Alexander Vatulin General Director, All-Russian Research Institute of Inorganic Materials (VNIINM)
Andrey Bochvar, an outstanding scientist, headed the development of new materials and their production technologies from the start of the implementation of the Russian atomic project. Fissile materials light actinides and alloys on their base #&150; were the research object. Despite the applied orientation, the entire materials science research in All-Russian Research Institute of Inorganic Materials (VNIINM) Moscow, was of fundamental nature, and the findings have not yet lost their urgency.
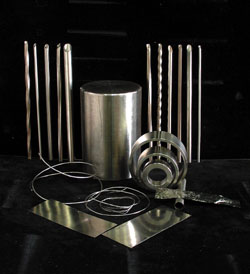 | Specimens of commercially produced Zr-alloys items |
The structural reactor materials are subject to active irradiation, the effect of high-value energy carriers, nuclear fuel fission products and thermomechanical loads. Irradiation defects are gradually accumulated which ends in the change of original mechanical properties. In the development of innovative materials, the main objective is to ensure allowable variations of these values dictated by the requirements to fuel elements and assemblies as well as other reactor parts.
At present, the foundation of the world nuclear power industry is pressurized or boiling water-cooled thermal reactors. The Russian achievements include the development and successful commercial operation of a BN (fast neutron)-600 sodium-cooled fast reactor. A higher-power BN-800 reactor is under construction. A ‘Brest fast reactor project featuring improved safety with lead coolant and a station fuel cycle is being elaborated.
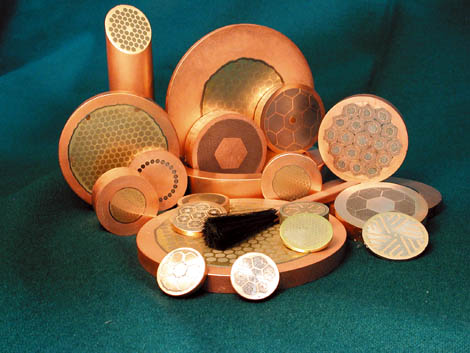 | Novel designs of Nb3Sn and NbTi-based superconductors |
Zirconium alloys are the main structural material for cores of water-cooled thermal reactors. They have such unique properties as low neutron capture ratio, good corrosion resistance and high ductility. In view of the concepts of safe development of the nuclear industry and an entry of the Russian zirconium products to the world market, the Chepetsky Mechanical Plant, Udmurtia, began a reconstruction of ingot and finished products making together with an updating of chemical-metallurgical operations. Here a chloride rectification Kroll process for producing spongy zirconium of lower (0.01%) hafnium concentration is being adjusted. It is required for the lowest possible proportion of higher neutron capture ratio materials in the reactor core. The introduction of the new technology will permit a much lower prime cost of zirconium.
Stainless steels continue to be applied as structural materials for water-coolant reactor core elements. They are acceptable for absorber element claddings where the neutron capture requirements are not limitative, and 10 to 15 years of service life are much longer than the potential of zirconium alloys.
Austenitic steels with higher general corrosive resistance are liable to intercrystalline fracture. That is why the material with a different plastic deforming behavior was needed. The research resulted in a Bochvalloy (named after Bochvar) high-strength chromium-nickel alloy resistant to irradiation and corrosion cracking. Not a single specimen of this alloy failed during more than 80 hours of comparative corrosion cracking tests. Bochvalloy has high strength properties close to perlitic steels, thus permitting it to be viewed as a promising alternate material for vessel structures.
A new multi-purpose dispersion-hardened Fe-Cr-Ni alloy with higher elasticity and strength, along with better relaxation, radiation and corrosion resistance has been developed for spring members of fuel elements and assemblies of WWER and RBMK (water-cooled graphite-moderated high-power channel type) reactors.
The ChS68 austenitic steel is applied in fuel element claddings of the BN-600 sodium-cooled reactor. An introduction of such as-20 % cold-deformed claddings promoted a stable reactor operation for eight years till a design burnup of 10 % of heavy atoms is reached. Many fuel elements showed a higher fuel burnup of up to 11.6 % of heavy atoms that corresponds to a damaging dose of 87 displacements per atom. All-Russian Research Institute of Inorganic Materials (VNIINM) faces the problem of a deeper fuel burnup to be achieved - up to 14 % of heavy atoms (the damaging radiation doses are 100 to 120 displacements per atom). In order to solve the problem, a new radiation-resistant complex-alloyed austenitic steel of EK164 grade has been developed. An existing process with a 20-% cold deformation operation is used to make claddings from this steel. This steel shows a very good stability of g-solid solution due to higher Nb and Mn content and an introduction of three carbide formers: Ti, Va and Nb. The steel is additionally alloyed with rare-earth metals.
