Yevgeny Khokhlov
Over the course of many years Russia has been the largest consumer of 1420-mm dia. longitudinal-welded ERW pipes for gas mains but not their producer. Due to orders from the Russian gas industry, a lot of Western steel companies managed to set up high-capacity complexes for the output of these products and ensure their stable utilization while Russia became deeply entrapped by the import dependence and forced to spend hundreds of million dollars annually on pipes purchase.
Now the situation is radically changing. In 2001almost simultaneously, with a break of one month, it was officially announced of the start of two big projects which are directed to the set-up of 1420 mm-dia. pipes production in Russia.
Russia is the largest gas supplier, it has the world-longest network of gas mains. This gas-transport system is continuously extending and being modernized. An annual demand of Gazprom for large-diameter pipes is hundreds of thousand tons. Gazprom places orders for the most expensive high-tech product, 1420 mm-dia. pipes, in the West. In Russia gas main pipes are produced by only three enterprises: the Vyksa Steel Works, the Chelyabinsk Tube-Rolling Plant and the Volzhsky Pipe Plant. So far none of them is ready to meet the requirements of the oil-and-gas complex for range, specification and service properties of tubes/pipes. It is beyond the capabilities of the equipment available at the Volzhsky Pipe and Chelyabinsk Tube-Rolling Plants to make tubes of up to 32 mm in wall gage and over 12 m in length while the Vyksa Steel Works, the only Russian producer of heavy-gage longitudinal-welded ERW pipes, can offer pipes of 1000-mm dia. maximum. This being the case, the main Gazprom suppliers, its partners in the most prestigious projects of the construction of transcontinental mains, like Yamal-Europe and Goluboy Potok (Blue Flow) are still companies from Germany, Italy and Japan
In order to understand the anomaly of the situation at large, one must recollect another circumstance. Russia has a mature steel industry at its disposal and ranks among the world steel export leaders. Then why did Russian steel companies producing 59 million tpy of steel give their foreign competitors this most profitable and promising niche in the market? The reply will be as follows: it so happened historically.
DIRECTOR OSADCHIY AGAINST GERMAN FEDERAL CHANCELLOR ADENAUER
The problem of pipes production for oil-and-gas mains in Russia exists at least four decades. But not always it was realized to a full extent. There were times when this disproportion of supply and demand seemed to be of no concern to anybody at all. But crises did take place.
The first mishap occurred at the climax of the cold war, in 1963. At that time, owing to political disputes with the first socialist country, the Federal Republic of Germany imposed an embargo on supplies of large-diameter pipes to the USSR. But there is sense in the saying that while wasting opportunities in the normal circumstances Russians are able to master all their strength in the most irremediable situations.
The winner in that confrontation was Yakov Osadchiy, Director of the Chelyabinsk Tube-Rolling Plant. He was one of many engineers who made a career in the planned state economy but with an ability rare for a Soviet manager he could keenly feel forthcoming changes in the market and bravely violated crusted production stereotypes. Already five years prior to those events in endless debates with design institutions, he managed to prove that it was necessary to install an additional forming line in the electric-weld tube shop. It was this line that became the basis for the construction of a 1020-mm mill. In a record time Chelyabinsk began mass-lot production of 1020 mm-dia. longitudinal-weld ERW tubes equivalent to German ones. The first tube had a chalk mark on it to the effect: "Truba tebe, Adenauer (Go to blazes, Adenauer)!" a play of words (the Russian word "truba" is translated into English as "pipe") meaning an all-around failure.
The first lot was directed to the construction of the Bukhara-Ural gas main. Further on, the Chelyabinsk Tube-Rolling Plant made 23 million t of 1020 & 1220 mm-dia. tubes/pipes. They were applied in the construction of the longest pipelines, among them, the well-famous Druzhba (Friendship) oil main pipeline, the Central Asia-Center, Urengoy-Pomary-Uzhgorod, Surgut-Polotsk, Siyanie Severa (Lights of North) mains. A decade after the relations between the West and the East became warmer. And again the policy produced a powerful effect on the large-diameter pipes market. A symbol of the epoch of detente became, as it was named at that time, a project of the century "gas in exchange for pipes". The period of long-term cooperation between Gazprom and Mannesmann began, continuing up to now. But anything good has its portion of bad, and vice versa. In opposition to the embargo that was an excellent incentive to Russian steelmakers for a process bound, the guaranteed supplies from the West decelerated the progress of the Russian tube/pipe industry for a long time.
