|
Magazine |
|
About |
|
SUMMIT |
|
Contacts |
|
Home |
|
|
|
|
| |
|
|
 |
#4' 2003 |
print version |
|
STILL A LONG WAY BEFORE THE IRON MOUNTAIN IS DEPLETED |
|
Vladimir Denisov
The daily output of run-of-mine ore and production of iron-ore concentrate and pellets again reached the design values at the Kachkanarsky Mine & Concentrator. The enterprise operated at this level prior to the start of the market reforms but later on the production volume drastically fell. A new rise began when Ural Mining & Metallurgical Company (UMMC) came to the management of the enterprise. The program for equipment and technology modernization was elaborated. Its fulfillment brought about positive results. Meantime Andrey Gruzdev, General Director, does not think this achievement infallible. "We face a lot of work to provide for stable and rhythmic operation in these conditions and bring the enterprise to the level of 45 million tons of raw ore mined each year", Gruzdev affirms.
he new management of Kachkanarsky Mine & Concentrator was induced to speed up the modernization because no steps in this direction had been taken for over a decade. The specified life of the major part of the haulage trucks and excavating machines already expired. Along with it, the deeper open pits substantially increased the haulage costs. In 1999 the dump trucks removed 10 mt and by almost 50 % more in 2002. By 2005 it is necessary to increase the haulage operations to 40 to 42 mt.
|
The local population knew about the ore outcrops on the slopes of the Kachkanar Mountain long before the Russians came to Ural. This mountain named ‘Iron Mountain by the mansi people (a local tribe) was believed to be sacred, and pagan deities were worshipped on its peak. In the 18th century Akinfiy Demidov, a famous manufacturer, made a try to buy the whole mountain but the natives refused to sell it.
Three and a half billion ton of ore containing 16 % of iron are concentrated in the Kachkanarsky group of iron-ore deposits. The raw material also contains vanadium and titanium. The bulk of the resources is two deposits, Gusevogorsky and Kachkanarsky. In 1930s their scientific study began. There had been no practice of commercial use of the lean ore similar to that in iron concentration. However, the research and pilot work on ore dressing and pelletizing of Fe-Va concentrate showed that this raw material could be used in iron and steel industry practice.
The Kachkanarsky Mine & Concentrator was built at the Gusevogorsky deposit in 1957-1963. Meantime the Kachkanar Mountain, comparable to the Gusevogorsky deposit in ore resources, is in reserve so far.
|
| |
|
By Gruzdevs words, the company already bought new dump trucks of higher capacity and 12 m3 bucket excavators. The modernization of the rail transport turned out to be more complicated. Due to well-known reasons, EL-20 diesel-electric locomotives that used to be the main haulage units on the local railways stopped to be supplied from East Germany. Similar trucks had never before been made in Russia. In 2001 the All-Russian Research Institute of Electric Locomotive Engineering (VELNII) and the Novocherkassky Electric Locomotive Plant got down to the development of a NP-1 electric traction unit for iron-ore mining. The Kachkanarsky Mine & Concentrator undertook the financing of the engineering and the manufacture of a prototype.
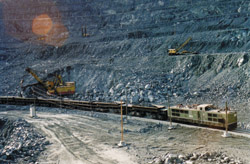 Kachkanarsky intagrated mill started upgrading its railroad transport |
|
At present the new machine is under testing. It consists of an electric locomotive and two motor dump-cars. It is capable of driving trains weighing over 2,000 metric tons in open pits on sections with a slope of up to 60 per mille with a speed of 25 to 30 km per hour. Such units will become the base of the loco fleet which will permit a much higher car turnover.
The enterprise still has limited finances therefore the investments are made in what will bring the maximum effect. Jointly with Uralmekhanobr Institute, a new technique of ore crushing using a free-drop concept in an impact-inertial crusher was tested and good results were obtained. The radically new crushers will make it possible to separate up to 40 % of dry tailings instead of 4 to 10 % with the old technology. Here the magnetic iron losses will remain at the same level as in wet tailings. Moreover, wet tailings are much more expensive in storing than dry tailings. Apart from it, dry tailings are more eco-friendly because they eliminate a necessity to consume a great volume of water.
There is another advantage. The new Titan-250 crusher already mounted at the concentrating plant produces cube-shaped crushed stones. This product, of high demand in the market of building materials, will bring a supplementary profit. Besides, impact-inertial crushers consume twice less power that old crushers.
A reduction of production costs becomes one of the key principles of the new management. It was this task that induced the construction of a captive plant of emulsion explosives. The new production operations reduced the cost of explosives almost thrice as their consumption was about 400 tons per week. In 2003 another production line was commissioned. In so doing, the plant is nearing the designed capacity permitting explosives to be sold to other mining enterprises.
Energy resources account for rather a large share in the prime cost structure of the products. Andrey Gruzdev points out that the enterprise operates in heavy climatic conditions of Ural and that is why it has to consume an additional amount of thermal energy. Airgas heating systems more efficient than conventional heat supply are being installed at the crushing and concentrating plants. Thus, the intermediate and fine crushing house of 450,000 cubic meter in capacity is heated by one 10 MW unit. Four units in total operate at the enterprise, and one more will be pit into operation by next winter. By the way, each waste heat boiler eliminates 100 tons of dust released with air emissions.
 Kachkanarsky integrated mill. Agglomeration |
|
Heavier mining conditions called for a more accurate estimation of ore deposits under development. Especially for this, as Gruzdev reports, a Surpac mining-and-geological software complex is being introduced. It will especially improve the reliability of assessing the quality of ore. Computer technologies are also applied in other sections of production operations. New iron concentration control systems make it possible to define the concentrate quality with high precision at any moment and take corrective actions in due time.
Andrey Gruzdev also claimed that the company intended to set up automated process control systems at all stages of ore preparation and dressing and to introduce a corporate information control system. It will require big investments but a short payback period. An automated system of energy monitoring alone will bring an annual saving of $800,000.
"Now when the Kachkanarsky Mine & Concentrator stabilized its operation, one can assuredly predict growth of its output in the years ahead", Gruzdev summarizes. The Kachkanarsky products, iron-vanadium pellets, are delivered to the Nizhny Tagil Iron & Steel Works producing naturally-alloyed high-quality steels. Now the demand of the works for the main raw material is fully met.
|
|
|
|
|
current issue

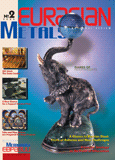
previous issue

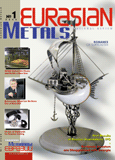
russian issue

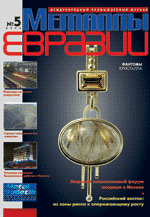
|
|