The institute, and it means Russia at large, is the leader in the development of the 12 % Cr steel for covers of fuel assemblies of fast reactors. Ten years of trouble-free industrial service in the BN-600 reactor proved the radiation resistance of this steel. The post-irradiation examination gives a reason to believe that covers made from this steel will not be an obstacle to reaching deeper fuel burnup values.
Alexander Vatulin
General Director, All-Russian Research Institute of Inorganic Materials (VNIINM), since February, 2002, Dr. of Sc.(Eng.). Born on November 6, 1948 in Moscow. Nuclear engineer by education. Graduated from the Moscow Physical Engineering Institute (MPEI) in 1973. Passed all administrative levels at VNIINM, worked in the field of designing dispersed fuels. Since 1993, director of the fuel department and deputy chief process designer of transport reactor fuels and manager of developments on fuel rod elements of new generation for research reactors. In 1996 appointed chief process designer of commercial uranium-graphite reactor. Specialization: research in the field of developing nuclear fuel and fuel elements for transport, commercial, research reactors and low-power nuclear plants.
| |
| |
|
ly steels with an abrupt drop of induced activity can be applied in thermonuclear reactors. Along with it, all service properties of the material should be at the same level as those of activated steels, and even higher for some parameters. VNIINM has developed a heat-resistant steel, which, in properties, meets the requirements of a structural material for the first wall and blanket of the DEMO reactor.
Good neutron-physical properties of aluminum make it an attractive material for fuel elements of research reactors. Aluminum alloys must have high strength and erosion resistance. The institute specialists have already developed:
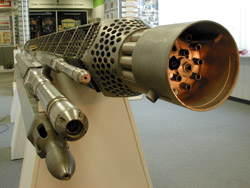 | Power reactor fuel assemblies |
a low-alloyed Al alloy with as small as possible cross section of thermal absorption. A small amount of titanium has been introduced into the alloy to ensure higher (up to 200oC) service temperature;
a heat-hardened complex 99 (AI-Ni-Fe-Cu-Mg-Cr) alloy.
Beryllium shows a unique combination of physical and mechanical properties. It is superior to all other materials in specific stiffness, strength or heat and comparable with the lightest magnesium alloys in density. VNIINM has at its disposal a smelting module comprising the process stages of Be powder production, compaction by cold isostatic and hot pressing as well as mechanical working and processing.
Structural Be grades have been developed for better quality of navigation systems. Gyroscopes made from them increased a system precision by order of magnitude, substantially shortened readiness time and extended warranty assurance.
Optical Be grades have been developed for higher regular reflectance of optical metal elements of laser systems with a 10.6 µ wavelength. In terms of strength properties, they correspond to the US S-65 and J-220-1 grades but have a better reflection power (over 98.4).
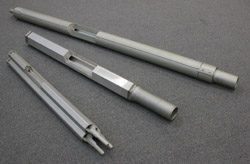 | Fuel assemblies of "MIR", IVV-2M and VVR-M research reactors |
Modern materials science of superconductors solves two main problems - developing promising materials with higher critical properties and reliable technologies of their production. VNIINM accumulated large experience on the development and research of composite low- and high-temperature superconductors.
Engineering composite superconductors based on a wrought Nb-Ti alloy ensure magnetic fields with an induction of up to 10 T at an operating temperature of 4.2 K, and the materials based on a Nb3Sn compound, magnetic fields of up to 20 T at the same operating temperature.
Niobium-titanium superconductors for accelerator equipment, magnetic ore separation, medical tomography, etc. have been elaborated and examined at VNIINM for 30 years. Their technologies permit a production of long round superconductors whose diameters are from 1.75 to 0.1 mm with superconducting fibers from several tens of micrometers to micrometer fractions in diameter and a critical current density of up to 3000 A/mm2 in a 5-T field as well as rectangular conductors with a section area of 7 to 28 mm2 and a current-carrying power of 580 to 18,000 A.