SELECTION OF FREE MARKET
With the start of economic reforms the situation in the Russian steel industry began to change rapidly. Liberalization of foreign trade made it possible for producers to trade in their own products in the foreign markets at free prices. It at once brought about earnings in hard currency exchanged for rubles at a very favorable rate. However, the euphoria due to export success lasted not long. Very soon the independent producers began to fall into the orbit of antidumping sanctions. The economic reality forced steelmakers to change priorities and make out a long-term strategy with an eye to Russian consumers.
The industrial lobby representing the interests of big steelmakers made the government seriously treat the problem of setting up a modern complex of tubes/pipes production. At that time, the embargo story of 1963 was recollected. The experts took this precedent to come to an obvious conclusion: extra dependence of Gazprom on import purchases is too risky. And this is not only the problem of the company but a matter of economic security of the state.
In summer 1999, the Ministry of Economy of RF held an extended meeting on the problem of the construction of a tube-weld complex. The biggest steel producers, among them, the Magnitogorsk, Cherepovets (Severstal JSC), Lipetsk and Nizhny Tagil Iron & Steel Works were examined as applicants for the participation in the contest. In November, the discussion was prolonged in Nizhny Tagil (Ural). There a letter of intent was signed between Rem Vyakhirev, Chairman of the Board of Directors (Gazprom) and Sergey Nosov, General Director of Nizhny Tagil Iron & Steel Works. A note that substantiated the construction of a large-diameter pipes complex in Russia was sent on behalf of Vyakhirev to the Prime Minister (at that time it was Vladimir Putin). In April, 2000 the Governments resolution was issued on the set-up of a Large-Diameter Pipes Plant JSC in the town of Nizhny Tagil.
In parallel with organizing work, a discussion on the technical aspects of the project and the requirements for future products was on. In this connection, it would be interesting to cite two opinions given in Metally Evrazii (published in Russian in Moscow since 1996). Nikolay Bogatov, an authoritative expert in tube/pipe production, pointed out that 1420 mm-dia. imported pipes had insufficient reliability and inadequate service life, and it caused premature failures in operation of pipelines. This being the case, it is expedient not to apply foreign process flowsheets but to use radically new criteria and parameters. Professor Oleg Steklov, President of the Russian Scientific & Technical Welding Society, is of the opinion that domestic processes are not far behind the world level. Both the Chelyabinsk Tube-Rolling Plant and the Volzhsky Pipe Plant make use of quite up-to-date methods. But at the stage of transition to new high-strength materials one must think of welding techniques based on other physical solutions.
At last the set-up of gas main pipes production began to be considered a national task. It was responded to by state authorities, science representatives and steelmakers. But only a powerful industrial corporation could implement such a large-scale project.
In the second half of the 90s, after the period of chaotic privatization and dissipation of property, integration processes began in the Russian steel complex. Big companies started to be formed. EvrazHolding, a dynamically developing trader group, became prominent. It established its control over three integrated works with a total production tonnage of 14 million tpy of steel. The biggest up-to-date plants in the tubes/pipes industry joined Obedinennaya Metallurgicheskaya Kompaniya (United Metallurgical Company) or OMK. These two structural formations claimed their readiness to set up 1420 mm-dia. pipes production operations. It resulted in the appearance of two competing projects in Russia.
EVRAZHOLDING: AS IN EUROPE ONLY BETTER
A decision on the construction of a large-diameter pipes plant in Ural was taken on the basis of all-around studies and examinations. The most authoritative scientific and design organizations took part in them: Institute of Metallurgy of the Russian Academy of Sciences, Central Research Institute of Iron & Steel Industry, Gipromez and other institutions. The new complex is unrivalled by any investment project in this country for scope, cost and process intricacy. The specialists of Hatch, a consultant to the US banks in steel projects, even think it to be the biggest project of world steel industry for the last decade.
