|
Magazine |
|
About |
|
SUMMIT |
|
Contacts |
|
Home |
|
|
|
|
| |
|
|
 |
#3' 2004 |
print version |
CHEAP RESOURCES MAKE UP FOR TECHNOLOGICAL LAG |
On the question of Russian metallurgys competitiveness |
Yuri Adno
he Russian metallurgical complex, along with the fuel-and-energy and some defense segments, is the most competitive sector of the countrys industry. At present, Russia exports about half of its rolled iron stock, over 80% of primary aluminum, 70% of nickel and titanium, about 40% of copper, zinc, etc. Russian producers account for about 12% of the world steel market, between 15% and 20% of the world aluminum market while their shares of the world titanium, nickel and cobalt markets amount to 40%, about 30% and 20% respectively.
The dynamic growth of metal exports, the total volume of which makes Russia one of the world leaders, proves competitive advantages of its national metallurgy. To a large extent, this breakthrough to world market has become possible thanks to a major and sufficiently diverse raw material base, high concentration of production capacities, availability of skilled labor force and advanced scientific potential. Metallurgical mills, which export most of their products, as well as ore-mining enterprises that provide them with raw materials have withstood ‘the shock therapy of market reforms with less trouble than other industries and succeeded in attracting investment resources while preserving their production potential.
The competitiveness of the metallurgical complexs products is influenced by the interconnected internal and external factors. The first group includes those, which are directly linked to state of enterprises production facilities and its operations: indexes of prime cost and production cost parameters, quality characteristics of products (chemical as well as physical and mechanical properties, dimensional accuracy, compliance with the international standards), marketing policy and sales, extent of state support (regulating tariffs on energy and cargo transportation, tax and customs policy). Russias specific feature is the factor of the so-called ‘social burden. That is, in other words, the amount of social obligations that companies have to take with respect to not only their personnel but also to towns where their enterprises are located.
The second group of factors covers, above all, external characteristics that influence processes of production and marketing of products: ratio between currency rates, level and dynamics of world prices, the States measures of external economic support.
At the beginning, the idea to quickly integrate Russias economy in world market was actively supported by the State. This support was demonstrated by liberalizing the countrys foreign trade: revoking export quotas and duties, simplifying the licensing procedure. For metal producers a chance to make real money in foreign markets was much more attractive than their ties with Russian consumers. During that time the domestic market was characterized by both low demand and weakness of the financial system that serviced it.
The export orientation helped Russias metallurgy get through the most difficult period of market reforms. However, it was not a panacea but rather it was a kind of dope that conserved the industrys deep-rooted problems. The negative aspects of the business, which is concentrated mainly on export shipments, are quite obvious.
Above all, the large share of export products increased Russian companies dependence on fluctuations of market demand and world prices. In some sectors of the non-ferrous metallurgy, mainly in the aluminum production, companies switched to tolling contracts, which are still widely used reducing the market effectiveness of the business. As for the structure of shipments, the Russian exports are clearly dominated by ordinary and relatively cheap types of metal products: cast iron, slabs, blanks, non-ferrous metals ingots and cathodes. Sales of products with higher added value are hampered by tariff as well as non-tariff restrictions: more than 50 antidumping investigations have been started against Russian exporters whose losses are estimated at $2.5 to $2 billion. On the other hand, the large-scale export of semi-finished products have resulted in their deficit in the domestic market and stoppages of production capacities at semi-integrated mills. Products of these enterprises have also been in short supply and they are replaced by the imported ones.
The most specific feature of the market of mass metal products is the price competition, i.e. the competition in prime cost. Since 1992 the prime cost at Russian metallurgical enterprises has been constantly rising due to the steady increase of prices for raw material resources, tariffs for services and in nominal payments for labor and allocations for social needs. Of the major importance is the total amount of expenses on products and services of natural monopolies, which include three national super-corporations RAO UES Russia (electric power), Gazprom (production and transportation of natural gas) and Russian Railroads. In the last ten years the average rates of growth of their tariffs and prices have been surpassing the growth of prices for metal products by 1.5 to 2 times.
The quality of Russian metal products is well described in the assessment by the countrys Ministry of Industry: the share of those products, which comply with the international standards, does not exceed 25%.
