Yevgeny Kablov General Director, Russian Institute of Aircraft Materials (VIAM), Corresponding Member of the Russian Academy of Sciences, Professor
With all variety of individual research directions, modern aircraft materials science is summoned to settle two priority practical tasks to establish a complex of materials for craft airframes and for gas-turbine engines (GTE). Lightweight construction, smaller outline dimensions, fitness for work in the conditions of force, temperature, corroding and other actions are to be attained during the en-gineering of these units. The study by VIAM, jointly with TsAGI and TsIAM, permitted promising trends to be identified in the development of aircraft manufacturing. In 10 to 15 years ahead it is pending to increase weight efficiency of materials usage in the plant and helicopter airframe by 25 %, to extend an operating life of the units by 1.5 to 2 times with higher reliability of structures, to raise fuel efficiency up to 13 to 15 kg per passenger calculated per one kilometer of flight with an increase of the ratio of en-gine thrust to weight to 20 kg minimum. Moreover, passengers capacity growth and noise reduction will continue. The settlement of these complex tasks can be helped a lot by the fundamental theo-retical & practical backlog available with VIAM.
Yevgeny Kablov, General Director, Russian Institute of Aircraft Materials (VIAM)
Professor Yevgeny Kablov, Correspondent Member of Russian Academy of Sciences, is 50 years old. Specialist in materials science of aircraft industry. Head of research in higher reliability and longer life of cast blades of aircraft gas-turbine engines from super heat-resistant nickel alloys. To settle the above tasks, a complex method: development of new materials, formation of optimal macro- and microstructures, elaboration of innovative technologies is applied. The outcome of the studies is a two to five-fold extension of working blades life.
Under his guidance promising materials and technologies, which became a new word in aerospace engineering, were developed.
Yevgeny Kablov is a member of Council for Science and High Technologies at the President of the Russian Federation, an author of over 100 scientific publications, including two monographs. He has 54 patents & inventor's certificates.
| |
| |
|
In our opinion, in future there will be retained the scientific and practical relevance of work in the field of light alloys (aluminum and titanium), first and foremost, using nontraditional concepts of structural and intermetallide strengthening. Here aluminum alloys of higher strength will continue to occupy a dominating position (about 50 %) in the airframe materials structure. The application scope of polymer and metal-polymer composites in the airframe structure will grow substantially (up to 25 %). Beryllium-based materials will be used more widely. To be sure, an up-to-date com-bat vehicle cannot be visualized without such a general-purpose material as heat-resistant steel. As a rule, a complex effect of theoretical and laboratory studies is reached only if relevant eco-nomical technologies are developed. In view of this, the development by VIAMs specialists of a full-scale process and equipment for high-gradient casting of monocrystalline blades with penetrat-ing (transpiration) cooling and protection against high-temperature gas corrosion can be attributed to outstanding achievements of modern engineering.
Aluminum alloys More lightweight designs from aluminum alloys with simultaneous higher operation reliability are attained by two ways: higher strength or lower density (without reduction in strength properties). The requirements of higher operating reliability are met by the 1163 alloy of Al-Cu-Mg system de-veloped in VIAM. It is used for fuselage and wing bottom skin. The alloy features high cleanness in impurities, low amount of excess phase and, due to it, high fracture toughness. The manufacture of different semi-products, among them, long plates (up to 25 m) is implemented. The Zr-containing ultra strong V96C-3 alloy of Al-Zn-Mg-Cu system was developed for wing top. The manufacture of semi-products (plates, panels, sections) is implemented. The 1933 wrought alloy of the system with a unique combination of strength and fracture toughness is superior in these properties than the US 7175 and 7050 alloys. The large-size components (frames, fittings, girders) are applied in An-tonovs and Yakovlevs design bureaus. It is planned to apply up to 6 m-long complex-shaped fit-tings in A320 and A380 airbuses. The components manufacturing process has been put into practice by the Samara Metallurgical Plant in cooperation with VIAM. The other way lower density is accomplished through the development of Li-added Al alloys. A series of alloys with low (1420, 1421, 1441) and high (1460) strength has been introduced. The high-strength weldable 1460 alloy is designed for service in a wide range of temperatures from +175 till –253oC. It ensures lower design weight. This alloy applied in space structures permits strength properties of welded constructions to be retained ( up to 0.94) at -253oC which in turn af-fords a 35 %-lower structure weight with a drastic improvement of life and reliability. The similar effect is achieved due to complex metal composites. The VIAM-developed material of SIAL type consists of thin sheets of Al alloy and interlayers of glass fiber-reinforced adhesive pre-preg. SIAL shows high crack resistance/fracture toughness and lower (by 10 to 15 %) density as compared with conventional D16, V95 Al alloys. These metal composites are promising to be used as fuselage skin material. Beryllium and its alloys Efficiency of application of these materials in rocket space and aircraft technology depends on a combination of high heat resistance, heat conductivity, low density, extremely high rigidity, dimen-sional stability, high resistance at low-frequency loading. Thus, brake beryllium discs (as primary structure) with carbon pads for large Buran freight aircraft made it possible to achieve a 2.5 times reduction of brakes weight as against the steel ones and to ensure smoother operation of the brakes, owing to better cooling, along with longer service life of hydraulics. This was achieved after a unique protection system was elaborated The system permitted an elimination of contaminating emissions of beryllium spray at 760oC and a reliable protection against high-temperature gas and contact corrosion.