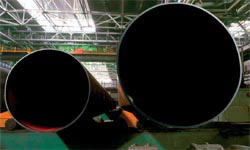 |
The Nizhny Tagil Iron & Steel Works. The largest diameter pipes plant wilt be build at this site. |
For this project to be implemented, Large-Diameter Pipes Plant (Zavod po proizvodstvu trub bolshogo diametra ZTBD), a joint-stock company with the participation of state and private capital, was formed. The state has a controlling block of shares 25 % plus one share. A similar share part belongs to the main executor NTMK JSC. Gazprom, a future consumer of the plant products, has 19.9 % of shares. The shareholders also include a potential investor Dufenco (Switzerland) which has 30.1 % plus 2 shares.
Sergey Nosov, General Director of ZTBD, is convinced of the success of the project. He indicates three main competitive advantages. First, high steel quality: NTMK is the only Russian steel works that does not use return scrap in basic oxygen steelmaking. Hot metal is made from V- and Ti-bearing ore. A unique naturally-alloyed steel is obtained in this way, which is capable to service under heavy loads and in low temperature (down to minus 70oC). Second, NTMK has a ready-made site where the entire production complex will be compactly arranged it will save a lot in the costs of construction and subsequent operation. Third, a geographic factor has been taken into account: the plant will be located relatively near the main oil & gas fields, on the crossing of transcontinental gas pipelines and it will ultimately reduce pipe transportation costs.
A network of gas mains established in Russia is the most powerful in the world. It unites all the fields of the CIS countries and provides gas export to the European countries. The Russian gas pipelines extend for 150,000 km, and their overall throughput capacity is more than 600 billion m3 of gas.
The new plant will comprise the following main units: a 5000-mm mill for wide plate production by controlled rolling, a electric-weld tube mill shop where the plate will be formed into the UOE tube, a coatings department with three-layer external and smooth internal protective coating technologies.
The5000-mm mill capacity is 1.5 million tpy of plate. The plants requirements will not be over 1 million t. Thus, about 500,000 tpy of high-quality plate could be sold to other customers.
Pipes of up to 40 mm in wall gage and up to 18 m in length will be made by a forming technique which is the most up-to-date at present. The pipes will be an equivalent to the product made by Europipe. It is clear that in this time a lot of innovations appeared in steel industry processes, and the participants intend to introduce a number of improvements to go beyond the European prototypes: to make the production operations more saving, and the products of higher quality.
A significant event took place in February, 2001. During the state visit of President Vladimir Putin to Austria, a contract between NTMK JSC and Voest-Alpine (Austria) was signed. It deals with the construction of CCM No.4, the first large unit in the 1420 mm-dia. pipes complex. At the same time, SMS Demag and Voest Alpine signed a letter of intent with NTMK JSC on envisaging further joint work, namely, the construction of the 5000-mm mill and the electric-weld tube shop. During the negotiations the interests of the Russian side were represented by the shareholders of NTMK JSC EvrazHolding and Duferco. They were lucky in bringing the partnership to the level of confidence and responsibility pertaining only to the relations of Western companies among themselves. The contract deserves the highest appraisal. Both the amount and the conditions of the credit are unexampled. For the first time in the process of market reforms, a Russian industrial company is granted a free credit from a foreign partner for a term of 7 years with a considerable delay in return: the first payment shall be made after the CCM starts operation.
Thirty-one million out of 86 million Euro will come directly to Russia where a substantial portion of orders will be placed. From its end, Voest-Alpine is committed to supply the main equipment and technologies as well as to arrange financing of the project through attraction of syndicated credits of several European banks and, partially, inputting its own funds.
