|
Magazine |
|
About |
|
SUMMIT |
|
Contacts |
|
Home |
|
|
|
|
| |
|
|
 |
#4' 2003 |
print version |
|
MARKET OF RAILROAD WHEELS: HANDICAPPED ONLY BY SHORTAGE OF THEM |
|
Andrei Karunos
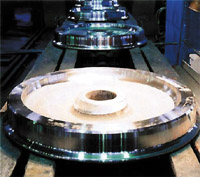 Nizhny Tagil Iron & Steel Works |
|
he dynamic development of the Russian market results in situations when demand starts exceeding supply. Railroad wheels, wheel axles and railroad wheel sets have become precisely the goods, which are in especially great demand now. Due to their shortage the rolling stock repair program scheduled for 2002 was actually implemented by 80 % only.
In Russia railroad wheels are mainly produced by two companies, which are the Vyksa Steel Works owned by the United Metallurgical Company (UMC) and the Nizhny Tagil Iron & Steel Works (NTMK) controlled by EvrazHolding. According to the analysis by the All-Russian Railroad Transport Scientific Research Institute, currently these producers are not in a position either to meet the market demand or offer products, which would be in a 100 % compliance with necessary standards. There are grudges against both the quality of metal and wheel` s geometry. Mechanical properties of railroad wheels and rails are getting more unbalanced. Hardness and wear resistance of rails have increased 1.5 times on average resulting in a shorter service life of railroad wheels.
Railroad wheel producers agree: the problems really exist, though, in their opinion, it is railroad men who are to blame for the current situation. The railroad transport in Russia is a state monopoly run by the Russian Ministry of Railways (RFMR). In the past ten years at least the Ministry placed no major orders with the producers so they had to develop manufacturing other products, which were in demand on the market. Alexei Kushnaryov, the chief engineer at NTMK, reminds that from 1997 to 1998 RFMR stopped buying railroad wheels and now it is in a hurry to make up for the neglect.
Steel makers invite their partners to solve the problem jointly. Now NTMK is starting modernization of its railroad wheel production facilities. In this connection the company held a special conference with railroad experts. According to Mr. Kushnaryov, RFMR representatives accept the quality of steel made by NTMK, yet everybody agrees that its rolling technologies are obviously outdated.
The railroad wheel rolling plant at the Nizhny Tagil Iron & Steel Works has been in operation since 1955. In 1975 the plant with the annual design capacity of 440,000 wheels reached the maximum production of 602,000 railroad wheels a year. There are four production shops in the plant, which are in operation now: the blanking shop, machining shop, heat treatment shop and heating furnace shop. Before 1993 wheels used to be machined from round-bottom cast ingots of open-hearth steel. When the open-hearth furnace was shut down, they switched to converter steel, which gets heat finishing through the furnace-ladle process and vacuum degassing. The continuous casting machine makes round blanks with 430 mm in diameter.
Though provided with a high-quality steel, NTMK still can’ t produce high-quality wheels from it. "We are sorry to see that we fail to meet RFMR’s requirements for the wheel geometry,"– admits Alexei Kushnaryov. Besides, the chief engineer considers the press-rolling technology used at the plant ineffective: "We are making wheel blanks at the rolling mill to machine them afterwards and we are losing a great deal of metal. We actually waste the material".
The planned modernization of the press-rolling shop will ensure higher accuracy of wheels` geometry and enhance capacity of the equipment. It is also planned to proceed with expanding the range of wheel steel grades and start producing wheels of low-alloyed steel.
In the previous decades there were just insignificant changes in design, dimensions and configuration of railroad wheels. However, operating conditions of the freight car fleet became much tougher. The program to construct freight cars of a new generation provides for higher loads on the axle and that calls for a new design of the wheel.
In 2001 NTMK produced two batches of the new generation wheels with the S-shaped disk, which meet all the requirements by both their sizes and mechanical properties and which have a higher hardness of the rim and enhanced durability. According to railroad specialists, "NTMK’s pilot design wheels with the S-shaped disk have successfully passed development testing and can be recommended for field tests with higher loads on wheel axles".
In the future the annual demand for wheels of the new design will increase to 150,000 wheels in 2005 and to 550,000 wheels in 2010.