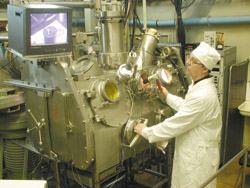 | CA-424 facility for electron beam welding |
An important field of applying Nb3Sn superconductors is the development of high-field solenoids for various physical laboratories. With this view in mind, stabilized superconductors have been developed. Their different structures have from several tens to hundreds of thousands of fibers affording high current-carrying power in a wide range of magnetic fields up to 20 T.
The leading Russias position in the development of low-temperature superconductor technologies was confirmed by the participation in a project for setting up a research thermonuclear reactor with a superconducting magnetic system. Within the framework of this project, VNIINM develops and produces Nb3Sn and NbTi-based superconductors fully meeting the world standards.
High-temperature superconductors are believed to be the main material for a new generation of electrical and electric-power equipment. Of the greatest interest for commercial application among high-temperature superconductor compounds are Bi-Pb-Sr-Ca-Cu-O and Y-Ba-Cu-O ones. The original institutes research resulted in elaborating basic concepts of producing solid and multistranded conductors in up to 250-m single lengths based on superconducting compounds of the Bi system (Bi-2212 and Bi-2223).
One of major activity lines is the development and adjustment of commercial technologies of producing refractory metals - vanadium, niobium, tantalum and alloys on their base - for thermonuclear power engineering, superconducting devices and electronic industry. The Russian part of the research thermonuclear reactor project includes studies of a low-activity Va-Ti-Cr alloy of higher purity. Uralredmet JSC, Sverdlovsk Region, has put on stream the production operations for vanadium metal. A flowsheet for processing high-purity Va alloy ingots was elaborated, and first plate semi-products were obtained, thus making it possible to carry out comprehensive tests prior to and post irradiation in the BN-600 reactor.
In nuclear power engineering niobium is used for alloying zirconium alloys and making superconducting products. At present there exist technologies for making ultra pure niobium of RRR > 300 grade, which is used in superconducting high-frequency resonators, for which purpose the institute smelted more than 5 tons of ingots.
Tantalum is applied as sheet, foil, rods and wire for making products with a unique combination of properties in chemical stability and heat resistance as well as for manufacturing superconductor components, production of heat-resistant alloys and as powders for electrolytic capacitors.
A.A.Bochvar All-Russian Research Institute of Inorganic Materials (VNIINM) Federal State Unitary Enterprise is the leading institution in materials science and technologies of the nuclear fuel cycle in the framework of the Russian Ministry of Atomic Energy.
The institute was founded in 1945 to solve materials science and technology related problems of nuclear weapon development. For more than 30 years the institute was headed by Academician A.A.Bochvar who founded a national materials science and nuclear technology school.
According to the governmental resolution, the institute was given the standing of a state scientific center of the Russian Federation.
The institute is a multi-purpose organization. Its terms of reference are the development of nuclear fuel cycle technologies; fissile, radioactive, structural, superconducting materials, refractory, rare-earth and other metals and alloys on their base; technologies of making various parts based on innovative materials; radiochemical production and radioactive waste processing technologies.
The institute has at its disposal a unique research and technological base, which allows the whole complex of R&D to be carried out, from research to output of prototypes and pilot lots of products.
| |
| |
|
In the last decade an interest in nanomaterials (named superdispersed materials in Russia) grew considerably worldwide. It is related to new properties of them, which appeared with a decrease of crystallite size. Owing to the emergence of these materials, nanotechnologies began to progress. By virtue of a large surface area of crystallites, nanomaterials show high reactivity, wettability and sorption power, better sintering ability, etc. which makes it possible to obtain new metal matrix composite materials, intermetallic compounds with higher strength, plasticity and wear resistance.
Now VNIINM has processes for producing highly porous and high-strength nanoberyllium and nanoaluminum. A technology for making porous beryllium from conventional beryllium powders with a nanoberyllium binder, intended for thermonuclear reactor blankets, is under development. It affords high precision parts to be made at 250oC (instead of 1000oC). With the help of nanoaluminum, unique parts with 100-% open porosity and high strength are obtained.
Tantalum powders of nanocrystalline structure gave an impetus to producing high-capacitance capacitor powders with a charge of 20,000 to 100,000 µC/g. Nanomaterials will help to solve a number of difficult problems concerning reactor fuel, high-temperature superconductors and high-strength structural materials.
|