On the eve of the new 2002 year, the Government of Russia transferred its share to the authorized capital of ZTBD, that is, 300 million rubles (about US$10 million). So, apart from financing, the project obtained an explicit moral support. As claimed by Sergey Nosov, the state thus demonstrated a certainty that the invested money would not be wasted.
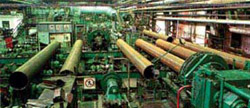 |
The electric-weld tube shop of the Vyksa Steel Works: one of the main units of reconstruction within the framework of Alliance-1420 |
ALLIANC-1420: SELF-RELIANT
The initiators of an alternate project, Obedinennaya metallurgicheskaya kompaniya (OMK) and Severstal JSC, stress their independence. They set up 1420-mm dia. pipes production operations at the cost of own funds, maximizing the utilization of their production facilities and requesting no extra guarantees from the future customer, Gazprom.
Severstal and ��� already have some experience of cooperation. Seversral is the Russias largest producer of skelp (strip for electric-weld tubes), and the OMKs plants, the Vyksa Steel Works and the Chelyabinsk Tube-Rolling Plant, are the main consumers of this product. Annually they require over 1million t of skelp. This interrelation became the basis for the development and deepening of the partnership. The companies concluded a strategic market alliance and pursue a coordinated technical policy. In the process of cooperation, new steel grades were developed, a commercial output of cold- and corrosion-resistant tubes was put into practice, critical orders for oil & gas complex were fulfilled.
The agreement between OMK and Severstal JSC on the set-up of a joint venture was signed on June 28, 2001, and immediately after that the implementation of the project named "Alliance-1420" started. The companies work at par, the share of each is 50 %. The investments are approximately equal. Severstal works at the modernization of the 5000-mm mill and guaranteed output of 450,000 tpy of plate at the first stage of the joint program with a subsequent capacity build-up to 850,000 tpy. OMK will deal with the reconstruction of Electric-Weld Tube Shop No.4 at the Vyksa Steel Works.
This shop is one of the most up-to-date in the Russian tube/pipe industry. It was built in 1993 and designed for the output of 530-1020 mm dia. electric-weld tubes (with one longitudinal seam) of up to 32 mm in wall gage and up to 12 m in length. The design capacity is 1 million tpy, inclusive of 150,000 tubes with a three-layer external protective coating. All the products have been certified by API, with a quality assurance system according to ISO 9001:94. Sergey Chekalov, technical Director of Alliance-1420, pointed out several advantages of the shop reconstruction program in his interview to the correspondent of Eurasian Metals. It will permit not only the existing production cycle to be retained but also an implementation of the entire combination of reconstruction steps without the downtime of the main production unit, the electric-weld tube mill. As a result, two parallel production flowsheets will be in operation: one for the production of 520-1020 x up to 32 mm tubes, and the other for 914-1420 x up to 40 mm pipes. There will be no need to construct new industrial buildings, the existing production infrastructure will be utilized. This money-saving scheme permits a substantial reduction of costs for the set-up of the new production operations and a minimization of the construction time.
The standard tube made by the Vyksa Steel Works is 12-m long. Tubes of this size account for 80 % of Gazproms purchases. The project provides for the production of 18-m long tubes with one butt joint. This welding operation will be shop-made, on a circular welding machine, with thermomechanical treatment and required testing techniques. The circular weld technology has been coordinated with Gazprom. It also permits 24-m long tubes to be produced. This variant is in-principle profitable to the customer as it makes it possible to reduce 1.5-2 times a number of butts to be field-made.
In December, 2001 OMK signed a contract with SMS Meer for the supply of a press forming equipment for the production of 1420 mm-dia. pipes. Referring to Dr. Helmut Fricke, President of SMS Meer, the OMK press office states that this equipment has no analog in the world. It is capable of producing 40 tubes of up to 40 mm wall gage per hour. The contract value is US$30 million.
The overall amount of capital investments in the implementation of Alliance-1420, including the equipment cost and expenditures on contracting works, is estimated by experts at no more than US$300 million. Severstal and OMK whose turnover is assessed at billion dollars would be able to invest at the expense of own funds. Nevertheless, they believe that the promise of rapid payback will help to attract credits of Russian and foreign banks: judging by the companies estimations, the new complex will bring first profit already three years after the start of products supply.
