There is no aircraft industry in Kazakhstan. However, it is where the raw material (titanium sponge) for critical parts of engines and fuselage parts is produced. The Ust-Kamenogorsk Titanium and Magnesium Plant (UKTMP) JSC is one of the world largest producers of titanium sponge. Most of the producers of titanium components for aerospace in the world use UKTMP sponge. The most interesting feature of this plant located far from the raw material sources and main markets might be the ability of its staff to maintain high competitiveness due to their high skills, diligence and persistence. Anyhow, this was the impression that Sergei Oposhyansky and Yevgeny Khokhlov, Eurasian Metals journalists received on the basis of interviews with the staff and the detailed information obtained from the company.
SELF RELIANCE
Ust-Kamenogorsk Titanium and Magnesium Plant was built in 1965 with the latest technology and became the leading titanium sponge producer of the USSR titanium complex. The raw material titanium slag and dehydrated carnallite was supplied to UKTMP from Berezniki Titanium and Magnesium Plant (Russia) and Zaporozhie Titanium and Magnesium Plant (Ukraine), and produced titanium sponge was shipped for further processing to titanium metal and alloy producer Verkhne-Salda Metallurgical Production Association (Russia).
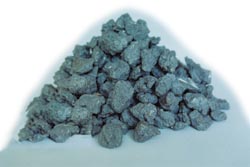 | Titanium sponge | In early 90-s, the plant gained full economic independence, but lost its traditional suppliers of raw materials and the main customers. Former partners turned into competitors, and the plant management faced a number of challenges: to find new suppliers of raw materials and customers for its products, to update the manufacturing process, to certify the products and ensure steady market.
Within a short time, the plant experts, ministries, professional organizations and scientists of Kazakhstan devised the program of development of its own titanium industry that was approved by the Kazakh Government setting the following directions:
establish domestic mineral base for titanium industry;
construction of metallurgical plant to process primary titanium feedstock;
increase of technical level of production and improvement of quality;
reduction of pollutant emissions.
As of today the basic goals of the program have been achieved.
Reserves of three titanium deposits with commercial value have been explored and approved: Shokash in Aktyubinsk oblast, Obukhovsk in Akmolinsk oblast, Satpayevsk in Eastern Kazakhstan oblast, their development started already.
Exploration at Satpayevsk deposit was performed using UKTMP funds. Reserves were approved in 1999. Additional exploration in 2000-2002 by Kazakh and Japanese geologists showed an 80 % increase of the reserves of this deposit. An independent mining enterprise Satpayevsk Titanium Mines Ltd. was established here. As of now, the open pit has been developed, a pilot concentrating plant has been constructed. Ilmenite have been produced.
In October 2000, an ore smelting furnace for titanium slag was commissioned at Ust-Kamenogorsk Titanium and Magnesium Plant. Commenting this event, Alexandr Cheprasov, UKTMP Technical Director, emphasized its extreme importance for the whole manufacturing cycle. The construction of the ore melting complex was started in late 80s, but was completed only recently. It consists of 28 facilities. The plant started production of its own raw material for titanium sponge. An integrated scheme was established. Tens of thousands of tons of titanium slag were produced since the complex has been operational. Its quality was found to be better than the imported raw material.
The UKTMP main product: titanium sponge for various applications.
The plant produces also magnesium ingots and magnesium powder. The plant can produce additionally vanadium pentoxide, scandium oxide, scandium metal, hydrochloric acid, potassium fertilizers, calcium hypochlorite, TiO2 pigments.
|
|
During that period, the technical renovation of production facilities was continuing with implementation of advanced R&D developments including a microprocessor based process control system. Per unit capacity of the basic manufacturing equipment significantly increased, the plant can now process a wider range of various raw materials.
Development of technologies and decrease of production costs, certification of products and quality system and successful marketing allowed the plant to take its own place in the international aerospace production cycle. Having resolved the above problems the plant stabilized its financial and economic position. Vera Kim, the Financial Director, confirmed that the company has no overdue debts, uses its own funds for the production and commercial cycle, and reached high efficiency.
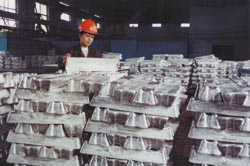 | Magnesium ingots | AUDIT STARTS FROM THE SKY
The UKTMP making its way to the world market as a seller of titanium sponge was going simultaneously with certification of conformance of this product to the requirements of new buyers. The first certification phase for commercial application was performed in 1994-1995 by Sumitomo, Kobe Steel, Nippon Steel, Deutsche Titan and others. Aerospace companies conducted numerous audits. They confirmed the existing quality control system and approved the plants product. The UKTMP brand was recognized by UK, Germany, China, USA, France, Japan. The high quality of Kazakh titanium sponge ensured its application in products for chemical, shipbuilding and automotive industries as well for production of sporting and consumer goods.
It could be regarded as a significant commercial achievement. However, the priority was to enter in the most prestigious and profitable sector of the titanium market, the aerospace industry.
During 1995-1998, the premium grades of titanium sponge were certified for aerospace application.
