|
Magazine |
|
About |
|
SUMMIT |
|
Contacts |
|
Home |
|
|
|
|
| |
|
|
 |
#3' 2003 |
print version |
|
URANIUM MINING: UNCONVENTIONAL TECHNOLOGIES |
|
Evgeny Tolstov Chief Engineer, Navoi Mining & Metallurgical Complex (NMMC)
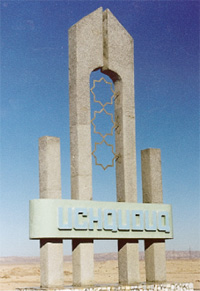 Uchkuduk means "three wells" in Uzbek. In fact, there are no sources of water in Uchkuduk. Instead, enormous uranium reserves are concentrated there, which could last for no less than 100 years. |
|
he Navoi Mining & Metalurgical Complex (NMMC) was specially set up for mining uranium. But, as time went by, its priorities changed. Nowadays our attention is focused on the gold-mining complex. Mining and selling gold account for 80 % of NMMC budget, while the share of the uranium-mining amounts to no more than 15 %. This is explained by economic and political reasons. But there are also reasons of a technological nature.
In todays conditions the development of gold production requires considerable efforts due to the need for technical modernization, introduction of new methods of mining and processing. As for technologies of getting uranium products we, one might say, have already achieved the level of perfection. All the production cycle is ideally adjusted. It does not require a day-to-day intervention or capital investments and leaders of the integrated mill do not have any special problem with it. As far as the uranium production is concerned, we are far above the world level. In our practical work we are using such methods that are known to the West only in theory or, as in one of the laboratories in the state of Nebraska, are at the stage of experimental research studies at the best.
During more than 40 years of the integrated mills existence the uranium production passed through several technological stages. And each of them produced innovation solutions directed towards the future. In 1959, when the enterprise was just being formed, uranium was extracted through underground mining with the use of the technology copied from the one that was applied in the coal industry: the same pit-faces, the same chisel hammers and coal-plough machines. There was a need to adjust this equipment or even alter it on the spot since no specialized machine-building for the new industry was developed by then. Mining of uranium was done in the most difficult conditions: watering, heat, poor ground stability, ionizing radiation background. But the most dangerous were emanation and evolved radon that was very hard to fight with in a closed space. Problems of the production economy and prime cost of products did not matter much then and were not considered important.
The next stage was the transfer to the open cast production. The integrated mill was building open casts and gradually closing mines. This way of extracting uranium is more productive and less dangerous. But, essentially, the technological scheme remained the same. The ore was extracted, loaded in cars and brought for processing into a final product.
|
Evgeny Tolstov
Chief engineer of Navoi Mining & Metallurgical Complex (NMMC). Born in the city of Irkutsk (Siberia) in 1944. Graduated from the Moscow Geological Prospecting Institute. While studying at the institute, showed a particular interest in nontraditional technologies of conducting mining operations, including underground leaching (UL), which later became the main subject of his scientific research. Doctor of engineering, professor of geotechnology. Author of scientific works on the UL problem.
From 1982 to 1993 worked as an engineer becoming the director of NMMC enterprises in the cities of Uchkuduk and Zarafshan. During that period uranium deposits were developed in mines and open casts. By his own initiative began introducing the UL technology. Especially proud of the fact that on his insistence the mine of the Vostochnoe ore department (the city of Zarafshan) was closed down regardless of enormous uranium reserves available there (40,000 tons). As he himself explains the reason for such a decision, "the mine should be closed down due to moral, economic, technical reasons, let alone just common sense". Works were carried out in conditions unacceptable to any human being: at the depth of 500 meters, with the temperature reaching 60 oC and emanation being on a very high level.
Very sociable and enjoys sport: hunting, fishing, billiards and football. He has two children. His son followed the fathers footsteps and graduated from the Moscow Geological Prospecting Institute. Later, the son graduated from the U.S. mining school (near Denver, Colorado) and now works as the chief production engineer at the Uzbek-American JV Zarafshan-Newmont. The daughter is a market expert, works in Moscow.
|
|
| |
|
The real change of all technological modes in the mining business began, when NMMC started introducing the method of the uranium underground leaching (UL). We became the first in the world, who upgraded this method and used it on an industrial scale. The new scheme was working the following way. Acid solutions were injected in drilled wells, there was a reaction in an ore layer and after that a liquid product was lifted from there. Then, it was enriched and brought to certain standards at the integrated mill.
The UL technology finally replaced traditional ways of producing uranium. Underground mining and, later, open cast works were discarded. It happened so that this period coincided with the well-known events in the countrys life. All political and economic guidelines were changed. Thus, it was necessary to think of not only increasing production volumes but also of the amount of costs, of the U.S. anti-dumping campaign, of the state in the world market, where the price for uranium fell down to the all-time low level amounting to $6.5 a pound.
We were producing then about 3,000 tons of protoxide-oxide of uranium a year. The essential question arose: should the integrated mill keep producing uranium at all? Our raw material base was sufficiently reliable. The discovered and proven reserves were enough for 50 years of mining. By estimates, the hypothetical reserves were even more considerable. After weighing our potential we decided to preserve this business direction and find such ways of its development, which would allow us to maintain a stable uranium production till the market started to rally.
