|
Magazine |
|
About |
|
SUMMIT |
|
Contacts |
|
Home |
|
|
|
|
| |
|
|
 |
#3' 2005 |
print version |
|
INVESTMENTS IN PIPE SECTOR ARE FULLY WARRANTED |
In an interview with Eurasian Metals president of the United Metallurgical Company (UMC) Anatoly Sedykh expresses his confidence that in the coming 4 to 5 years the situation on the Russian market will remain favorable for pipe makers. His optimistic view is based on both marketing forecasts and recent successful production results at UMC itself. |
Anatoly Sedykh
urasian Metals: Lately, the Russian steel industry has been developing quite successfully. How well do the pipe-making sector and, above all, your company look against this background?
Anatoly Sedykh: UMC has been positioning itself on the market as a steel company, not as the pipe-making one. In addition to pipes, we are making a wide range of other metal products: railroad wheels, rolled stock, cast iron, ferrovanadium, vehicle springs, etc. The business diversification is our solid advantage. It was also proved last year, which was quite complicated for pipe makers, while conditions on the market of rolled stock, coke, ferrovanadium, railroad wheels were more favorable. But, anyway, pipes in our business undoubtedly take up the leading position. The financial results show this too. Last year proceeds of UMC went up 59%, up to $1.43 billion, while the profit doubled, up to $186 million. More than half of this growth was provided by the companys pipe-making plants, i.e. the Vyksa Steel Works (VMZ) and the Almetyevsk Pipe-Rolling Mill. What is more, VMZ that produced 876,003 tons of pipes achieved the best production result among Russias seven largest pipe-making plants.
EM: What events would you call the most important to your company?
AS: Among the last years events I would single out the completion of pipe supplies for the Sakhalin-1 and Sakhalin-2 projects. I regard as a big achievement our operations under these projects, in which the worlds famous corporations, such as Shell and Exxon Mobil, are participating.
The past year was the record one for UMC with respect to investments: over $190 million. The major part of them was connected with implementing the 1,420 project: that is the project to set up a complex of making trunk pipes with a diameter between 530 mm and 1,420 mm at the Vyksa Steel Works. We accomplished a large volume of works: the main equipment was supplied and assembled, the shop of electric-welded pipes was reconstructed, another section of preparing sheet for both the operating and new lines was constructed.
The situation could have been more advantageous to UMC and other participants of the market, if there were no growth of prices for steel and expansion of Ukrainian makers of pipes that sell their products in Russia for dumping prices. Besides, for a long time the prospects remained uncertain with respect to the start of constructing large pipelines. This restrained the increase in demand for pipe products in Russia.
EM: How did the rise in prices for steel rolled products influence your relations with the main partners, i.e. your suppliers and customers?
AS: This problem was especially serious last year. Consumers were not ready for such a steep jump of prices. Sometimes the metals share accounts for over 70% of the pipes prime cost and, thus, its becoming more expensive had a direct impact on the price for the end product. Budgets of oilmen and housing and communal services were based on the entirely different level of prices; that is why they could not buy pipes in the planned volumes. As a result, the market of pipe products went down sharply in the fourth quarter.
Today, the problem is not so acute. Consumers realize that high prices are not the consequence of someones rush for surplus profit but an objective result of the increased global demand for the metal, especially in Asia. What is more, this current year prices are going up by moderate rates amounting to several percentage points (not as last year, when they doubled) and, so, the main consumers are not worried that much, particularly because prices for oil and gas are quite high as well.
EM: There was a number of attempts undertaken in Russia to set production of pipes with the diameter of 1,420 mm for trunk gas pipelines. Could you sum up the results of this "projects competition", in which your company turned out to be the leader?
AS: We managed to implement the 1,420 project in 2 years and that is the record short time. And to a large extent it was the achievement of our own specialists as well as our partners and suppliers: the Russian and foreign companies, which strictly observed the schedule and supplied equipment for a new mill in proper time.
We have invested $172 million in this project and we hope that it will recoup itself in 3 to 4 years. Within the existing production structure a unique high-tech line has been constructed at the Vyksa Steel Works; it is capable of making all the range of pipes with a diameter between 530 mm and 1,420 mm, with a wall thickness of up to 48 mm as well as with inside and outside anticorrosion coatings.
At present, there are two lines in operation at VMZ. One of them, which was commissioned in 1993, is designed to make pipes with a diameter between 508 mm and 1,020 mm and the second one, our new project, is capable of making pipes with a diameter from 530 mm to 1,420 mm. Both lines are operating at the same production site. Simultaneously, the infrastructure of the enterprise and labor resources are now used more efficiently. The aggregate capacity to make pipes with large diameters now exceeds 1.5 million tons year-on-year, including between 450,000 and 500,000 tons of pipes with the diameter of 1,420 mm.
As far as "the projects competition" is concerned, in my opinion, there has not been and there is no such a competition. In Russia, besides UMC, only Severstal is implementing a similar project. I think that in the coming years the market of large-diameter pipes will steadily grow up and that there will be enough space for all.
EM: What is your confidence based on? What volumes of the 1,420-mm pipes is their key consumer, Gazprom, ready to buy?
AS: Pipes from the VMZ new line fully meet requirements of Gazprom and Transneft, their main consumers. These pipes are designed for used in trunk oil and gas pipelines, mainly, with the diameters of 1,067mm, 1,220 mm and 1,420 mm. Besides, the new line is capable of making thick-walled pipes with a smaller diameter for on-shelf pipeline projects in accordance with the highest standards. Today, this is a very promising and expensive segment of the market.
