineers.
|
EZTM is an integrated enterprise with two steelmaking shops, an iron foundry, a bronze casting department, a forging shop and a welded structures shop. After heat treatment cast or welded billets enter one of seven specialized machine shops. Pig iron for remelting, long and flat products, tubes/pipes as structurals are supplied by steel works/plants.
|
| |
|
The EZTM designers developed a dozen technical offers. Timken became interested in the implementation of a number of them at its enterprises. It so happened that the Russians had to modernize the equipment of their competitor Mannesmann Demag AG (Germany).
In Vinogradvs words, the problem of the US side was that races for bearings numbering in hundred millions were made by the pressing technique. EZTM offered the rolling process already tested in Russia.
The negotiations were carried on for three years. It was not a simple task to persuade the Western colleagues that the equipment in Russia is not worse, and sometimes even better, than in the US or West Europe.
"At first they got convinced that we are able to make technically interesting and complex machinery, after that they must have been persuaded that our workmanship is good, and at last that we can make timely deliveries", says Vinogradov.
The EZTM people were so sure of their abilities that by the time the Timken delegation arrived for the approval of the preliminary design the model of the main working stand had been already made. In Vinogradovs words, the Americans were surprised, signed the preliminary design at once and stated that they "will be only glad if everything is supplied as soon as possible". When they visited Elektrostal for the second time for the approval of the working drawings they came to see the finished castings.
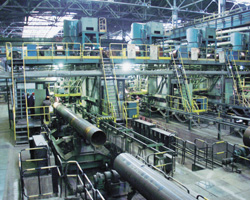 General view of large-diameter gas pipe line (Vyksa Steel Works) |
|
EZTM designed a complete shop for twelve types of roller races to be produced. The rolling process was developed by the All-Russian Institute of Metallurgical Machine-Building (VNIIMETMASH), Moscow. The equipment was supplied to the US but its commissioning was somewhat delayed. In North Carolina where the construction site was bought, there was a shortage of experienced labor force. That is why the Americans had not only to master the Russian technology but also to train the personnel with the assistance of Russian process engineers. It resulted in not 12 but 19 types of roller races put into smooth and profitable production. The Russian equipment was used first to make races for Timken bearings and then to execute orders for automobile industry synchronizer bushings and small gears.
Timken ordered another working stand to be installed in the laboratory for proving out operating conditions.
The chief engineer is proud to say that "we are the only plant in Russia, and very likely in the CIS, which delivered a complete plant to the US. Individual machines used to be supplied but not the whole shop nothing can equal it".
Today the EZTM equipment operates in all continents exclusive of Australia. Vinogradov stresses that "our products are delivered to such industrialized countries as France, Germany, Sweden, the USA, Japan".
The total range of machinery and mills produced by EZTM have been developed by its own design and process engineers. "We are elaborating all designs or technologies. About 2195 inventors certificates and patents relating to the facilities of our make were implemented", such are the words Vinogradov used to show the science-intensive level of EZTM products. He supplements that seven EZTM specialists are "Distinguished Inventors of Russia". This rank means that a specialist has as least a hundred of inventors certificates put into production with a high economic effect.
During planned economy, the state dictated the specialization of an enterprise. Uralmash (the Uralian Plant of Heavy Machine-Building) manufactured cold mills, Novokramatorsk Machine-Building Plant (NKMZ), hot mills, EZTM, tube/pipe, heavy section and billet mills. Nowadays this division is violated as the chief engineer says, "everyone wants to make everything". Naturally, each producer strives to occupy the most profitable market niche but keen domestic competition remains to be expected.
|
EZTM products:
tube-rolling mills and electric-weld lines,
bar, section and wire rod mills,
oil film bearings for mill rolls,
part-rolling mills,
mineral processing, blast-furnace and other metal-producing equipment.
|
|
In the world market, Mannesmann Demag AG has been always considered the main EZTM competitor. Impartially speaking, Russian machine-builders capable to offer products of fairly high quality can work at a similar level. However, they are deprived of one of the main competitive advantages a possibility to credit the buyers.
"If we had this opportunity our market would be much wider", says Vinogradov explaining the problem on actual figures. The average interest rate of Russian bank credits is 22 percent. About a year is required to manufacture a big unit. That is, it is necessary to loan a large amount of money and freeze it for a year. Meantime, the customer will not agree to pay 22 percent more.
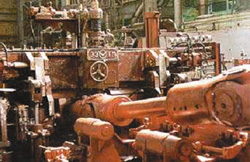 Piercing mill of ring-rolling line |
|
Vinogradov admits that to make a complete set of shop equipment for export supplies is not very profitable for machine-builders. Therefore EZTM prefers to sell individual mills and lines. Not so long ago ball-rolling mills were delivered to Germany and India. At present a rockright mill to roll circular and shaped tubes is being manufactured for India. It is the start of a new line of rockright mills.
Another interesting feature should be stressed here. EZTM is not a member of any industrial holding. It is a rather rare case for todays Russia. Certainly it is much more difficult for an independent enterprise to collect and manoeuvre funds. However, EZTM deals with the modernization of existing facilities and the construction of new projects.
While developing foreign cooperation, EZTM keeps in mind Russian consumers. An improved situation in the national steel industry, the modernization targets set by metals producers, the growing requirements of the oil and gas sector open up new markets to the machine-builders. 
|
|
|
|
current issue

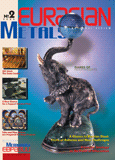
previous issue

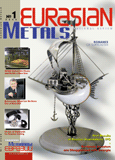
russian issue

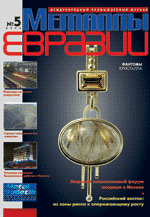
|
|