|
Magazine |
|
About |
|
SUMMIT |
|
Contacts |
|
Home |
|
|
|
|
| |
|
|
 |
#2' 2004 |
print version |
|
ÌÌÊ: CATCH-UP MODERNIZATION SUCCEEDS |
|
Yury Adno
ealistically, there is every reason to recognize the last year as the most successful for the development of Russias metallurgy in the whole period of ongoing market reforms. Such factors as the favorable foreign market conditions, steadily positive dynamics of the countrys improving economy as well as its political stability have contributed to the absolute growth of manufacturing metal products and raising companies profits. Today, the metallurgy accounts for about 7% of Russias total commodity output and for no less than 15% of the foreign trade currency earnings. Russian metallurgical enterprises meet about 90% of the domestic demand for metal products. Getting through the chaos of Russias initial stage of reforms and spontaneous upsurge after the 1998 state default, the Russian metallurgy has reached the level of sustainable development and it is now one of the most profitable as well as economically stable sectors of the national economy.
For many metallurgical companies the time has come to make a strategic choice and set goals of the long-term business development. The fundamental difference between the previous and current situations is the emergence of the relative surplus of the Russian economys financial resources, including the government as well as gold and foreign exchange reserves of the Central Bank, resources of the Pension Fund, commercial banks, companies, etc. Thus, conditions for the growth of investments are favorable. It is true that the country still lacks a reliable system of limiting financial risks that would cover the securities market and mechanisms of bank guarantees. That is why the investment policy of the leading companies is mainly based on using their own financial resources. It has to do, above all, with Russias largest integrated mills and companies: ÌÌÊ, NLMK, Severstal and EvrazHolding. These four majors account for about 80 % of the total steel production volume.
Magnitogorsk Iron & Steel Works (ÌÌÊ) stands out among Russian enterprises not only as the largest producer of rolled iron but also as a leader by the scale of its investment programs and their wide range. The high wear extent of its basic production assets and large share of outdated technologies prompted MMK to make massive investments in modernization.
By the available estimates, on the eve of the market reforms in 1991 the MMK equipment wear at some process stages reached 90%. The need for a radical reconstruction was already obvious in the late 1970s but its implementation was put off. As a result, it coincided with the process of reforming the national economy as a whole and that made the task more complicated. The general approach of the investment strategy provided for selecting projects of new construction and modernization of the available capacities on the basis of thorough analysis of market conditions, financial resources of the enterprise as well as technical and economic parameters of equipment to be used.
In the last decade ÌÌÊ has invested in production development about $1.7 billion. It managed to reduce the wear of the basic production assets down to 30 % on the average. To a larger or smaller extent the technical renovation covered all main and auxiliary process stages. The complex modernization of Russias largest steel casting facilities is especially impressive. By technological and technical capabilities this process stage came right up to the production level at the major transnational corporations. However, in order to consolidate market positions, MMK should still take a number of steps aimed at raising its competitiveness as the principal complex indicator of production efficiency.
The MMK investment program has the two main directions. The first one is connected to increasing price competition of metal products, i.e. to cutting down cost per unit at all process stages. The second direction is to increase making competitive products with the improved quality characteristics. Most production facilities, which have been or will be commissioned in the nearest future, are covered by precisely this direction (see the Table).
It is rather difficult to separate these two directions from each other in practice. The enterprise of the full iron and steel cycle is a single complex, where, as a rule, production potentialities of process stages, which are interconnected in consecutive order, should be balanced. For example, between 2004 and 2005 a transfer to a new technological chain will be made at the MMK steel casting process stage. Works are underway now to construct a new steel casting shop with two electric arc furnaces, out-of-furnace steel processing sets as well as two section and one slab continuous casting machines. As a result, the steel production capacity of the integrated mill will increase 2 million tones. Besides, the new shop will allow to cut down the use of cast iron and that, in its turn, will lead to reducing the need for agglomerate and coke. And, finally, increase of the steel casting capacities will significantly boost rolling potentialities.