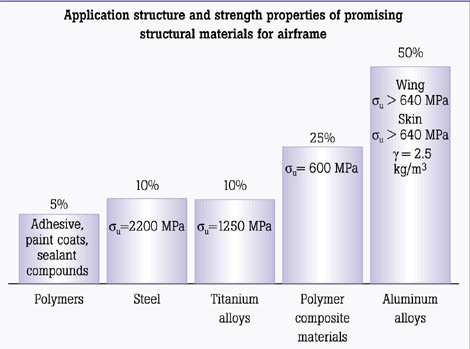
An extended application of beryllium in complex-loaded constructions is hindered by its high sensi-tivity to stress raisers. In this case it is beneficial to use high-modulus weldable light wrought Al-Be alloys. In building and regularities of properties variations Al-Be alloys are to some extent similar to com-posite materials with plastic matrix reinforced by strong solid particles or discontinuous fibers. These alloys have indisputable advantages over industrial aluminum alloys, as surpassing them spe-cific rigidity and strength, and show big promise as structural materials.
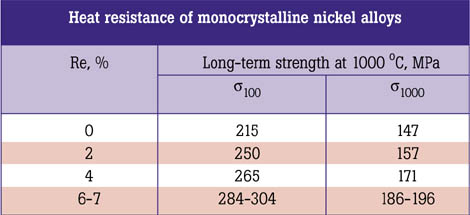
Sheets, presswork, stampings, welding wire and other semi-products can be used for fabrication of structures from high-modulus alloys. The greatest effect is usually achieved when sheet materials are applied which permits very lightweight and rigid constructions to be produced. Titanium alloys The most promising Ti alloys include high-strength VT-22, VÒ-23 and heat-resistant VÒ18H, VÒ25U, VÒ-36 alloys. The prerequisites of wider application of Ti alloys (up to 20, 50 and 60 % in civil and military plane airframes and space systems, respectively) are high level of specific strength, reliability, corrosion resistance, together with good weldability, nonmagnetic properties, high workability and wide range of semi-products. Thus, through complex alloying of and -solid solutions and multi-phase structure, the VT-23 structural alloy is effectively strengthened to a different level of strength ranging from 1100 to 1300 MPa. Therewith, the alloy is less expensive (as compared with Trans206, Trans134 alloys) due to lower concentration of costly molybdenum and vanadium, and absence of tin and zirconium which are in shortage. It is applied for structural elements acted upon by forces and welded joints of aerospace equipment. Presently all kinds of semi-products: foil (0.08-0.1 mm), band (0.15-1mm), sheets (0.8-10.5 mm), plates (11-160 mm), pressed sections and tubes, hot and cold-rolled tubes, rods, forgings, stampings up to 3.5 t in weight are lot produced. A combination of wide range of semi-products and high workability permits all force structures of aerospace equipment to be made from VT-23L alloy. The result of application is a 20 to 30 % weight reduction, lower cost and labor intensity, higher reliability. Among heat-resistant sheet Ti alloys one must note the VT-18U alloy with ultimate alloying of -solid solution, controlled strengthening by aluminum intermetallide and silicides. Heat-resistant 0.8-1.2 mm-thick sheets are made from this alloy. They have higher (by 10 %) long-term strength for 100 hrs at 500oC (600 MPa), at 600oC (200 MPa) and higher (20 %) creep strength than sheets from a similar T-6242 alloy (USA). Heat-resistant alloys based on -solid solutions of intermetallide strengthening type are an example of a new development trend. Higher heat resistance at 600-00oC and satisfactory plasticity are achieved due to age hardening and formation of natural composite type structures. Usage of alloys of this type will afford 25 to 30 % higher strength and heat resistance.
