|
Magazine |
|
About |
|
SUMMIT |
|
Contacts |
|
Home |
|
|
|
|
|
|
|
 |
#3' 2004 |
print version |
|
WESTERN CREDITS AND TECHNOLOGIES: NEW HEIGHTS FOR NTMK |
|
Andrei Karunos
n July a new continuous casting machine has been put in operation at the oxygen-converter shop of the Nizhny Tagil Iron & Steel Works (NTMK). It has been supplied by Voest-Alpine along with other equipment for the steel out-of-furnace processing. The cost of the contract, 86 million euros, is not something unprecedented for the Russian steel industry. The most important is another aspect of the deal: it is the first time that foreign investments have arrived as direct money credits. Thus, NTMK and EvrazHolding, its management company, have received not only the latest technology but they have also set a precedent of qualitatively new relations with the Western business acting as an equal responsible partner.
Mikhail Arshansky, the director of NTMK for long-term development said that Voest-Alpine Industrieanlagenbau (VAI) has constructed the whole complex on the turnkey basis in less than two years and this means that the project has been implemented five months ahead of schedule. This situation reminds of the well-known Soviet ambition: to show the West the ability to work faster than the adopted schedule requires. However, this time around the Russian ‘acceleration is aimed at reaching a particularly pragmatic goal. The favorable market conditions have provided a high profitability of steel companies and allowed them to start a large-scale modernization of production capacities. EvrazHolding, Severstal, MMK and NLMK, leaders of the Russian steel sector, are investing hundreds of millions of dollars to update their potential as they hope to get a solid return in the shortest possible time and ensure a reliable margin for the future, when the market curve may go down again.
In the words of Mikhail Arshansky, the NTMK modernization program is planned for the period till 2009. It provides for a complex development of all technological process stages and the appropriate infrastructure. Reconstruction will be done on the blast-furnace, steel-melting and rolling production facilities. Besides, large investments are being directed in consolidating its own energy base: in the foreseeable future NTMK will be able to independently generate about 60% to 70% of the needed electric power. After the modernization is completed, this integrated mill will become one of the most advanced enterprises of the Russian steel industry and a highly profitable division of EvrazHolding.
Right now the second stage of the mills reconstruction is underway but, at the same time, several already modernized as well as newly constructed facilities are being put in operation. At the end of June the third furnace-ladle installation has been commissioned and from that moment NTMK has been the owner of probably Russias best system of metal preparation. There are three furnace-ladle units in operation now at the oxygen-converter shop as well as a vacuumator and a desulfurization unit. In the opinion of Mikhail Arshansky, so far not a single integrated mill in the CIS with the full iron and steel cycle does possess such a set of advanced units.
The further start-ups look even more impressive. As Arshansky said, in addition to the continuous casting machine supplied by Voest-Alpine, the program provides for commissioning in the second half of 2004 completely reconstructed blast furnace No.6 and a new equipment at the wheel-tiring shop: a pressing-rolling line, a line to machine railroad wheels and a complex of their quality finishing control. By estimates, these technologies will be recouped comparatively fast and already next year they will start bringing profit.
Mikhail Arshansky highly appreciates the importance of the new continuous casting machine for the steel-melting production at NTMK. This powerful single-strand machine capable of making 1.5 million of slabs a year will let the enterprise "totally complete the switchover to continuous casting", he stresses. As a whole, the program to update the steel-melting process stage will be accompanied by liquidating outdated inefficient capacities, such as the five remaining open-hearth furnaces and the blooming. Along with the engineering modernization it also provides for a significant growth of production volumes on the basis of advanced technologies. If todays capacity of the converter shop is limited to producing 3.5 million tons of steel a year, after the reconstruction it will increase up to 5 million tons, says Arshansky. The shop is being equipped with the newest system of purifying converter gases as well as a set of engineering devices that allow to save time for blowing and to raise steel quality.
It is obvious that the implementation of the joint project with VAI is directed to achieve far-reaching goals as well. The operational characteristics of the continuous casting machine and accompanying units allow to make high-quality steel for producing thick-sheet rolled products and subsequently, welded pipes. The idea to build a larde-diameter pipe-making mill in the city of Nizhny Tagil has been postponed but not forgotten. The scheme of getting a full technological line a continuous casting machine, mill-5000, pipe electric welding mill, coating section still decorates the walls of Mikhail Arshanskys office. Nobody at NTMK doubts that constructing new trunk oil and gas pipelines along the northern route to Europe as well as through Siberia to the Pacific coast will prompt the return to plans of creating a pipe-making complex. Within this scheme the VAI-made continuous casting machine is considered to be the first phase of the future pipe-making mill.
