Yulian Yusfin, Nikolay Pashkov
Professor, Moscow State Institute of Steel&Alloys
Nowadays the greater part of steel (95 %) is produced by a two-stage route: in blast furnaces hot metal is made from ore, and then steel is melted from it, with an addition of scrap. This production flowsheet developed almost 150 years ago features high capacity, low consumption of resources, variety of products. A long search for direct iron process when steel is made from iron ore in one unit convinced the majority of experts that this way yields no promise. The result was an inefficient and high resource-intensive output of low-quality product.
However, the research experience was not wasted. It has been transformed into the solution of a different task the replacement of the blast furnace (BF) as a primary metal producer. The blast furnace is a highly-efficient production unit. It shows high iron recovery rate (over 99 %), low consumption of resources (in particular, energy ones), and high production rate with relatively low environment contamination. The blast furnace has only two big limitations. As the run-of-mine ore is, for the most part, composed of small-size fractions pelletizing is required. It brings about high energy consumption and emissions of solid particles into the air. Besides, in the world there are limited reserves of coking coals with many countries having no reserves at all. Moreover, cokemaking is not environment-friendly. That is why, an alternate plant used instead of BF gives an opportunity to develop a national steel industry in many countries.
Here other aspects shall be taken into account:
a striving for more rational use of fuel-and-energy resources, possible increase in the share of gas, oil and noncoking coals consumed in steel industry,
limited stock of scrap of required cleanness and stable composition,
possible achievement of higher steel quality through application of metallized raw materials instead of scrap (it is of common knowledge that metallized raw materials are clean in harmful impurities, especially, non-ferrous metals),
possible set-up of low-capacity steel industry (mini-mills) and widening of regions of profitable steel production based on metallized raw materials.
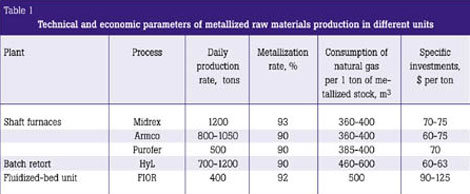
Non-blastfurnace ironmaking, which is sometimes, as before, named "direct iron reduction", is a variant of the two-stage processes divided into two large groups: solid-phase and liquid-phase ones. In solid-phase processes, oxygen is removed from iron oxides by gaseous or solid reductant at temperatures below the melting point of charge components. The reduction product is named sponge iron or metallized pellets. In the high-temperature process, iron is reduced at the melting point of oxide and metallic phases.
Most often, sponge iron is used as a high-purity addition to steel scrap during melting in electric arc furnaces (EAF) as well as for scrap replacement in the case of its shortage or high prices. The most stable demand for sponge iron is reported in the countries with inadequate BF facilities and steel scrap stock. Sponge iron is of less importance in steel production of industrialized European countries, Japan and the US where iron ore, steel scrap and solid fuel are still relatively cheap.
For iron reduction plants, the processes using shaft furnaces (in the main, Midrex, HyL-III) and batch retorts (HyL-I and HyL-II) are the basic ones. Let it be noted that for shaft furnaces, as for BF, pelletized raw materials are required. Lately, the processes based on rotary furnaces and solid reductants (SL-RN, Krupp-Izensvam, Kawasaki, etc.) find some industrial application, for the most part, in the reclamation of steel waste dust and sludge containing impurities of zinc, lead, etc., and in the processing of complex ores rich in Ti, Cr, Mn, etc. and unsuitable for BF. Dust ore can be used in rotary furnaces but it is critical from the ecological viewpoint.
The fluidized-bed processes are less widely used owing to their peculiarities: high requirements to fraction size, gas dynamics restrictions for fluidized bed, temperature conditions, etc.). The fact that Midrex and HyL direct iron processes are predominantly developed in the world practice stems from their better technical and economic parameters (Table 1). Presently, Midrex and HyL processes account for about 80 % of world-produced metallized pellets, including 60-65 % of Midrex pellets. In Russia this process has been put into practice at the Oskol Electric Steel Works (OEMK).
Non-blastfurnace ironmaking plants are built, for the main part, in developing countries with comparatively low steel demand in the market, limited investments, low resources of scrap and coking coals as well as large reserves of iron ore and natural gas.
When assessing the outlook for the development of non-blastfurnace steel production processes based on the replacement of hot metal with sponge iron, the circumstances depicted below must be borne in mind.
The metallized pellets production processes run in the solid-phase region without slag formed. Therefore the barren rock is not removed. The same is fair for associate elements. With larger portion of barren rock, the meltdown of metallized pellets in EAF is accompanied by greater loss of iron with slag, and, which is the main thing, by substantially larger consumption of electric power. The practice of sponge iron melting in EAF showed that it is economically feasible to produce steel from metallized pellets if they have no more than 3 % of barren rock. So, the first prerequisite of sponge iron production in shaft metallization furnaces is the rich or easily-processed ore.
Quality of steel depends on impurity elements present in it: S, P, Cr, Ni and other non-ferrous metals. Therefore the second prerequisite to be taken into account in the production of sponge iron is the cleanness of the ore in impurity elements. The major part of ores and concentrates used in the production of metallized pellets has no more than 0.02-0.04 % P, below 0.02 % S, with a total content of non-ferrous metals of below 0.02 %. The composition of ores and oxidized pellets used in the production of sponge iron is given in Table 2.
