Yevgeny Khokhlov
Muruntau is the biggest but not the only source of gold in Uzbekistan. Considerable reserves of the precious metal are concentrated in the ores of the Kokpatas, Daugyztau, Myutenbay and other de-posits. All these sites are being mined by one enterprise: the Navoi Mining & Metallurgical Com-plex (NMMC), the main Uzbek gold producer. The technogenic stock accumulated for the years of the operation of the Muruntau mine are processed by heap leaching by the Uzbek-US Zarafshan-Newmont joint venture. It must be noted that the geological prospecting works in Kyzyl Kum are still going on rather ac-tively. The results permit a further build-up of the reserves. However, it is unlikely to rely on an-other Muruntau to appear in this region: as is testified by statistics, only one unique deposit falls on hundreds of ordinary ones. That is why the Uzbekistans outlook in the world gold market depends mostly on the intensification of gold mining operations and the application of innovative technolo-gies for a higher rate of gold recovery from the ore to be achieved. When assessing the results of the operation in the first decade of existence of the country as an in-dependent state, its general director Nikolai Kuchersky said the following: «The main thing done during this period was the modernization and the re-equipment of existing enterprises. The Navoi Complex increased gold output by 1.5 time, with the entire build-up re-ceived mostly due to more productive up-to-date equipment, advanced technologies and new re-search developments». In his interview to Eurasian Metals, Nikolai Kuchersky gave a detailed description of the essence of the modernization which permitted the complex to be fully re-equipped within 2 to 3 years: «In the beginning of the 90s in the Muruntau open pit there were only 110-ton BELAZ (trucks made by the Byelorussian Automobile Plant), whose failures used to occur at a depth of 150 to 200 meters, thus disrupting the whole production cycle. Frankly speaking, this truck in engine rating, cooling system and other design parameters was not fit for operation in our conditions. An immediate tran-sition to a different process chart was required then. The first step was made when a cyclic & as-sembly-line process of lode rock mining was introduced. Owing to it, the load of haulage equipment was reduced but the problem was not yet settled. In 1993 we bought first 20 Euclid trucks and in the following two years 60 Caterpillar dumpers. We had to spend a lot but, in my opinion, it paid for itself many times over. Although today the work is on already at a depth of below 400 m, our unit production costs remain invariable and even decreased in some items.
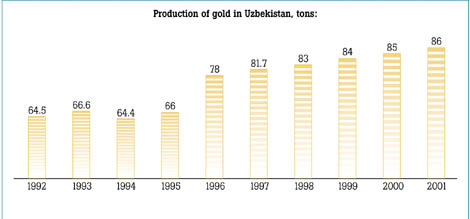
Nowadays in the Muruntau open pit Hitachi, Caterpillar, Orenstein & Koppel 1720 m3 bucket hydraulic shovels, together with CAT 785B 136-ton and R-170 dumpers, operate. The operation in difficult mining and climatic conditions proved high reliability of this equipment. It is of interest to note that all dumpers (78 units in total, bought within nine years) are still in operation though, ac-cording to makers norms, a part of this machinery could already be written off. For example, a normative life of the engine before overhaul is 12,00015,000 engine hours while here they oper-ate 20,000 engine hours and more. As is noted by Petr Shemetov, Head of the Muruntau Mine, «in this way we render good promotional advertising to the makers» because «not a single big open pit in the world managed to reach similar records». The great credit for it is due to NMMCs specialists who are skilled in operation, maintenance, reclamation and keep constant contacts with the makers. The replacement of the truck fleet may begin in 2003, and it will take place with a simultaneous rise of load-carrying capacity. This is the opinion of Viktor Sytenkov, Chief Engineer of Central Ore Division which incorporates the entire gold-producing complex in Zarafshan. He also claimed that its is planned to use 2630 m3 bucket shovels, consequently, the transport load will grow, and 190200-ton dumpers will be required. It is very likely that Caterpillar will be chosen again. »We examine many offers», Viktor Sytenkov clarified, «but we do not feel there is any sense in transition to a new type of trucks. We have been known Caterpillar for many years. Its equipment bulldozers, graders, loaders have been working in the pit since the start of the mining operations. Besides, the company submits a sheet of interchangeable parts for any type of its machinery while the problem of unification is urgent to us». In future the company would like to reach a higher rate of unification of operating equipment in consideration of the plans of mining other gold-bearing deposits and the expansion of output of phosphorites.
Nikolai Kuchersky
belongs to that generation of specialists who created the production complex in the Kyzyl Kum desert. Here he has been working since 1961 and therefore knows the capabilities of the Navoi Mining & Metallurgical Complex to perfection. In 1985 he headed NMMC when became a director third in sequence.