So far another scheme is being implemented. In 2003 EvrazHolding signed an alliance agreement with the Severstal Group on jointly using available capacities. It is planned that slab billets will be brought from NTMK to broad-strip mill-5000 in the town of Kolpino (the Saint Petersburg region), the reconstruction of which will soon be completed.
The Nizhny Tagil Iron and Steel Works occupies a special niche in the market as a maker of products for railroad transport. It manufactures rails, wheels, tires, blanks for axles, car-building profiles. This market sector is about to get booming now: the Russian Railroads JSC, which has started modernizing its locomotive and train car fleet, has sharply increased orders and raised requirements with respect to ‘transport metal.
Railroad wheels are made in Russia by the two enterprises, NTMK and the Vyksa Steel Works (integrated in the United Metallurgical Company). "The wheel-rolling shop at our mill is the first one constructed in Russia, it is over 50 years old. So, it has been ripe for reconstruction a long time ago", says Mikhail Arshansky. In June a wheel quality control installation has been put in operation, which includes an ultrasonic and instrument quality control line. This RWI-01 (Railroad Wheel Inspection) system was specially developed and manufactured for the NTMK wheel-rolling production by institutes of Germanys Fraunhofer Gesellschaft, the leading European organization for technical innovations. It allows to check rolled-steel wheels through 13 channels of control in accordance with requirements by the Russian Railroads JSC, international standards as well as national standards and specifications of such countries as the U.S., Germany, France. The ultrasonic control installation is included in the wheel data system. The detailed information on parameters of adjustment and results of control is also kept in the data bank of the RWI-01 system for the whole wheel service life.
Mikhail Arshansky points out that, regardless of the ongoing reconstruction, the wheel-tiring shop keeps making its products. In his opinion, it proves once again the rationality of the NTMK reconstruction plan. Thanks to the powerful complex of steel finishing and cleaning at the oxygen converter shop, the wheel shop could afford the closedown of the blank preprocessing section and start construction of new facilities.
A new pressing-rolling line is planned to be commissioned in October. It has been designed by SMS-Imuco (the division of SMS-Demag) and the project is being implemented jointly with the Novo-Kramatorsk Machine-Building Plant (Ukraine), which specializes in making presses. Simultaneously, works are being done to construct a wheel machining line that allows to fully process wheels. So far NTMK can do it on only some parts of the wheel surface. As Mikhail Arshansky notes, it will be possible to make wheels with the S-shaped disks, which presently are most demanded.
With the start-up of the new line the annual production volume will increase almost one third, from 450,000 up to 600,300 wheels. However, even this volume will fail to meet needs of the railroad industry.
In the next two years the second stage of reconstructing the wheel production facilities will take place. At the same time the reconstruction of the rail-and-beam shop will start.
Touching upon the cast iron production, the director of NTMK for long-term development told about plans to reconstruct three blast furnaces. They will provide as much cast iron as the whole blast-furnace shop is making now with six furnaces (five of them are in operation today). These furnaces will start operating under a single technology, with a same-type equipment and same parameters. The unification will allow to improve the technology of the blast-furnace production and raise limits of equipment repairs. Intellectual management systems will make it possible to provide the most efficient modes of operation and that, in the words of Arshansky, will permit to sharply reduce consumption of coke: the saving is expected to reach up to 20 kg per ton of cast iron.
Mikhail Arshansky gave a detailed description of blast furnace No.6. This furnace, one of the largest in Europe, replaced the furnace that was put out of operation in 1996. It was developed by specialists of the integrated mill, who possess the experience, unique in Russia, of melting vanadium-containing types of cast irons. The optimal profile of the furnace and a number of other engineering features allow to successfully smelt other kinds of heat-resistant raw materials, which, for example, contain titanium. Blast-furnace stoves designed by Russian expert Kalugin can operate without repairs for as long as 25 years. The furnace itself should operate for about 20 years without overhaul. Its equipment was supplied by both Russian and Western companies Gosha, Paul Wurth, Voest-Alpine. The design capacity of the sixth blast furnace amounts to 1,730 million tons of cast iron a year. That is enough to avoid complications of the production cycle and start repairing the fifth blast furnace so as to do the same reconstruction works as well as to close down one more blast furnace.
In 2004 investments in the engineering renovation of the integrated mill will amount to $170 million and, as far as the modernization of NTMK is concerned, they will total $66o million by 2009. Terms of recouping all projects that are included in the NTMK reconstruction program vary from 3 to 6 years from the start of works.
|
|
|
|
|
current issue

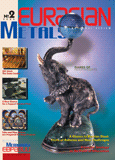
previous issue

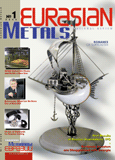
russian issue

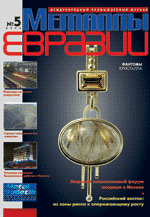
|
|