Long term agreements with leading world companies placed UKTMP as the leading supplier for the aerospace industry.
In 2000, UKTMP was granted a certificate for the quality management system in accordance with ISO 9002 by TUV. Further improvement of the quality management system resulted in the certificate of conformance of the quality management system to AS9100 issued in March 2002. The certificate was issued by BVQI (Bureau Veritas Quality Internationals) accredited by the US RAB.
Companies of the aerospace industry prefer to work in accordance with their own specifications. Each customer has its own requirements for titanium sponge, and all of them are fulfilled. Mikhail Yakutov, the Deputy Technical Director for Quality and Certification, explained that the companies check not only the products sizing and chemistry, but also the manufacturing processes. They look at the whole manufacturing cycle from arrival of raw materials. If the plant is planning to make some changes it must get approval of its customers. Although the process is being continuously improved all the rules are strictly followed. The aerospace industry auditors who studied the manufacturing process at Ust-Kamenogorsk Titanium and Magnesium Plant rated highly the well maintained and clean production facilities for titanium sponge.
With the support of the Government of the Republic of Kazakhstan, UKTMP and its management company, Specialty Metals Company of Belgium, gained revocation of the antidumping duty (83.95 %) on imports of titanium sponge to the USA established two decades ago.
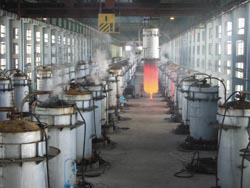 | Distillation department: the main product titanium sponge is produced here | Due to persistent technical and marketing policy, UKTMP increased output of high grades of titanium sponge to 90%. But the commercial and military aerospace market is highly cyclical. During the last period, due to slowdown of the world economy, production in the aerospace industry decreased. It was necessary to look for alternative applications for titanium products. Oil and gas industry in Kazakhstan is developing rapidly. It will need new offshore platforms, modern drill rigs, and other equipments. Titanium products due to their high strength-to-weight ratio and corrosion resistance may find wide application.
Bagdat Shayakhmetov
The President of Ust-Kamenogorsk Titanium and Magnesium Plant (UKTMP) JSC. 56 years old. Devoted to his profession and his plant. In 1969, after being granted a diploma of engineer, started his career at UKTMP, went through all stages of the management hierarchy to directorship. From July 1995 he became President of the joint stock company. From 1996 to 1998 created and headed the Kazatomprom National Nuclear Company, and simultaneously continued to be the President of UKTMP.
| |
| |
|
Arrangement of large scale production of TiO2 pigments at Ust-Kamenogorsk Titanium and Magnesium Plant could be a promising direction. There is significant reserve of capacities at the plant for pure titanium tetrachloride production (feedstock for pigment production), gas purifying facility, power and transport facilities. This complex allows for production of up to 80,000 tpy of TiO2.
 | Ore melting furnace: one of the units of the metallurgical division. Commissioned in 2000 | ASSESSMENT OF HIGH TECHNOLOGIES
Recently, a group of UKTMP specialists headed by Bagdat Shayakhmetov, the President of the Joint Stock Company, was awarded the State Award of Kazakhstan for the complex of R&D and implementation of innovations in titanium sponge production, as well as for mastering of output of new products. To explain the importance of this award, Stanislav Chaikovsky, one of the prize winners, suggested a look into its history.
There is a R&D division at the plant that in cooperation with the leading institutes of Russia and Kazakhstan implemented many improvements in each manufacturing division. Thus, for example, a new design of titanium chlorinators was developed resulting in doubling capacity of these units, but above all, it opened the possibility to use various types of raw materials while maintaining the high quality.
When UKTMP was lacking traditional raw materials, it had to adjust its technology to rutile and titanium slag sourced from Australia, Africa and Canada. The new raw material differed significantly in chemistry and quality, however, it is this circumstance that favored creation of the flexible manufacturing scheme becoming later an important factor of the commercial success.
The manufacturing process produces some waste, containing a valuable element vanadium. The plants experts passed through a number of research stages trying to extract it. The developed technology allows not only to recover vanadium in the form of pentoxide but also in the form of chlorides that can be used as catalysts in the chemical industry. It is a profitable production.
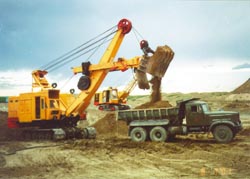 | Mining of ilmenite sands at Satpayevsk mine | The R&D facility allows the successful increase of the level of environmental protection. UKTMP experts established the water recycling system and stopped discharging industrial water into the Irtysh river.
Soil and underground water contamination is being reduced. To fully exclude filtration of harmful substances, the plant is constructing a dumpsite for waste using special impervious materials.
In order to reduce atmospheric emission the gas purifying equipment manufactured from titanium at the plant is being updated. Such equipment does not corrode and therefore less maintenance is required.
One of the R&D directions is focusing on the utilization of waste accumulated in the past.
In conclusion: UKTMP accounts only for less than 2.5 % of the total emission of the plants in Ust-Kamenogorsk. Nevertheless, the plants experts are planning to reduce further this figure.
|