He will be 65 in June. Despite a rather adult age, he is especially acquisitive of new in, above all, what relates to engineering ideas and research developments. Brave enough to undertake experi-ments conjugated with high costs in the conditions of large-scale production operations. With great experience, knowledge and high personal account, he thinks it necessary to listen to different opin-ions, even if they may be disputable. He is on friendly terms with foreign colleagues, among them, managers of companies noted throughout the world.
In his rare rest hours he tries to go to the country. He knows a lot of picturesque places in the desert where one can be a tourist, a fisherman or a hunter. His binding companion in these trips is photo camera. Keen on photography since childhood. Another inclination of similar passion and age is cars. Excellent driver and fitter. Willingly takes the steer during his frequent long business travels for his chauffeur to have a rest.
| |
| |
|
The reconstruction of the Kyzyl Kum gold-mining complex is not restricted to the replacement of equipment and machinery. Its modernization shall be considered as an integral process enclosing the whole production cycle, from blasting till output of finished gold ingot. As is stressed by the companys specialists, the main target is a continuous build-up of gold output, keeping an adequate production profitability rate in the conditions of actual pricing. For this task to be fulfilled, the most up-to-date technologies are applied, with many of them developed by the Navoi Complex itself. Here is what was told by Nikolai Kuchersky about the results of this enormous work. «At our main enterprise the Muruntau mine we established automated process control systems (with further implementation at other industrial units). They already brought about a saving of $200300 million due to an optimal flow chart of mining and a guarantee of output to be kept at a profitable level. For instance, if the gold price falls we immediately adjust the operation in the ore mining area. And all this is done at a sockdolager where over 20 large-capacity shovels, tens of 140 to 190-ton dumpers, drill rigs, conveyers and other equipment are in continuous operation».
A billionth cubic meter of lode rock was delivered from the Muruntau mine in 2001. This record figure vividly demonstrates the scope of the work executed for more than 35 years of the operation.
Year after year the mining conditions of the Muruntau deposit deteriorate. The pits are deepened, the haulage distance grows. All this involves an inevitable increase in costs. From the other hand, a substantial drop of world gold prices occurred. None the less, the technologies applied in the mine make it possible to effectively work in this situation. The general director of NMMC sited the fol-lowing comparison. «According to the project of the 4th stage of mining, it was necessary to excavate 1200 million m3 of lode rock, as per a conventional process. In view of our ore flow control system, we claim: all the gold will be taken out, with the excavation amounting only to 580 million m3, that is, there will be no need to haul more than 600 million m3 of gangue from a 0.5-km depth over a distance of 8 km». An important link in process control became a global positioning system (GPS) based on computer technologies, satellite navigation and communication. The system implemented with the participa-tion of a Russian company (INTEGRA JSC) performed very well. It permits an actually minute-by-minute control of operation of the excavating-and-haulage complex without any delays or down-time. It is supplemented with another system monitoring the composition of ore grabbed by the shovel and transported by the dumper. It is a know-how of the Navoi Complex and not applied anywhere else as yet. For the time elapsed the development concept of the Zarafshan gold-mining complex has undergone changes. If previously the target was to increase ore output now it proved more profitable to be en-gaged in dressing and downstream processing. The reconstruction is going on at the extractive met-allurgical plant, a more productive equipment is being installed in order to involve extra-register ore in processing. The orientation to possible use of ore with low content of gold was taken as a promising direction from the start of the deposit mining. With this view in mind, separate mining and storage of com-mercial and extra-register ores were carried out. Now the prepared stock allows larger gold output without intensification of stripping operations. The extractive metallurgical plant in Zarafshan processes 70,000-72,000 tons of ore per day. Only 70 m3 of gold-saturated solution which is electrolyzed are produced from this ore quantity. The gold recovery rate is 9295 %. The gold quality is acknowledged by a Good Delivery status be-stowed by the Arbitration Laboratory of LBMA and a certificate of Tokyo Exchange of Industrial Goods. «The Muruntau gold is thought to be the world best in quality», Nikolai Kuchersky affirms. «As a matter of fact, we offer «five nines», instead of «four nines» (999.9) approved by the certificates. We are told: «Why do you lose 70 grams of gold per each ton?». The existing status of supply per-mits 100 g of impurities per ton while we have a constant figure of 2630 g. But what is the sense of lowering the level of technology that is so carefully adjusted? But on the other hand we are en-sured that we shall never suffer a failure due to quality. For all these years we have had not a single claim on quality of our supplies». Opposite to other CIS countries, where mining & metallurgical complexes are under the control of private capital, the role of the state is still great in