|
Magazine |
|
About |
|
SUMMIT |
|
Contacts |
|
Home |
|
|
|
|
| |
| |
 |
#1' 2005 |
print version |
|
NTMK: SCEPTICS DO NOT COUNT |
|
Andrei Karunos
here have been changes in the leadership of the Nizhny Tagil Iron and Steel Works (NTMK) integrated in the EvrazHolding Group: Alexei Kushnarev, formerly chief engineer of the enterprise, has become chief executive officer. In the interview with Eurasian Metals, one of Kushnarevs first, he talked about the program of the enterprises re-equipment.
Reminding that NTMK is one of the leading and dynamically developing enterprises of Russias steel industry, Kushnarev cites some preliminary figures related to results for 2004 (according to the Russian Accounting Standards): the enterprises gross profit will increase 2.4 times and will amount to about 21605 million rubles, while its net profit will go up 3.3 times and will equal aboutî 13338 million rubles.
In Alexei Kushnarevs words, the modernization of the integrated mill started with its energy facilities. After new turbogenerators and turbocompressors were installed, NTMK achieved stability in power supply. "Today we produce half of needed electric power and by 2008 we are planning to bring the share of our own electric power to such a level that the enterprise will be able to maintain production even in cases of emergency outages of external networks", says Kushnarev.
For an enterprise, which just a few years ago had one operating blast-furnace and undemanded products, the program of technical re-equipment allows not only to modernize the outdated production facilities . "The most important thing is that by fully implementing this program we will make NTMK highly competitive on the market", notes the CEO, He points out that already today there is an enough potential to regulate production and quickly change the range of products according to market needs.
Kushnarev says that the present stage of the technical re-equipment program is focused, above all, on the steel-melting process stage . The major task is to close down the open-hearth shop as inefficient and ecologically harmful, while, accordingly, increasing steel production in the oxygen-converter shop bringing its productivity up to 5.2 million tons year-on-year. As the CEO notes, just recently there were enough skeptics at the enterprise convinced that it would not be possible. But today NTMKs main partners Voest-Alpine, SMS-Demag and the Russian designing company Gipromez have already submitted necessary calculations.
The full reconstruction of the steel-melting production means modernization of the converter sector and billet continuous casting machines. Four converters are to be replaced. Alexei Kushnarev believes that replacing two converters a year is quite realistic. "If we sign contracts in 2005, then in mid-2006 we can replace one converter, two more in 2007 and the last one in the first half of 2008", he goes on saying.
After the reconstruction is completed, it will be technologically possible to pour out steel, which will be produced by the converter section, at the available continuous casting machines as well. However, in Alexei Kushnarevs opinion, it would limit the range of products. For example, continuous casting machine No. 1 produces transport-designed metal (rails, wheels) as well as round billets. Nevertheless, NTMK cannot satisfy needs of customers asking for continuously cast billets to make axles for wheel pairs. "We have completely exhausted the resources of this machine and that is why we would like to reconstruct continuous casting machine No.3 so as to make it produce this part of the products range", says the CEO.
Kushnarev admits that reconstructing continuous casting machines can be done in parallel. "We want to start reconstructing the most outdated one, machine No.2, in 2005 and complete it in two years. The modernization of machines Nos, 1 and 4 is to be finished by 2008", he says.
Reconstruction works are underway on the open-hearth and by-product coke production facilities at NTMK, where the machinery capacity is being increased and where a switch over to new, ecologically cleaner technologies is underway. "You can wear a white shirt when coming to see open-hearth furnace No. 6, to climb up to the very top but the collar of your shirt will still remain clean", insists Kushnarev. In his words, after reconstruction open-hearth furnace No.5 will be the same. Kushnaver says that there are no such open-hearth complexes anywhere else in Russia.
In 2005 the enterprise is going to master machinery commissioned last year and, in particular, the new line in the tyre shop. As the CEO says, the technology of making mass products, which are in the daily demand, is being worked out The enterprises main customer, the company Russian Railroads (RZHD) would like to get a new type of wheels with a higher strength.
On the whole, NTMKs head highly appreciates the level of cooperation with the chief consumer of the transport-related metal. Although RZHD remains a monopoly in the field of railroad shipping operations, its new leadership has changed the attitude towards steelmakers and other partners trying to maintain the dialogue in the spirit of constructive cooperation. "We have got an access to the internal information of the railroadmen concerning the quality of our products. And it makes sense: how can we perfect the quality not knowing reasons for our wheels failure?", he says.
The major rival of NTMK in this market segment is Vyksa Steel Works, the United Metallurgical Companys enterprise. This plant has already introduced an installation to make wheels of a higher strength and put out the first trial batch "They are ahead of us in this respect", admits the CEO. "But we are not going to force events and we keep implementing our own program according to the approved timetable We have just installed a pressing-rolling line. The next stage is the sector of thermal treatment, which improves wheels quality characteristics", says Alexei Kushnarev.
Reconstruction of the rail production is to start not earlier than in 2007. It will impossible to do it in parallel with other works: the amount of needed investment is too high. Besides, the main consumer apparently is not ready to change over to using rails 100 m long. "We asked them and received a rather evasive answer. That is why we concluded that today Russian railroadmen are not prepared for 100m rails and that they will be ready to use them not earlier than in 20 years from now" believes Kushnarev. In his opinion, in order to do that RZHD will need to replace all track-laying equipment.
Nevertheless, NTMK has a well-elaborated and approved concept of developing the rail production.
And the last question is about NTMKs attitude towards the present tumult on raw material markets Alexei Kushnarev believes that it does not hurt NTMK since the enterprise is part of the vertically integrated Evraz Group, which is well-provided with raw materials: the Group includes Ural ore-mining enterprises Vysokogorsky and Kachkanarsky ore mining and processing mills. Although other steemakers worry is well-grounded. In conditions of high demand raw materials (agglomerate, for one) are still being exported from Russia Thus, says Kushnarev, "objections of steelmakers, their appeals to the government are absolutely just and understandable".
Profile:
Alexei Kushnarev
CEO of NTMK. Born inî in 1960. Has a diploma of metallurgic engineer. Graduated from the G. Nosov Magnitogorsk mining and metallurgical Institute. Made a career from a roller to the chief rollerman at the Magnitogorsk Iron & Steel Works. In 2002 through 2004 was NTMK chief engineer. Has a scientific degree. Author of scientific articles and inventions in technology of roll-mill production.
|
|
|
|
|
current issue

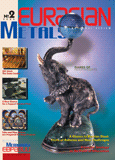
previous issue

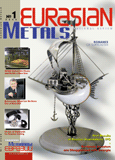
russian issue

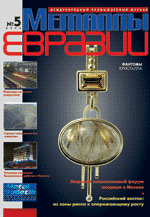
|
|