There is an agreement of intentions in effect between UMC and Gazprom: in 2005 the gas company will buy 100,000 tons of pipes from us. I think that in the nearest years Gazproms need for pipes will go up considerably. The length of Russias gas pipelines amounts to 153,000 km, a significant part of them is worn out and requires repairs. Also, there is a necessity to develop new fields and construct new pipelines. For example, preparatory works are underway now to construct the North European gas pipeline. Transneft also has major plans. One of Russias largest projects is the construction of an oil pipeline from Eastern Siberia to the Pacific Ocean (Taishet-Nakhodka). Only the first stage of construction will require $6 billion in investments, while the steel intensity of the oil pipeline is estimated at 2.5 million tons. The existing plans provide for using pipes from the new line of VMZ. Works are continuing so as to extend the Baltic pipeline system for raising oil pumping to Europe. And this will also increase the markets capacity for our products. Besides, we are discussing a possibility to supply large-diameter pipes with foreign partners as well.
EM: How is the scheme to provide the VMZ new line with wide sheet being formed?
AS: Russian suppliers include our strategic partner, Severstal, which annually provides us with about 700,000 tons of strip. Quality requirements with respect to new trunk oil and gas pipelines are constantly on the rise; that is why we are seeking more suppliers. We have held talks on buying sheet with German, Japanese, Korean companies and we have already received the first trial consignments.
The new line at VMZ is designed to make both single- and two-weld pipes. If consumers want to get two-weld pipes, then, in this case, the range of our suppliers will expand: we are ready to work with the Ukrainian steelmakers Azovstal and the V. Iljich Mariupol Iron & Steel Works.
EM: Your companys plans to develop its own making of steel have become known. What details of this project can you share with us?
AS: In March UMC and Danieli signed a contract to supply equipment for a future foundry-and-rolling complex, which is planned to be constructed not far from VMZ. It will produce hot-rolled coils for pipes with a diameter of up to 530 mm. In the nearest three years we intend to invest over $500 million in this project. The complex will include an arc steel-melting furnace, furnace-ladle and vacuumator, thin-slab continuous casting machine, tunnel furnace and wide-strip mill of continuous hot rolling. These high-tech production facilities will be able to make 1.2 million tons of rolled stock year-on-year with less than 1,000 workers operating them. Scrap will be used as the raw material. It is abundant in this region (Nizhny Novgorod), where many metal-working enterprises are located.
We need this project not only to reduce the dependence on price conditions on the market of steel rolled products but, above all, to get a guaranteed quality of sheet. Production of modern pipe requires more often rolled stock with unique properties, which our steelmakers cannot ensure as they focus their efforts mainly on making rolled products of the average quality.
EM: Quality requirements with respect to pipes are getting tougher by other parameters as well. How does your company react to them?
AS: We are trying to operate in advance, so to say. For example, the new VMZ line can make pipes, which are capable of withstanding pressure of up to 250 atm, while most pipes in Russias functioning pipelines are designed for a pressure between 100 and 120 atm. We take into account long-term plans of oil and gas companies, which are moving more and more operations to remote regions difficult of access, such as Yamal, Eastern Siberia, etc. Pumping compressor plants are constructed at considerable distances from each other and, thus, the need emerges to use a higher pressure in pipelines. And we are ready to make pipes for such pipelines.
There is a growing demand for pipes with anticorrosion coating. Today, the coating-applying line that is in operation at VMZ is loaded by 100%. In 2005 we are to commission two new lines, one for pipes with a diameter between 57mm and 530 mm and the second one for pipes with a diameter of up to 1,420 mm.
I would like to remind that the participation in the Sakhalin-1 and Sakhalin-2 international projects gave us a unique experience and contributed to our serious engineering development. VMZ passed the certification procedure according to requirements from the worlds leading oil companies.
EM: Is there a possibility of compromise in relations between Russian and Ukrainian pipe makers or a tough competition till the full victory will take place?
AS: We are against a tough confrontation with our neighbors and we are ready to agree to a reasonable compromise. We recognize that their presence on the Russian market is predetermined historically: Ukraines pipe industry was established in the Soviet times and it was aimed at meeting needs of the oil-and-gas complex of the whole USSR. But today we are working on unequal conditions. Ukrainian pipe makers have tax privileges from their government and, so, they can use dumping. By contrast, the Russian pipe industry found itself in the intricate situation. At present, Russian companies are implementing large investment projects, while the Ukrainian dumping restricts possibilities for their recoupment. That is why I think that in this respect we have the right to count on protection of our interests by the Russian government.
EM: What is your forecast of the Russian pipe production in the foreseeable future?
AS: In my opinion, besides the market growth because of Russian pipeline projects, we will be able to get more customers abroad. Today, the worlds energy system is undergoing changes. In the past, the Russian fuel complex was directed mainly toward Europe. Now other directions are emerging and that is countries of Southeast Asia, China, Japan. These regions are experiencing a quick growth of the industry as a whole and the construction industry in particular, Thus, a rapid increase in consumption of energy resources is expected. In terms of efficiency, trunk pipelines are an optimal way of transporting oil and gas. That is why I am sure that in the nearest years the demand for our pipes will be just rising.
|
|
|
|
|
current issue

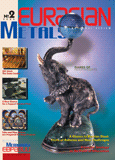
previous issue

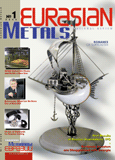
russian issue

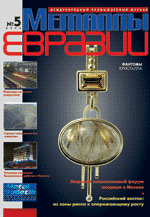
|
|