Yury Adno
A 350-mm mill, a high-capacity rolling unit, has been put in operation at the Oskol Electric Steel Works (OESW). This investment project has been implemented within the Federal program to re-equip and develop the Russian steel industry and it is the largest industrial project built in post-Soviet Russia. By commissioning the 350-mm mill OESW JSC becomes Russias largest producer of constructional bars.
The Oskol Electric Steel Works is the first and still the only one plant in Russia, which realized technological principles of the blastfurnace-free metallurgy on a commercial scale. It is the largest production complex of this kind in Europe.
The major advantage of the works is its alternative concept of steelmaking based on the Midrex direct reduction process. In combination with the progressive complex technology of electric arc furnace process it permits to make steel of high quality, exceptionally clean in detrimental impurities and residual elements. Not only does Oskols steel correspond to world standards, by many characteristics it exceeds them.
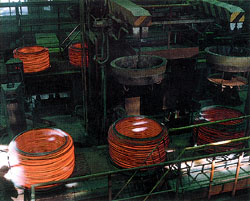 | New product of 350-mm mill |
The progressive technology is not the only one competitive edge that OIEM has. A number of other factors should be mentioned as well. The works is securely provided with iron-ore materials supplied by the nearby Lebedinsky Mine & Concentrator as well as with comparatively cheap natural gas for its energy needs. The advantageous geographic location in the center of Russias European part makes it possible to significantly reduce costs of transporting products to large consumers both inside and outside the country. Finally, it is already possible today to fully evaluate the pragmatism and operational precision of OESWs top managers, who retained control over the assets during the privatization period. The civilized policy towards corporate property served as a basis of a normal business development and ensured trust of financial partners.
Stressing these factors OESWs general director Lev Kvetnoy believes that exactly all this helped the works enter the new economic environment with a relative ease. The Oskol Electric Steel Works turned out to be the only steel plant that was steadily increasing production volumes in Russias crisis years of the 1990s. In 1991 through 2001 the steel production volume increased 1.5 times exceeding the design output of the steel melting process stage.
In this connection OESWs executive director Andrei Ugarov stresses the particularly important role of export orders, which, though, did not come all by themselves. There was a need to significantly revise the marketing policy. "We were forced to considerably change the range of products because, due to well-known reasons, there was a sharp decline of demand for our traditional steel products: tubular billets, bearing steel, rolled products for machine-building plants. Square billets produced at the 700-mm mill accounted for most of our export shipments", Andrei Ugarov says.
There are three process stages at OESW JSC:
production of oxidized and metallized pellets;
steel melting in electric arc furnaces with ladle treatment and continuous casting;
production of bars.
Until recently the works could not fully exploit advantages of its unique technological scheme because the production cycle was not complete. Products of the 700-mm mill varied in size from 80 mm to 180 mm and that affected very much OESWs ability to maneuver on the market.
And now the 350-mm mill, the most important production unit, has been commissioned. The range of the mills products is cut-to-length round, square and hexagon bars with diameters of 12 mm to 70 mm as well as coiled bars with similar types and diameters of 12 mm to 35 mm. The annual design capacity of the mill amounts to 1 million tons (700,000 tons of cut-to-length bars and about 300,000 tons of coiled bars).
The mill, which has light- and medium-section lines, has such technical advantages as the moderm roll arrangement in mill stands. It permits to perform twist-free single-strand continuous rolling at each line with the speed of 18 to 20 meters per second. The automatic control of the minimal tension and interstand looping as well as the optimal reduction schedule provides stable geometry along the full material length. Such design peculiarities of the mill as the higher stand rigidity (permitting material deformation at minimal temperatures of about 950 degrees centigrade) and the sizing block after the light-section line ensure the high geometrical accuracy of rolled products (within 0.1 mm). So as to get required material physicomechanical characteristics there is a complex of units for thermal treatment both in and off the mill line in furnaces with protective atmosphere. The final finishing and nondestructive testing of products are carried out with centerless lathes and ultrasonic flaw detectors in the finishing line.
With commissioning of the 350-mm mill the total capacity of the rolling process stage increases up to 2.5 million tons a year. But at the same time there is a problem of matching the main process stages. So, it seems that there will be a need to adjust the range of products at continuous casting machines through making billets of smaller section for the 350-mm mill. In order to provide the full utilization of the 700- and 350-mm mills the production capacity of the steel-making shop should be raised from 2 million tons to 2.55 million tons. In the future this will make it necessary to expand and reconstruct steel-making facilities, which will bring the already advanced works to a new qualitative and technological level with no equals in the world.
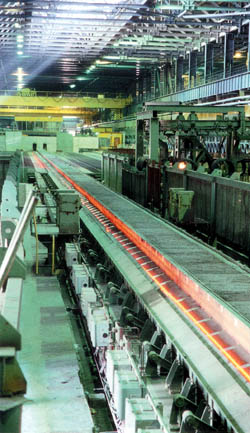 | 350-mm mill of OESW JSC has two light- and medium-section lines. |
As Lev Kvetnoy said, "the mills commissioning should give a new impetus to the development of the Oskol Works. Its leaders are convinced that, as a result, OESW will move to a new market category. There will be a significant extension of the range of products and we will get additional opportunities for maneuvering". Now the works can offer customers the whole number of new products. Among them are hexs, flats, steel reinforcement, turned and ground rolled products, including those made of spring, carbon and alloy steels as well as steel for cold heading.
It is obvious that the competition on Russias bar market will grow significantly taking into account that similar products are being made by MMK and Mechel (the Chelyabink region), the Krasny Oktyabr Plant in the city of Volgograd, Petrostal (St. Petersburg), Moscows Serp i Molot Plant, Sibelektrostal (Krasnoyarsk). The West Siberian Iron & Steel Works, the largest bar producer incorporated in EvrazHolding, has started modernizing its facilities. Besides, Severstal JSC intends to set up facilities to make this type of products.
Nevertheless, the management of the Oskol Electric Steel Works is confident of the its strong positions on the market. Quality characteristics of OESWs products permit to market them even at above-the average prices. Additional costs to consumers will be fully compensated thanks to minimal rejection and improvement of performance of items made of this steel. For example, tests for fatigue strength of springs made at the Volzhsky Automobile Plant (the maker of Lada, Samara and Niva cars) proved that by their consumer qualities and technological characteristics rolled products of OESWs 350-mm mill considerably exceeded those of competing products. Many engineering plants prefer to use OESWs products when fulfilling the most important export orders.
Shareholders and managers of OESW JSC determine their long-term market strategy taking into account, above all, needs of the national economy. The revival of demand in most steel-consuming industries contributes to the growth of bar sales. However, the Russian market capacity is still not high. To a larger degree financial prosperity of the works depends on export, which accounts for about 60 % of OESWs shipments. The commercial services of the works make sure that they are offering high-quality rolled products with high added value including those made by the 350-mm mill.
In 20 years of its operation the Oskol Electric Steel Works produced over 25 million tons of crude steel and 20 million tons of high-quality rolled products.
The total cost of constructing the 350-mm mill amounted to over $656M, of which $292M were the works own funds and the rest were credits from the consortium of German banks and Russias Sberbank. Terms of credit repayment depend on how fast the new mill will reach the design capacity.
The mills commissioning is the beginning of efforts to master all connected units of the production line. A significant adjustment of the program to modernize other shops at OESW can be expected in the nearest future.
|