Russian Institute of Aircraft Materials (VIAM) was founded in 1932 as state materials science cen-ter of aircraft industry. The main lines of activities are as follows:
aluminum, magnesium, titanium alloys,
protection of metallic and nonmetallic materials against corrosion,
cast heat-resistant alloys and coatings,
high-temperature materials for gas-turbine engine components,
high-strength steels and instrument materials,
technologies of production and treatment of metallic materials.
Ninety six percent of materials applied in aircraft manufacture in Russia and other CIS countries have been developed in VIAM.
| |
| |
|
High-strength steels The major purpose of steels is their usage in structures requiring high values of rigidity, specific strength, fatigue endurance, heat and corrosion resistance, and some other parameters. Besides, steels can be used in the manufacture of semi-products and complex (among them, welded) con-structions. Steel remains a dominating material in some planes, for example, supersonic fighters. Up to recently the 30HGSN2À steel with 1600-1850 MPa strength level was a high-strength steel most used in aircraft production. Owing to new achievements, the strength level was increased to 1950 MPa with plastic properties retained. Lately new super low-alloyed weldable VKS-8(â= 1800-2000 MPà) and VKS-9 (â = 1950-2150 MPà) high-strength structural steels which are not inferior and sometimes are even superior in crack resistance than the 30HGSN2À steel. One must especially note such application field of high-strength corrosion-resistant steels as cryogenic engi-neering. The advent of promising cryoplanes (hydrogen fuel engine planes) calls for studies to be conducted on carbon-free corrosion-resistant steels for service in liquid and gaseous hydrogen environment. At present VIAM developed and introduced a group of steels for space units. The steels have high strength and are not subjected to embrittlement under the action of low temperatures and hydrogen environment. Heat-resistant materials and advanced technologies of casting for parts of a new generation of gas-turbine as well as ramjet rocket and heat engines are attributed to priority directions of aircraft ma-terials science. An engine of sixth generation must have a target ratio of thrust to weight of 20:1 (in 1970-1975 and 2002 it was 8:1 and 10:1, respectively). Therewith gas temperature is necessary to be elevated by 300-400oC, and a life extended 2 or 3 times. These tasks are being settled based on innovative concepts of alloying high-temperature materials, like intermetallide alloys of Ni3Al type. Metal composites will receive further development. Newest developments The largest breakthrough in the field of higher heat resistance of turbine blades (critical GTE com-ponents), whose temperature and force loads are very high, took place due to a VIAM-developed technology of producing monocrystalline blades at a crystallization front temperature gradient which is 4 to 5 times larger than that of the accepted technologies. This technology developed for the first time in the world ensures a production of monocrystalline blades whose volume fraction of microporosity is 0.09 % (instead of 0.25 % for the technology applied in the USA). It allowed an extension of service life till 34,000-36,000 hrs instead of 17,00019,000 hrs). For the first time in the world practice an original full-scale plant was set up for casting of large-size monocrystalline blades for power units together with technologies of producing monocrystal (up to 450 mm) blades for a new generation of stationary gas-turbine power units of 350 MW in rating. As to latest VIAM studies of applied research, one can point out rhenium-containing nickel alloys having a much higher level of workability and long-term strength properties. The pilot alloy containing more than 70 % Re showed a record value of long-term strength which permits a production of monocrystalline blades with penetrating cooling for engines of sixth genera-tion. Intermetallide alloys ensure further rise of operating temperatures and service life of GTE parts. Heat resistance of Ni3Al-base alloys is regulated by alloyage and cast structure defined by the cast-ing process. The intermetallide alloys contain a much lower amount of expensive refractory ele-ments in shortage, like vanadium, molybdenum, niobium, tantalum, etc. Their application is effec-tive for manufacture of cooled and non-cooled nozzle blades, parts of heat tubes and jet nozzles op-erating in a temperature range from 900-1150oC. Protective oxidation-preventive coatings extend service life of heat-resistant alloy parts. It primarily concerns turbine blades. A new step in the progress of protective coatings became the development and industrial introduc-tion of a multi-component material coating technique a vacuum plasma process of high energy. In this technique an action of accelerated plasma streams on the heat-resistant alloy surface brings about task-oriented regulation of composition, structure, microgeometry, physical and chemical properties of surface under treatment. The types of coatings produced are diffusion, condensed, condensation-diffusion. Further on, reliability and safety of aircraft equipment will be provided by ongoing practical intro-duction of new facilities for nondestructive testing of quality of materials and constructions made from them. Quality control system for aircraft materials, which will include certification of materi-als using more than one hundred of different tests, will gain further acceptance.
|