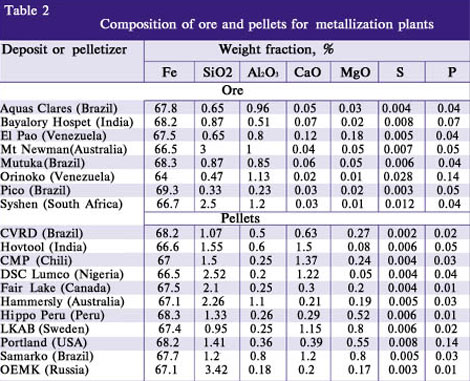
A gaseous reductant is applied for the reduction of iron oxides in the shaft metallization furnaces. Nowadays the reducing gas is produced by air, carbon dioxide or steam conversion of natural gas. Depending on conversion type or combination of types, a gaseous reductant containing a certain ratio of carbon monoxide and hydrogen is produced.
Taking into consideration that the processes of gasification of solid and liquid fuel still wait their designers, in the near future the gaseous reductant can be produced mainly from natural gas.
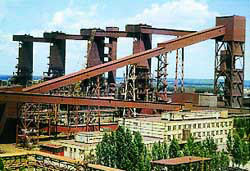 |
The Oskol Electric Steel Works is Russias only plant of BF-free ironmaking. The metallized pellet production plant. |
So, the third prerequisite for metallization of iron ore materials in shaft furnaces is the availability of natural gas resources. No wonder that the construction of non-blastfurnace steel projects is intensely under way in the Middle East and Latin American countries as well as in Indonesia.
In 1997 the world production of metallized raw materials was 31.2 Mt. In 2005 the production of direct-reduced iron (DRI) will reach 53 Mt. The world market of commercial metallized raw materials is developing. In 1995, 7.6 Mt of DRI was land and sea transported to the regions with a negative balance of clean metallic charge. By 2005, the world demand for metallized raw materials is estimated to be stabilized at 27-29 Mt. The good market shows promise for investments in this conversion stage.
A transition to the construction of sponge iron-based integrated mini-mills became evident as early as in the 70s. It is connected with the fact that with comparable energy-intensity the shaft furnace EAF route has the following advantages:
lower scale effect. The BF basic oxygen furnace (BOF) route is economically effective at a production tonnage of 3 Mtpy, as a rule, while the shaft furnace EAF route already at 300,000 400,000 tpy;
lower cost of main facilities. The investments in the BF BOF route and the shaft furnace EAF route is US$750 and 380 per tonne of conticast billet, respectively;
lower manpower. At a plant capacity of 1 Mtpy of primary metal, this indicator is 2.6 and 1.2 man-hour per tonne for the BF BOF and shaft furnace EAF routes, respectively;
opportunity of speedy commissioning within 20 months from the construction start.
The production of sponge iron grew at a rapid pace, with 37 Mtpy in 1997 against 15.8 Mtpy in 1989. After that, the growth rate declined essentially. Thus, in 1998 the build-up as only 4.1 %, and the utilization rate of production facilities equal to 88 % in 1996 fell to 82 %. None the less, a high level of investments in the set-up of DRI facilities was retained. For the last two years, these facilities increased by 7.5 Mtpy (20 %), and the growth is most likely to continue despite the cancellation or delay of several projects. In the coming years new 10-Mtpy facilities will be put on stream.
Yulian Yusfin
Professor, Moscow State Institute of Steel&Alloys
Dr. of Sc.(Eng.), Prof. Yulian Yusfin is an author of 471 scientific papers, among them 15 books. He has 108 inventors certificates and patents. Specialty: preparation of ores for melting and iron metallurgy. Full member of New-York Academy of Sciences, correspondent member of Russian Engineering Academy. Head of department in Moscow Institute of Steel & Alloys since 1987. Prepared 35 candidates and 2 doctors of sciences. His theory of high-temperature strengthening of iron-ore pellets is well-adopted. He established a concept of widening the terms of reference of steel and nonferrous metals industries with an incorporation of energy and sanitary & ecological functions, along with a metallurgical one proper.
| |
| |
|
Late in the 80s, BF-free liquid metal production technologies, usually united as liquid-phase processes, became firmly established in the world steel industry. The Corex process developed in Germany and operating in South Africa, South Korea and India is applied on an industrial scale. A hot metal production module is a blast furnace cut into two halves. The upper part is used as a shaft furnace where lump material (sinter, oxidized pellets, coarse ore) is reduced to the highest (about 90 %) metallization rates. In the second unit (the lower BF part: the hearth) metallized pellets are melted, the metal is recarburized. Here the fuel is the lump coal burnt in the oxygen blast flow, and the gas produced as a result of incomplete combustion is the reductant.
The main advantage of this technology is the replacement of coke with coal ranks not in short supply. The main disadvantages are high consumption of utilities (1.5 2 times higher than in BF), loss of associate elements with slag, impossible production of foundry iron and ferroalloys, and ambiguous ecological effect. Let it be noted that the Corex process clears one of the limitations of the BF process: coke is replaced with coal, but the problem of elimination of the ore pelletizing stage from the traditional steel production flowsheet is not solved. Due to these reasons, the Corex process seems to find no wide application.
In our opinion, the Romelt process developed in Russia is more attractive. It permits a production of hot metal from non-pelletized ore and coal in one unit. This technology is extra viable in processing of technogenic raw materials and gasification of coal. A plant using this technology is being designed for India.
The practice of the last decades affords a statement that the BF-free ironmaking has significantly widened the abilities and found its own place in the world steel industry. For natural gas-rich regions, it is a metallurgical technology of wide application range but of low production tonnage, which depends mostly on the quality of iron-ore raw materials. For countries without coking coal resources and not rich in gas, it is, for the most part, liquid-phase processes meeting minimum requirements for iron.
Along with it, the majority of experts is inclined to believe that the traditional and alternate technologies of steel production do not compete, supplementing each other to a larger extent; here the share of BF-free methods of steel production is apparently stabilizing, with a future outlook for 10 20 % of the total world figure.
|