Another example: with the commissioning of a new turbine generator MMK has become almost totally self-sufficient in energy supply. Taking into account the constant growth of prices for power resources in Russia it is not too difficult to appreciate the advantage of the integrated mill that has an opportunity to stabilize the share of energy consumption in products prime cost. Funds being saved this way are invested by MMK in projects to improve quality of metal products.
As a rule, the most attention in enterprises modernization projects is paid to the rolling process stage. MMK was known in the past as a maker of a wide range of rolled products using steel of mainly regular grades. That is why of special importance to the integrated mill has been the introduction of an equalizing blow unit, steel cycling degassing, cast iron desulfurization and finishing units as well as the furnace-ladle set in the oxygen-converter shop. These technologies allow to significantly increase the range of grades with the help of alloyed metal, which is used, among other things, to make sheet for the automotive, pipe-manufacturing and electrical industries. In recent years ÌÌÊ has almost doubled making dynamo and transformer steel that has contributed to a further consolidation of its presence in this market sector.
In the nearest future the MMK section rolling production facilities will be radically modernized. By its scale the project being implemented by the company Danieli has no match in Russia. It is planned to install three newest section mills with the total output of about 2 million tons of rolled stock a year.
The existing plans call for replacing heat-treatment nitric-annealing furnaces in sheet-rolling shop No.5 with the equipment that uses a more advanced technology of the hydrogenous annealing. This will allow to considerably improve the quality of sheet surface, reduce ecologically harmful discharges while the output of metal products will go up by 300,000 tons a year.
Metal products consumers are especially interested in developing production of coated rolled stock. In this respect the two investment projects have been implemented at MMK lately: the continuous hot galvanizing machine (HCGM) and double-stand reversing mill (with the production capacity of 800,000 tons) have been put in operation. The mill makes 0.35-to-2.0-mm thick and 800-to-1.650-mm wide sheet with high accuracy of geometry. For this purpose there is an appropriate system to adjust flatness.
At present, a polymeric coating unit with the annual production capacity of 200.000 tons, which has been supplied by the company VAL, is being assembled in the coating shop. The new line that is to be commissioned in July 2004 will allow to cover steel strip with polymeric coatings of the wide range and to get product with strong corrosion resistance. The market demand for such products that possess advanced consumer characteristics is quite high.
The modernization projects of MMK are being implemented with the participation of such world leading engineering companies as Danieli, VAI, SMS Demag, Techint, Ebner, Siemens and others. MMK is also cooperating with Russias Uralmash Plant to carry out some projects.
The radical reconstruction also includes production modernization works at two hardware-metallurgical plant (MMMZ) and calibration plant (MKZ), which are integrated in MMK JSC. The main goals of this modernization are to improve quality and diversify their products. The MMMZ plans provide for mastering production of powder wire, the A500C class reinforcement, wire with bright zinc coating. In its turn, MKZ plans to start making zinc-coated ropes, reconstruct furnaces for annealing calibrated rolled stock, modernize the length cutting unit for hot-rolled products and put in operation an automated line of rod etching.
Any competitive metallurgical enterprise should correspond to high ecological standards. Expenses on ecology account for a considerable share of all investment projects at MMK. Last year the complex of nature conservation measures with the total cost of $12.7 million allowed to lower the index of discharges per one ton of steel by 7.3 %.
In April 2004 the Magnitogorsk Iron & Steel Works has received certificates of conforming with the system of quality management by the ISO 9001:2000 standard. The certificates have been given because of results of the supervision and certification audit conducted by auditors from RW TUV. The complex check-up has proved that one of the Russian steel industrys leaders not just completely fulfils requirements of the quality management system to enterprises certified earlier but is also practically ready to extend the certification sphere. In particular, the case in point is the production of agglomerate, cast iron, hot-rolled coils, sheets, galvanized steel and some other kinds of metal products.
|
|
|
|
|
current issue

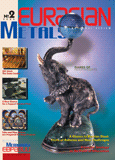
previous issue

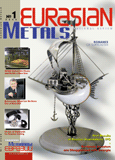
russian issue

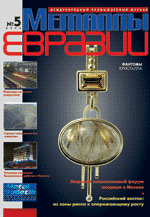
|
|