The claimed design capacity of the complex for 2006 when the reconstruction is to be completed is 2.9 million t of oil & gas main pipelines, including up to 860,000 t of 1420 mm-dia. pipes.
The joint venture managers, showing trust in their own powers, claimed that the first 1420 mm-dia. pipe will be made 1000 days sharp after the start of the work on the project. OMK even issued a unique souvenir, a calendar in the form of a tube section for two and a half years ahead, including the 24th of March, 2004 the date when the claimed thousand of days will expire.
EACH HAS ITS OWN DISADVANTAGES
Both competing projects have advocates and opponents. The point here is not only the companies representatives or structures connected with them, independent experts also express opposite opinions.
As considered by critics of the Nizhny Tagil project, it raises no doubt from the technical viewpoint but is economically unreal. In this case the opponents proceed from the Soviet practice of similar complexes when construction lasted for over 10 years, with a corresponding indefinite delay of the start of production. The project cost (US$1.5 billion) is also unprecedented: in Russia equally large investments have never before been involved.
On the contrary, Alliance-1420 looks quite attainable in investments. But it has some vulnerable technical and organizational spots.
The first point is the limited performance of the 5000-mm mill built in 1985 for meeting the requirements of machinebuilding. Severstal acquired its property from United Machinebuilding Plants and intends to revamp it for the production of tube plate. But some specialists doubt the possibility to settle this technically difficult task, noting that the mill design proper is obsolete and cannot be suitable for the rolling of this plate type.
The second point is the necessity to transport plate at a large distance from St.Petersburg where the 5000-mm mill is located till the Vyksa Steel Works in the Nizhegorodskaya Region. The most convenient way is to make use of a river and canal system well-developed in Russia but it is in operation only in the navigation time lasting for six months a year. The railway transportation requires special jack-equipped freight cars permitting wide plates numbering 100-150 pcs. to be arranged in an inclined position. Special routes, patterns and timetables will have to be compiled which will greatly raise the production costs and, consequently, the product cost.
In comparison with this variant, the project to be implemented in Nizhny Tagil seems perfect: the entire complex of production units is arranged at the site that can be easily covered with an eye.
There is also a conciliating viewpoint in the discussion where the major part of opinions sounds categorically, refuting one or the other project. It may be reduced to the following. Both production complexes will be called for in the Russian economy under recovery now. As assessed by Vadim Antipin and Nikolay Savchuk from Chermetinformatsia Institute, an annual demand of Gazprom for 1420 mm-dia. pipes will be 1000-1200 thou t by 2010, that is, it will exceed the capacity of each individual complex. Apart from it, the plate products will be required by other sectors, for example, construction of marine drilling rigs, tankers, icebreakers, oil terminals, power-generating units and, certainly, the military-industrial complex is still a big customer.
By forecast estimation, the total natural gas reserves in Russia are 236 trillion m3, with 61.2 trillion m3 in the fields already explored by geologists. In the preceding years 9.5 trillion m3 in total have been produced, and, consequently, the available reserves will not be depleted for many decades. The regions of Eastern Siberia and water areas of northern seas are considered to be most promising.
Yet the decision will be made by Gazprom. This largest company has not yet selected any project offered to its attention. The interaction of this gas giant with the steel companies so far takes place preferably in the technical aspects. A working team with the participation of OMK and Gipromez representatives has been formed in order to define possible requirements of the gas industry for large-diameter pipes. As to the Nizhny Tagil project, the Gazprom managers also made an important step signed a constituent agreement on the set-up of ZTBD JSC. However, the future pipes producers expect the main thing future contracts. Maybe, the reluctance of Gazprom to be bound with concrete commitments is due to the eagerness to continue the previous policy of foreign purchases of pipes in exchange for supplies of gas. As believed by analysts, this non-committal was one of the reasons due to which Rem Vyakhirev had to leave the leaders post.
|