It is worth to note that during those 20 years before the demise of the USSR the technological lagging of the Soviet metallurgy behind the level of the leading industrialized countries was obvious. Reforms provided the incentive for restructuring production capacities, mainly, through liquidating morally and physically outdated equipment. In ten years the share of the open-hearth production went down from 55% to 28% while the share of continuous casting increased from 23% to 56%. However, it is still far behind the leading countries level (from 90% to 96%) and the world average (75%). The wear extent of production equipment is considerable yet: about 49% in the steel industry and over 65% in the non-ferrous metallurgy.
The technological lag predetermines the low efficiency of production and higher consumption of basic resources. Thus, the average consumption of steel to produce one ton of rolled products amounts in Russia to about 1,200 kg, while this figure is about 1,130 kg in the U.S. and the leading EU countries and it is less than 1,100 kg in Japan. The consumption of coke to produce one ton of cast iron exceeds the similar index in Western countries by 40% to 50%. The labor productivity at the largest enterprises of the Russian steel industry, such as ÌÌÊ, NLMK and Sevestal, 6 times as low as in Japan, South Korea and Taiwan and it is 3 times lower than in the U.S. (not taking into account differences in the range of products). It is true that, at the same time, the structural peculiarities of Russian enterprises should be taken into account. Among them, for example, are the large number of auxiliary shops and facilities and support of the social sphere that is considerable by its scale. In Russias conditions transportation costs are also rather high. It is estimated that the average distance of transporting by railroad raw materials, fuel and products amounts to between 5,000 and 6,000 km per one ton of metal.
Nevertheless, even with such a level of resource consumption the countrys metallurgy remains quite competitive. Thus, material costs to make metal products in Russia are by 1.8 to 1.9 times lower than in the industrialized countries. The reason is lower prices for all kinds of resources. Prices for iron ore and scrap existing in the domestic market are lower by 25% on average than the world ones, natural gas is sold approximately 5 times as cheap as in Western markets and electric power is cheaper by 2.5 to 4 times. The Russian business spends considerably less (by between 3.3 and 6 times) on paying for labor as well. The cost of one man-hour at Russias metallurgical mills is from 8 to 17 times lower than at foreign enterprises. Precisely these factors result in competitive advantages of Russian metal products.
The potential of the Russian metallurgys competitiveness depends, to a large extent, on external factors, such as the ratio between rates of currency exchange. This was fully proved by events following the crisis of August 1998: the ruble devaluation and abolition of ‘the currency corridor contributed to the dramatically improved economic indexes in the metallurgy between 1999 and 2000.
In the long term, the Russian metallurgy, probably, will keep and even consolidate its position among leading world exporters. In our opinion, a number of favorable conditions will make it possible.
First, as the experience of previous years shows, the production potential of the countrys metallurgical complex, including capacities of ore-mining enterprises, is considerably more than enough to meet the Russian domestic needs. Second, in recent years, the demand and prices for metal products have been perceptibly growing thanks, mainly, to Asian countries and, especially, China. Experts estimate that this trend can remain for the nearest 7 to 10 years. Third, the Russian metallurgy as a whole has overcome the most complicated stage related to the redistribution of property, primary accumulation of investment resources, formation of advanced management and entry to the world capital market. The process of establishing large holding-type companies has been completed: as a result, there is a strong core formed in the industry by such major corporations as Severstal, EvrazHolding, Rusal, Norilsk Nickel, SUAL Group and Mechel, which are actively integrating in world metallurgical business.
Successful activities of metallurgical companies are furthered by the trajectory of the steady growth that the Russian economy has achieved. The political stability that ensued the 2000 presidential elections and measures taken by the State to maintain the macroeconomic stability (the introduction of the Tax and Customs Codes, reduction of bank credit rate, protection of the domestic market from dumping) make businesspeople much more confident in implementing strategic plans.
But, as before, the key condition of raising the Russian metallurgys competitiveness remains the same: continuing modernization of production capacities and overcoming the technological lag behind main competitors. At the same time, the priority is to be given to non-price factors of the competitiveness, i.e. increasing the share of metal products with high added value.
Structure of expenses on making steel products, %
Components of expenses Russia U.S. Japan Germany
Material expenses 73.7 59.8 55.9 59.3
Payments for labor 15.4 32.1 31.0 31.5
Amortization 2.4 6.0 8.7 6.9
Other expenses 8.5 2.1 4.4 2.3
Total 100.0 100.0 100.0 100.0
Source: The Union of Russian exporters of metal products (based on the analysis of data for 2001).
|
|
|
|
current issue

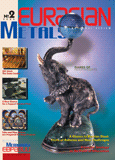
previous issue

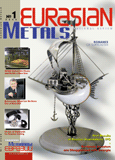
russian issue

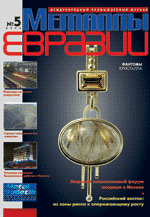
|
|