Uzbekistan. NMMC mines gold under the state order and, having no right of free entrance to the market, supplies all ingots produced to its only buyer at so-named «state prices». The Government of Uzbekistan uses the national currency with limited conversion («sum») in its settlements with NMMC but a certain part of these funds are per-mitted to be exchanged for foreign currency. To be sure, the disadvantages of such dependence of the producer on the state are too obvious to comment on them. But the benefits obtained by NMMC due to cooperation with the Government of Uzbekistan and direct support by President Islam Karimov must be mentioned as well. It is the state that assisted in the attraction of the required funds and resources for the modernization of the Zaraf-shan gold-producing complex and the set-up of a new gold-mining center in the town of Uchkuduk where another extractive metallurgical plant processing the ores of the Kokpatas deposit was built in 1995. Nikolai Kuchersky advised the decision of the President of Uzbekistan to prepare a program for the development of the production operations till 2010 with a 1520 % increase of the gold output as against the level achieved now. In this case there should be laid water pipings, a railroad will have to be constructed together with power units, maybe, using nontraditional sources wind and solar energy. «We are not able to solve the problems of this rank by our own funds. That is why we need the support of the state», the general director of NMMC concluded. As to the Muruntau deposit, its mining by an open-pit technique will be carried out for 30 years ahead at an average rate of sink of 15 meters per year. Inclined shafts and drifts may be cut from the mined-out space in due course. This combined technique can be applied to mine the outstanding sections of the deposit to a depth of 8001200 m. Later on, it is predicted to turn to an under-ground technique of ore mining. In consideration of underground operations, the mine will operate half a century at least. As the Muruntau is gradually depleted the role of the new gold-producing complex set up on the united raw materials base of the Kokpatas and Daugyztau deposits will increase. It will include a number of small pits as well. Opposite to the gold quartzite ores of Muruntau, the primary gold sul-fide ores of these deposits are rebellious, with a high concentration of arsenic. For gold to be ex-tracted, fairly complex processing techniques must be applied. Nowadays only oxidized Kokpatas ores are mined. Alongside it, a new process chart using bacterial oxidation of sulfides is being adjusted. NMMC is engaged in this problem jointly with Biomin and Bateman (South Africa) which signed a credit contract and granted a license. The BIOX process as applied to the local ores showed good results but from the viewpoint of economy it was found out that this process will gain no profit because of too low content of gold in the ore. The prime cost of this gold will be higher that the market price. настоящее время отрабатываются только окисленные руды Кокпатаса. A unique complex of X-ray radiometric ore screening became a key link that predetermined not only technological expedience but also cost-efficiency of the project. In fact, an additional dressing cycle whose purpose is «to prepare ore from rock» appeared between the mining operations and the plant of extractive metallurgy. This technology is applied for the first time in industrial practice. Here is it assessed by Nikolai Kuchersky: «We invested about $4 million, carried out hundreds of tests and analyses of process samples, estab-lished a plant with a capacity of 1,200,000 tpy of run-of-mine ore, and we are convinced that our new technology will bring an enormous effect. From a broader point of view, it is the future for not only mining of gold but iron & steel and nonferrous metals industries as well. Following the pilot plant, two high-capacity ore screening complexes will be built directly on the sites of the deposits. The capacity of the Kokpatas complex will be 7,000,000 million tpy of run-of-mine ore. About 2.9 million tpy of dressed ore from the above quantity will be produced as a result of screening. As to Daygyztau, 5.5 million tpy of ore will be mined and 2.1 million tpy of dressed ore will be produced.
Now Muruntau is a gigantic cup of 3.2 km long and 2.5 km wide. The mine is as deep as 480 m. The prospecting drillhole was as deep as 1,875 m with the bottom ore still having gold in its com-position.
Thus, the technology of ore screening applied on the site of mining permits a large quantity of ore rock subject to rejection to be withdrawn from the haulage and processing operations. The content of gold in the sulfide ore under processing raises to 45 gr per ton. Owing to this, the profitable processing of gold sulfide ores of the Daugyztau and Kokpatas deposits can be ensured. The companys specialists study the opportunity of further application of the ore screening technol-ogy. Laboratory studies showed that the gold content in the Muruntau dressed ores can be 100 % improved. As was clarified by Sergey Inozemtsev, chief geologist of the complex, «this problem is not yet urgent for the Muruntau mine. However, by ore screening we can make use of the big tech-nogenic deposit almost one billion tons of mineralized matier, i.e., the ore with low gold content that has been accumulated in dumps for more than 35 years of the operation of the deposit. It is ap-proximately 500600 tons of gold». Already this autumn the results of tests of prototype screen-ing plants are expected to be obtained in Muruntau. It is not improbable that in the foreseeable fu-ture the construction of a new high-capacity complex will begin.
|