Yury Adno
The Chelyabinsk Zinc Plant is commissioning an automated electrolysis complex. This event completes a long period of reconstruction, which took 15 years and called for significant investments - around $180 million. Presently one out of two banks of electrolytic tanks is in operation, together with an anode department and a solution treatment section, and full-scale tests of smelting furnaces are carried out. The new process and equipment are in line with the world achievements in hydraulic metallurgy of zinc.
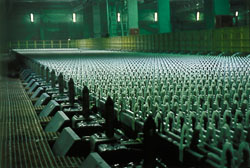 | New section of zinc electrolysis. |
The commissioning of the new complex is of special value to the Russian market. The fact is that after the collapse of the USSR, a larger part of the zinc industry turned out to be in the territory of the new independent states - Kazakhstan, Uzbekistan, Ukraine. It failed to affect the market solely due to a concurrent dramatic decline of the home demand. While in 1991 Russia consumed more than 500,000 tons of zinc metal, in 2001 just about 110,000 tons were sold. A revival of the Russian industry, including zinc-consuming sectors - steel industry, non-ferrous metals processors, automakers, paint and tire producers, changes the pattern. In the experts opinion, the demand for zinc will surpass the production tonnage in the country already in 2002.
Three zinc plants operate in Russia. Here the Belovsky Plant in the Kemerovo Region (approximately 2,900 tons in 2001) in its production potential cannot have a profound effect on the market. A much bigger Elektrotsink plant in the town of Vladikavkaz (North Osetia, about 90,000 tons) carries out tolling operations, for the most part, and is not able to make large metal supplies to the home market.
Under these circumstances, according to its general director Vsevolod Geikhman, the Chelyabinsk Zinc Plant becomes a monopolist in its way. However, the plant is not going to dictate the conditions. "We do not interfere with anybody in the market", stresses Geikhman. The price level is directly connected with LME quotations, and the consumer can select any supplier.
The share of the Chelyabinsk Plant in the world zinc production is about two percent. But export expansion is not the main market strategy of the plant. In its portfolio, the obligations under foreign contracts account for more than 20 to 25 percent. "With due regard to the specific position in the Russian market", Vsevolod Geikhman says, "our priority is the preferential provision of home consumers. We export only that quantity of our products (zinc, cadmium, indium) whose sales in Russia is hampered because of a limited effective demand". Alongside it, positions in the foreign markets are of interest for future prospects as well. The plant management believes them to be a bridgehead for the forthcoming promotion of the premium products - zinc metal of Special High Grade (SHG).
The Chelyabinsk Zinc Plant passed the privatization safely, now having no problems in regard of corporate property. In 1996 Euromin, a big diversified company and a division of Vitol (a transnational petroleum corporation), became its owner. Euromin representatives in the management of Chelyabinsk Zinc Plant JSC deliberately restructured the operations according to the rules and standards approved in Western companies. With their assistance, an up-to-date management system was successfully introduced and skilled managers were trained. In turn, the plants specialists helped their Euromin colleagues to better understand the production peculiarities, with focus on economic prospects and high investment attraction.
In the opinion of Berislav Galovich, Commercial Director, "our plant has got in Euromin civilized and skilled partners respecting Russian laws. And the main thing is that the company pursues a promising strategy while connecting its long-term interests to the Russian economy".
Euromin acts as a trader of the plant, thus sparing the necessity to resort to the services of other mediators and use less effective patterns with an involvement of outside current capital. The quality of commercial-and-sales activities is testified by the following figures: the share of zinc supplied to the Russian market grew from 15 % in 1997 to 80 % in 1999, and by that time the overall zinc production figure reached a record value for the whole history of the plant - 138,000 tons, above the approved design capacity (130,000 tons).
With the appearance of Euromin, the plant could go on with the reconstruction of the main production operations.
The modernization of the plant is a long story. As early as the middle of the 1980s, the variant of a highly-automated production based on a Snamprogetti (Italy) project was chosen. Its core was an automated zinc electrolysis complex with
3.4 m2 area super cathodes (1.2 m2 now), with greatly improved synchronized conversion stages and infrastructure in order to reach an ultimate annual production capacity of 200,000 tons of zinc with much better quality. Here the basic hydrometallurgical method of production with a high rate of zinc recovery from concentrate (97 % minimum) is preserved. The main product specialization is also retained. Alongside zinc metal, the plant is to make cadmium and indium metals as well as sulfuric acid, copper slag - a raw material for copper smelteries, lead cake - a raw material for lead and precious metals producers, as well as commercial zinc vitriol.
Vsevolod Geikhman
General Director of the Chelyabinsk Zinc Plant, 56 years old. Engineer in chemical processing by education. Graduated from the Lenindrad (St.Petersburg) Technological Institute. For 30 years he has been working at the plant where he passed all career steps. Elected General Director in 1996. Engaged in research. In 2000, he received a patent for the unique technology of complex processing of lead middlings accumulated at industrial dumps for many years.
Vsevolod Geikhman enjoys team sports, in particular, voleyball in which he became a national veterans champion.
| |
| |
|
In the 1990s, lack of investments caused a break in the implementation of the project. The work was resumed in 1997 with the direct participation of Euromin. By now, due to this company, adequate funds have been accumulated. Of great help is also the support of the European Bank for Reconstruction and Development (EBRD): its share is about 25 %.
The raw materials base of the Chelyabinsk Zinc Plant is rich deposits of sulfide copper-zinc ores in South Ural which are processed at the Uchailinsky, Gaysky and Bashkirsky Mine & Concentrators and whose total resources are estimated at about 30 million tons.
The start-up of the new electrolysis complex will afford much lower production costs. Thus, power consumption will decrease by 50 kWh/ton of zinc, with annual savings reaching about 7.5 million kWh. Consumption of industrial water will be reduced by 600-700,000 m3. Savings of lead, aluminum and silver will increase owing to longer anode life. Rate of zinc dust applied in solution treatment will go down by 2030 %. Here saleable fine zinc powder can be produced. Automatic facilities will drastically improve labor conditions. Heavy manual operations will be fully eliminated. When the complex reaches its design capacity, labor productivity is estimated to raise 1.6 times. The product quality will be greatly improved. The Chelyabinsk Zinc Plant will be capable to produce SHG zinc of 99.995 % purity (for the time being, HG zinc of 99.975 to 99.98 % purity is made). The product of similar purity can be certified and registered at LME. It will help the plant to raise profitability of exports and improve flexibility of the market activities. Moreover, when the smelting department is put on stream, the plant will be in a position to produce Zn-Al-Cu alloys, the demand for which is evaluated at 10 to 15,000 tons a year.
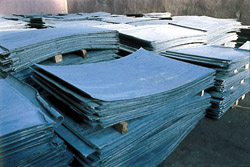 | New product: Special High Grade zinc. |
Leonid Kazanbaev, Engineering Director of the Chelyabinsk Zinc Plant, is sure that by the start of 2003, the complex will be fully commissioned. "We are aware", he continues, "that it is only the beginning of enormous work at the mastering and matching of the new equipment with the existing facilities and the promotion of the new products in the market".
By now the next stages of the production modernization program have been calculated with design assignments made out. The key objectives are elimination of bottlenecks of the zinc oxide flowsheet, further increase of plant capacity, expansion of raw materials base, observance of stringent ecological standards.
It is estimated that, when the modernization is completed, the Chelyabinsk Zinc Plant will correspond to the best world zinc producers in equipment. It will ensure the lowest production costs and high product quality.
|