|
Magazine |
|
About |
|
SUMMIT |
|
Contacts |
|
Home |
|
|
|
|
| |
| |
 |
#3' 2005 |
print version |
|
TINS RENAISSANCE |
|
Yury Adno
lthough tin belongs to the so-called big six of stock-exchange metals (along with aluminum, copper, nickel, zinc and lead), the volumes of its world production are comparatively not large, amounting to between 250 and 300 thousand tons year-on-year. The concentration of tin that, as a rule, can be found in subsoil complex ores reaches no more than 1% to 2%. The dressing of this ore requires considerable expenses that results in high prices for the metal.
The main consumer feature of tin is its low toxicity and this determines the leading sphere of its use. That is making of tin-plate for packing food products. Besides, tin is used to make bronzes, bearing alloys (babbits), type-metal alloys as well as components of various chemical accelerators.
Until recently the tin industry was in a protracted crisis. The sluggish demand and extensive overproduction of the metal led to bankruptcies of many tin mines in Indonesia, Thailand, Malaysia. Only in late 2003, riding the wave of the general boom in the nonferrous metallurgy prices for tin started rising and in a few months increased 2.5 times. By this index tin became the champion among all metals of the stock-exchange group.
Environmental priorities played a certain role in the growth of demand for tin. Its ecological advantages make tin an alternative to lead and other toxic metals. As is known, starting in 2006 there will be a ban on the use of lead in various industries of EU countries: from radio electronics to mechanisms balancing weights. Obviously, lead in solders will be replaced. Compositions and brands of solders, in which the tin content has been brought to 97%, have already been developed and tested on the industrial scale. This can raise the use of tin by 15,000 tons year-on-year.
Despite its quite large reserves of tin ores, Russia plays a comparatively modest role in the worlds market of tin (Table 2). This is explained by the geographic remoteness of main deposits, their low tin content and complexity of ores concentration.
The leading Russian producer of tin is the Novosibirsk integrated tin mill, which fully meets demands of the domestic market. If with the start of reforms other nonferrous industries managed to quickly redirect their activity to foreign markets and, as a whole, to maintain and even increase production volumes, the tin making was a different case. Its production was down by almost 4 times. What is more, the Novosibirsk integrated tin mill also had to yield a part of the domestic market to the imported metal.
The first signs of the Russian tin industry getting out of crisis appeared in 2000. Like in other industries, this was linked to forming the vertically integrated structure and consolidating the raw material base. The Novosibirsk integrated tin mill acquired Vostokolovo, Khynganskoye olovo and Tyan-Shan olovo, tin-producing companies, which are developing their own deposits and which are engaged in reprocessing and concentrating ores. In addition, the mill also acquired a 15% stake in Russias largest tin-producing company in the settlement of Deputatsky (Yakutia).
In the opinion of Vladimir Sherstov, the chairman of the board of directors at the Novosibirsk integrated tin mill, even if all expenses, high cost of mining and big transportation costs are taken into account, reprocessing of the Russian raw material is more economically advantageous than importing tin concentrates. He stresses that it is possible to successfully solve a whole number of problems within the vertically integrated holding: to stabilize raw material supplies for the metallurgical production facilities, to make rational investments in developing the raw material base, to consistently reduce production costs through modernizing technological processes. This strategy made it possible for the enterprise not only to survive during the period of bad market economic conditions but to successfully use the chance for developing its business, when the worlds market began recovering in 2004.
Russian tin-producers supply their metal to mainly steel companies, which make tin-plate. In the first place, those are the Magnitogorsk Iron & Steel Works (Russia) and Mittal Steel Temirtau (Kazakhstan)
In 2005 the leaders of the Novosibirsk integrated tin mill are planning to raise supplies of its own raw material from 50% to 75% and increase metal production volumes by no less than 20% in the nearest two years.
The mills major project is connected with making complex products. That is chemical compounds. A line to produce 3,000 tons of stannic chloride for the glass industry will be put in operation already this current year. In order to make investments in this project, the joint venture Stannum Chemicals with participation of Great Britains trading company Russian Tin Sales has been set up. The products are expected to come to Europe, where Russians are planning to get no less than a third of the market in the nearest two years.
With existing world prices for tin the Novosibirsk mill is capable of accumulating profit for developing its raw material base and the concentration process stage, among other things. However, its own funds will not be enough so as to bring the ore mining and metal production to the level of the early 1990s. The Novosibirsk integrated tin mill has already obtained several credits from Russias Sberbank for the total amount of $14 million. It also became a guarantor of credits to the mill-controlled raw material enterprises totaling $10 million. Besides, its board of directors intends to attract additional investment resources through the bond loan for $14 million.
The strategic plan to develop the Novosibirsk integrated tin mill set for the period till 2007 provides for increasing the production of metal tin up to 6,000 tons a year; the volume of making alloys and solders is to be up to 3,000 tons. According to different accounts, the Novosibirsk integrated tin mill and its daughter enterprises possess licenses for developing tin deposits with the total reserves of over 190,000 tons. As a whole, the raw material supplies to them are ensured for no less than 30 years. This is the main competitive advantage of the integrated mill under the existing world conditions of the tin raw material shortage.
Table 1. World production of tin, thou tons
Country 1995 2000 2003 Share of world production
(2003)
%%
World, total 202.7 262 268 100.0
China 75 100 80 29.9
Indonesia 42.9 49.1 65.8 24.6
Thailand 9.8 17.3 14.9 5.6
Malaysia 38.2 28.9 14.3 5.3
Bolivia 18.1 11.1 12 4.5
Brazil 19.4 13.2 8.8 3.3
Belgium 8.6 8.1 8.5 3.2
Russia 13.1 3.8 5.8 2.2
Source: LME
Structure of tin consumption in Russia (Изобразить в виде круга, деленного на сектора )
%
Metallurgy 44
Engineering 17
Glass industry 17
Petrochemistry 13
Motor vehicle construction 7
Railroads 2
Source: Novosibirsk integrated tin mill
|
|
|
|
|
current issue

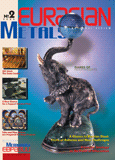
previous issue

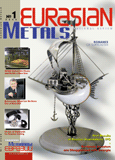
russian issue

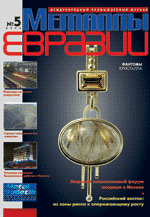
|
|