|
Magazine |
|
About |
|
SUMMIT |
|
Contacts |
|
Home |
|
|
|
|
| |
|
|
 |
#4' 2004 |
print version |
|
DAY OF METALLURGIST ON BORDER BETWEEN EUROPE AND ASIA |
|
Andrei Karunos
hen the Magnitogorsk Iron & Steel Works (MMK) is described, the largest, the strongest and other similar superlatives are often used. And there is nothing unusual about it. As todays image-makers would say, the founding of this enterprise was one of the most striking events in the Soviet epoch. This enterprise became known in the countrys history under the legendary name ‘Magnitka, which is still used today along with the companys official title and which is present in the name of the town, Magnitogorsk, that was built near this integrated mill.
This year Magnitogorsk marked its 75th anniversary. The ÌÌÊ leaders invited a group of reporters to take part in celebrating the towns jubilee and the Day of Metallurgist, which Russia traditionally observes every year, on the third Sunday of July. It gave them a good reason to see for themselves what is going on at Magnitka today and to ask the companys officials a few questions.
"We live in Europe but work in Asia", joke employees of MMK. And it is true: the town of Magnitogorsk and the mill are located on the different banks of the Ural river with the geographical border between Europe and Asia running along its bed.
MMK impresses with its size, in the first place. It occupies almost 12,000 hectares, 7,000 of which are taken up by the production facilities. In 1989 the mill reached its maximum capacity of 16 million tons of steel that could be compared with the annual steel production volume in an average European country. The current indicators at MMK are somewhat lower: in 2003 it produced 10.7 million tons of rolled stock and in 2004 the mill plans to make 10.2 million tons. However, even this amount is sufficient to remain the largest enterprise of Russias steel industry and, according to Metal Bulletins rating, to rank 16th in the world. It is expected that in the near future its annual production will be growing up and by 2007 it will reach 12 million tons of rolled stock.
Rafkat Takhautdinov, the deputy general director of MMK for production and construction, is satisfied with the companys results. By the volumes of making cast iron and steel the mill is approaching the upper limit of the available production capacities. Still, there are some capacity reserves at the rolling process stage. As Rafkat Takhautdinov points out, the enterprises personnel is successfully accomplishing the task of not just raising the volumes but also of making products that are in the highest demand in the market.
In Takhautdinovs words, MMK has solid competitive advantages resulting from the reduction of production costs and growth of making products at the final process stages. In order to maintain these advantages, the mill is undertaking a large-scale reconstruction. In 2004 investments in the MMK basic production facilities will amount to $400 million. As the deputy general director says, there will be no reduction of financial investments next year. "We are seeking to raise quality and get a wider range of products", notes Rafkat Takhautdinov. And reporters had a good opportunity to see it for themselves.
Reporters were invited to attend the formal start-up of a polymeric coating unit, which became the last link in the technological chain that includes a continuing casting machine in the converter shop (by the way, one of the worlds largest, with the annual production volume of over 10 million tons of steel), a reversing cold-rolling mill in sheet-rolling shop No.5 and a continuous hot-dip galvanizing unit. The polymeric coating unit allows to cover the surface of cold-rolled galvanized sheet with layers of polyvynylidene fluoride, polyester as well as with paintwork. The unit was shipped by Voest-Alpine, the old partner of MMK. The total cost of the project is 30 million euros. Its design productivity amounts to 200,000 tons of rolled stock a year. High merchantable properties of coated sheet are obvious. The economys construction sector is sure to become its chief consumer (about 60% of supplies). A considerable portion of supplies will go to companies that make home equipment. As is expected, sheet with polymeric coating will also be demanded by automotive plants that are traditional consumers of cold-rolled sheet produced by MMK, which has recently started supplying them with galvanized sheet as well.
The complex reconstruction of sheet-rolling shop No.5, which makes cold-rolled sheet, has been going on for several years now. According to estimates, it will significantly consolidate MMK positions in the automotive industry market and will yield an economic effect totaling $69 million. The shop has already had a two-stand reversing mill with the production capacity of 800 million tons of sheet a year. The start-up of new as well as reconstructed facilities in the shops heat treatment and pickling bay has become the next reconstruction stage. The transfer to the strip descaling technology with the help of hydrochloric acid (not sulfuric acid, as before) will allow to annually make 3.2 million tons of cold-rolled sheet of the first surface group.
The MMK management is persistent in implementing the program to liquidate outdated and inefficient capacities. There are still open-hearth production facilities at the mill but they are being replaced with electric-arc furnaces having continuous casting. The Day of Metallurgist was marked in the open-hearth shop by the start-up of the first section continuous casting machine supplied by Voest-Alpine and a furnace-to-ladle unit. As Rafkat Takhautdinov says, "with commissioning the second section continuous casting machine the mill will completely do away with the technology of casting steel in molds".