The years have passed but the price is still low. The integrated mill has been forced to reduce production volumes by 20 % to 30 %. Nevertheless, despite the unfavorable world market conditions the uranium production continues to bring us high profit.
In these years NMMC has made one more technological jump: it started producing uranium the reagentless way. The idea is that we do not inject sulfuric acid into a layer as before but use water and air instead for initiating the same solvent, which is contained in the subsoil itself.
This new technology has given the integrated mill a number of advantages. Expenses on producing 1 kilo of uranium went down by at least 50 %. There was no longer a need to use stainless steel since the equipment, pipelines and capacities stopped being damaged by the aggressive environment. There was no need to spend funds to buy acid that accounted for up to 30 % of the products prime cost. Operations became safer and this permitted us to cut down expenses on labor protection. But the most important thing was that costs of land reclamation went down sharply.
Probably it will be of interest to trace the way the impact of our production operations on the environment changed along with changing methods of uranium extraction. The matter is that after underground mining shafts, mining workings remained. Water-sealed mines and dumps were left behind after open cast works. A billion cubic meters of soil is still piling up near the city of Uchkuduk, which is the center of mining uranium. The UL technology does not seem to leave traces on the surface but the ecological characteristics of underground waters sharply worsen. When we tried to change things by using a strong reagent (foreign companies are still doing precisely this), then, besides uranium, the solution also absorbed other elements: iron, aluminum, heavy metals, etc. Before starting work in stratal waters there were three grams of salts per liter by solid residual but when we were leaving the site, there were 43 grams already, i.e. the content was much higher. The present reagentless scheme of leaching leaves the salt content practically unchanged. This is a selective method. Like a scalpel, it cuts off uranium only.
It seemed that after we learned to develop the reagent directly in ore layer, thus, turning the subsoil into one of the shops of our enterprise, we reached the limit and we could not make progress any more. But we keep moving forward. Right now we are developing the method of bacteriological leaching of uranium on the pilot scale. This technology is to supplement the reagentless method but, essentially, it is becoming a new technological stage. All necessary installations have been manufactured and we have prepared cultures of bacteria. We have already had some promising results and we hope that the new method will permit us to raise the metal content of the solution by 40 % while our present expenses will remain the same.
Probably, there is a direct dependence of efficiency of mining operations on methods of influencing the environment. The ruder your attitude to developing deposits is, the costlier and so much the worse ecologically the results are. And vice versa: the more delicate you are, the more economical, beneficial and simpler the outcome will be. I think that, if the choice of technologies was made precisely this way meaning not production volumes but attitude to the environment, then, production results would be much better as well.
Our technologies were highly appreciated by authoritative international organizations engaged in controlling the atomic industry field. The IAEA commission and representatives of the Swedish Institute of radiation protection came to meet with us. They visited all facilities of the production cycle. There were no critical remarks in reports on results of inspections. And in conversations inspectors, who were highly skilled specialists with a rich experience, expressed many times their delight in how ecologically faultless the uranium production was.
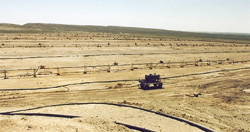 The range near the city of Uchkuduk. Advanced technology gives the uranium mining process the appearance of oil production. But only on the surface. |
|
Schematically, the uranium production is organized the following way. Each uranium-mining department (NMMC has three of them) has three mining sites, which are often scattered in the desert 100 km from one another. There is a small town built in the center for 10,000 people. Mine workers extract uranium and they bring its concentration through the chemical process up to approximately 0.5 gram per liter of the solution. The solution is brought in cisterns to the integrated mill in the city of Navoi and a 100% uranium protoxide-oxide is produced there with a simple technique that does not require any special efforts (calcinations, dehydration, etc.). This product is packaged in accordance with the established international standards and is shipped under long-term contracts to foreign companies, to spot markets, etc.
In this connection it seems appropriate to mention some problems related to international cooperation. We signed a contract with China to sell the technology of reagent leaching. NMMC is to provide the technological procedure regulations. Our specialists check and adjust the technology on a test site taking into account specifics of the given field. And, after that, the Chinese will be mining uranium on their own and for the next 10 years they will be paying to our integrated mill a certain interest on every kilo of produced uranium. The total amount, which NMMC will get from selling its intellectual property, is estimated at tens of millions of dollars. We are receiving proposals to set up joint ventures to produce uranium from the U.S., UAE and some other countries. The appropriate projects are now being worked out.
The atomic power industry is gradually coming out of stagnation. New large projects of modernizing and constructing new nuclear power plants are emerging. Stocks of nuclear fuel accumulated earlier are being exhausted. I do not think that we will have to wait long. Any day now the slump in sales that has been going on for many years will give place to a rush demand and prices will be steeply rising. And the real business will start then for those, who have advanced technologies and fields prepared for development. 
|
|
|
|
|
current issue

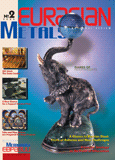
previous issue

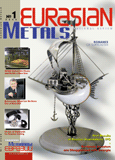
russian issue

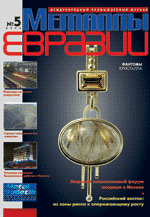
|
|