Reconstruction of NTMK’s wheel rolling plant provides for raising its production capacity up to 630,000 wheels a year. The modernized plant will produce wheels of standard diameters ranging from 710 mm to 1270 mm with disks of different designs, including the S-shaped, membrane type and cone-and-plate ones.
In the course of the reconstruction it is also planned to install equipment for secure removal of scale. To constantly ensure precise sizes of blanks working tables of presses will be technologically fixed. Accessory equipment of the presses and the rolling mill will permit to make blanks with a machining allowance for no more than 2 mm. The press-rolling production line should have the capacity to handle large blanks with the maximum diameter of 430 mm, being 315 m to 1,100 m long and weighing from 360 to 1,250 kg. All surfaces of wheels will be completely machined: it is planned to set up a machining line fully equipped to provide quick and high-quality turning of all segments of the wheel.
An automatic control system of the plant will check up machining of each wheel at every stage of the process. Control devices will ensure full compliance with technological parameters, monitor machining of every single segment of the wheel and, if required, adjust parameters of the machining.
The equipment for the wheel rolling plant will be supplied on the tender basis by SMS-Eumuco, Germany’s company, and NKMZ , the Ukrainian enterprise.
"After the reconstruction is over, RFMR would like to get all the wheels to be produced by NTMK. However, in addition to the Russian market there is a world market as well,– reminds Mr. Kushnaryov, – During my recent visit to Germany connected with the fulfillment of our order I also met with representatives of German railroads. They expressed a deep interest in NTMK and said that they would like to buy our wheels. We have been supplying wheels to Bulgaria and Canada. We are ready to work with other consumers as well."
NTMK plans to put the new press-rolling line into operation on October 31, 2004.
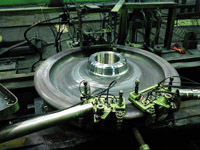 Vyksa Steel Works |
|
As compared with NTMK, the Vyksa Steel Works is a larger producer. It has a unique industrial complex that is Europe’s leader in making solid railroad wheels of 700 to 1200 mm in diameter. Rates of wheel production there are growing up: if in 1997 the Vyksa Steel Works manufactured 246,000 wheels, in 2002 it produced 548,000 wheels.
The Vyksa Steel Works has introduced new solutions in its wheel production technologies and equipment. Now it is implementing a long-term quality improvement program. Last year the company reached an agreement with RFMR, which, according to Anatoly Sedykh, the president of the United Metallurgical Company, gave the Vyksa Steel Works and UMC an opportunity of a long-term planning and allowed to work out an investment program. In 2004 they plan to raise wheel production up to 650,000 wheels a year and to reach the level of making 700,000 wheels in 2005. These will be modern, high-quality wheels designed to sustain a higher speed of trains and heavier freight traffic.
As Anatoly Sedykh stresses, his enterprise has refocused its production activity on the domestic market to meet RFMR` s needs in full, including its quality requirements. Out of 40,000 wheels currently produced by the Vyksa Steel Works 24,000 wheels are made with a hard rim. Next year the company plans to apply shot-peening to all wheels to ensure a higher hardness of their disks. This treatment is expected to improve wheel` s run by 15 %. The Vyksa Steel Works, like NTMK, also intends to start production of wheels with the S-shaped disk.
To all appearances, the wheel producers are moving the similar ways. The Vyksa Steel Works also has an agreement with NKMZ for supplying equipment to make wheel steel. This agreement provides for a furnace-ladle installation and a vacuum degasser. The first melt of wheel steel is set for May 2004.
The modernization of the wheel rolling plant should enable the Vyksa Steel Works to accomplish the task put forward by RFMR i.e. to increase service life of wheels from 7 to between 10 and 12 years. Russia’s railroads account for 80 % of all freight traffic. Last year for the first time in the past decade freight traffic increased 9 %. In 2003 alone more than 270 million tons of cargoes were transported by railroads. According to Gennady Fadeev, the head of RFMR, his Ministry intends to increase the railroad freight traffic: "Fulfillment of these obligations depends to a great extent on the technical condition of rolling stocks". So, during the next decade the market of railroad wheels will be getting more and more attractive to metallurgists.
|
|
|
|
|
current issue

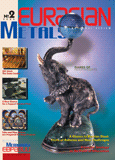
previous issue

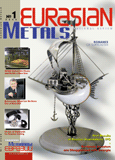
russian issue

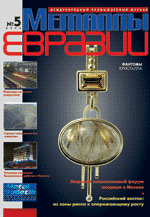
|
|