In his words, "a contract has already been signed to construct two electric arc steel-melting furnaces with the capacity of 2 million tons of steel each". The first one should be commissioned in November 2005. Works on constructing electric arc steel-melting facilities are closely connected with the reconstruction of the rolling process stage. Under the contract signed last year the company Danieli should provide Magnitka with three section mills having the annual production capacity of 2 million tons. As a result, half of electric steel will be used in future by these production facilities. Another 2 million tons of electric steel are intended for sheet-rolling shop No.4, which makes semi-finished rolled products for round billets.
Rafkat Takhautdinov puts a special emphasis on a link between reconstruction plans and the MMK marketing strategy. He compares the metallurgy with litmus paper: if the demand for metals is growing up, this means that the countrys economy is developing successfully. "Our task is to provide the supply side of the supply-and-demand ratio and, at the same time, to be competitive and have a normal economy", Takhautdinov says.
Gennadi Senichev, the MMK deputy general director for finances and economy, believes that the business is going quite well. In 2004 the profitability is expected to amount to 50%, the profit is planned at $1 billion.
Recently ÌÌÊ has reached a kind of landmark: the ratio between export and domestic shipments has changed and now the Russian market accounts for over 50% of its sales. Deputy general director for marketing Alexander Ushakov has called this fact "the key result of the first six months". He considers the Russian market to be "strategically important" for MMK and points out with satisfaction that all the main industries, including such consumers as the automotive and pipe industries, have increased purchases of steel from Magnitka. The prospects for Russias steel consumption let the MMK management predict that in 2005 supplies to the domestic market will amount to 55% of the mills total production volume. At the same time, managers from MMK do not intend to yield positions that the enterprise won in the world market. They remind that Magnitka products are shipped to 70 countries with almost half of its export going to Southeast Asia.
Like other major steel companies (Severstal, EvrazHolding), the Magnitogorsk Iron & Steel Works has showed its interest in production of large-diameter pipes, the most complex and, at the same time, the most attractive segment of the Russian market.
" I think that making pipes is the most promising direction for the steel industry since the Russian territory is literally entangled in a web of pipelines", says Takhautdinov.
Eurasian Metals has already reported on prospects for creating a pipe alliance between MMK and the ChTPZ-Group as well as on the position in this respect taken by Vitaly Sadykov, the general director of the ChTPZ-Group (ÅÌ, No.1, 2004, p.26). This time, in response to our request, Magnitkas managers expressed their opinion on a possible alliance with pipe companies. Here is what Rafkat Takhautdinov had to say:
"We are studying the project to construct a plate mill at MMK. Such a complex will cost no less than $800 million. This project can be implemented in cooperation either with the ChTPZ-Group or with the Volzhsky Pipe Plant, which belongs to the Pipe Metallurgical Company. There is also another project. Having examined the world experience in this respect, we have come to the conclusion that MMK can make semi-finished rolled products for large-diameter pipes at its 2500 mill of hot rolling, if it is reconstructed. In other words, by investing less funds (by four or five times), we will be able to start making strip coils with the thickness of up to 25 mm, which can be used for manufacturing double-welded pipes at that same ChTPZ". MMK is prepared to implement this program in two years.
At the end of the discussion one more important question was raised: the problem of providing the mill with supplies of iron ore and coal. As is known, MMK is Russias only major maker of steel, which does not have a sufficient raw material base and, thus, is forced to buy most of ore and coal in free market. About 70% of ore is supplied by the Sokolovsko-Sarbaisky Mining Production Association from Kazakhstan.
Magnitka managers do not deny that the enterprise is experiencing difficulties with the iron-ore raw material and coke but there is a program to improve supplying raw materials. As Rafkat Takhautdinov says, today MMK extracts 10% of all iron ore being consumed. There are plans to further increase this amount to 15% through developing iron-ore fields in the neighboring region of Bashkiria, among other ways. But, as Takhautdinov notes, it is still too early to consider the question of acquiring iron-ore producing companies and integrating them in MMK JSC.
As for coal, the situation in this respect is getting better as well. Magnitka has made a major acquisition: it has bought the Uregolskaya mine, which is located in Kuzbass, Russias largest coal basin. As the MMK public relations office reports, coal reserves at this mine amount to no less than 2 billion tons. At present, when prices for main kinds of raw materials and energy resources are growing, this step will allow the leader of the steel industry to maintain its policy of reducing production costs while keeping competitive advantages.
Photos:
Section continuous casting machine supplied by Voest-Alpine
Polymeric coating unit
General view of MMK
Diagrams:
MMK share of Russias steel production volume
Dynamics of growth in making main types of products
|
|
|
|
|
current issue

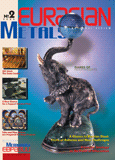
previous issue

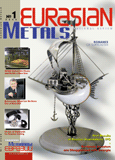
russian issue

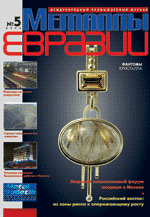
|
|