Pyotr Yugov Dr. of Sc. (Eng.), Professor
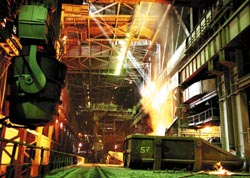 | Magnitogorsk Iron & Steel Works. Basic oxygen shop (BOS). BOF-2 in operation |
|
he basic oxygen steelmaking route has gained wide application due to high production rate, technological flexibility, simple design, low costs, good conjugation with blastfurnace ironmaking and continuous casting. Despite the dynamic development of electric steelmaking, the BOF steel ratio is 60 % in the word steel production. For the last decade, Russias steel production by this route has been continuously increasing: from 46.6 % in 1990 to 74.7 % in 2001.
State-of-the art steelmaking practice has as its disposal a variety of BOF processes ensuring melting of charge various in composition, including manganese, phosphorous, chromium-nickel, vanadium and other hot metal grades, with scrap additions. A basic oxygen furnace permits melting in the required conditions so that many different steel grades are produced..
Amongst the basic trends of BOF process development, higher steel cleanness must be first of all emphasized, that is, lower concentration of carbon and deleterious impurities like sulfur and phosphorus. Today the requirement for this route is an output of steel with a preset chemical composition.
The Russian BOF shops are fairly well equipped. The best of them comply with world standards in equipment. The Magnitogorsk Iron & Steel Works (MMK), Severstal, the Lipetsk Iron & Steel Works (NLMK), West Siberian Steel Corporation (ZSMK) have big steelmaking complexes equipped with 350 to 400-ton BOFs, continuous casting machines, hot metal desulfurizing and steel treatment plants, and fitted with automatic process control systems. In BOF shops, plants for complex ladle treatment, including units for circulation or batch-type vacuum degassing with preliminary refining, are especially effective for melting of constructional and tool steel grades.
At Russian works, BOF process has its peculiarities attributed to initial charge composition, steel grade mix or industrial traditions.
At MMK the key objective of steelmaking operations is governed by an extended range of steel grades with low sulfur content. This element enters the BOF heat from the charging ladle together with hot metal, scrap, slag, in complex with carbon-containing and slag-forming materials. Thirty to fifty-five percent of sulfur comes together with hot metal, and from 45 to 70 % with other components. In the BOF heat 30 to 35 % of this impurity can be removed. The steelmaking process factors have a rather limited influence on S concentration in the heat before tapping. For example, if the slag portion is 10 ton higher, S concentration is only 0.002 % lower. That is why the low-sulfur steel grades can be made in the BOF shop of MMK only if desulfurized hot metal and clean home scrap are used. But even in this case, it does not always happen that low sulfur content is hit before steel tapping. Here ladle desulfurizing is required.
Severstal applies a special charge based on hot metal with iron-ore additions. It reduces the steelmaking cycle and lowers Cr, Ni and Cu concentration in the final steel composition by 0.030.05 %, due to it an output of automotive steel of higher categories grows and shortage of clean scrap is set off. Hot metal desulfurizing is advised in the case of up to 0.01 % S in the final steel composition and required in the case of up to 0.005 % S.
At ZSMK the main problem of BOF operations is connected with the melting of low-silicon (below 0.4 %) hot metal with higher P content (up to 0.3 %). In mass production, the in-plant BOF practice permits lower lime consumption, higher steel output and formation of slag with required properties during blowing, for making steel of desired quality.
It is no doubt that in principle modern BOF route can process hot metal of any chemical composition. However, in the mass large-tonnage production, the requirement of stable technical and economic indicators claims that in the entry hot metal S concentration is below 0.03 %. It is a precondition of higher Si content (0.70.9 %) for desulfurizing. Here for better slag-making (as known, slag is the main factor of any steelmaking process), Mn concentration must be at least 0.81.0 %.
The study of desulfurizing processes shows that energy-wise the reaction of sulfur removal is much easier provided for in hot metal than in steel. None the less, in the blastfurnace process it is more difficult because owing to complex redox reactions, energetics of thermodynamic conditions of intensive desulfurizing predetermines higher Si content resulting in larger lime and coke rate with lower steel output. Therefore the low-sulfur hot metal BF melting calls for a well-proven technology, charge components with minimum S content and high-basicity slag mixes. In BF ironmaking a decrease in S content leads to lower furnace production capacity, higher coke rate and larger operating costs.
In the BOF process intensive desulfurizing is inefficient as well since the metal-slag system does not reach an equilibrium. The low coefficient of sulfur distribution between the slag and the metal makes removal more difficult and involves higher costs.
In so doing, thermodynamic conditions of effective desulfurizing are not provided for in either BF or BOF process. Hence, from this viewpoint both processes are technologically ineffective and economically unprofitable. That is why it is expedient to take the operation of sulfur removal out of the furnaces and practise desulfurizing of hot metal and steel in the ladle. It permits a simpler and less expensive start-to-finish flowsheet of sintering, blastfurnace and converter operations.
|
Pyotr I. Yugov Head, BOF Laboratory, I.P. Bardin Central Research Institute of Iron & Steel Industry (TsNIIchermet) State Scientific Center of the Russian Federation (RF)
Dr. of Sc. (Eng.), Professor. Author of more than 300 research works and 100 inventions.
Directly participated and supervised development of theoretical and technological concepts of high quality clean steel production, including high strength and cold-resistant steels for arctic service, high quality bearing steels, automotive sheet, kinescope strip, super thin tinplate, wire cord steel, rails, constructional steels. Developed and put into practice technologies of BOF steelmaking from hot metal of naturally-alloyed compositions: vanadium-containing (Nizhny Tagil Iron & Steel Works - Russia), phosphorite (Ispat Karmet Kazakhstan, ARBED Luxembourg), manganese (Kremikovcy Bulgaria), low-manganese (Severstal, Magnitogorsk Iron & Steel Works, West Siberian Steel Corporation Russia), high-silicon (Bokaro, Visakhapatnam - India); processes of solid-charge BOF steelmaking (without hot metal) that gained world-wide priority (Acominas Brazil, Sicartsa Mexico); start-to-finish energy- and resource-saving technologies for steel industry.
Academician of Russian Academy of Natural Sciences, full member of New York Academy of Sciences. RF State Prize laureate, two USSR Council of Ministers Prizes laureate, I.P. Bardin Prize laureate.
|
|
| |
|
With a shortage of manganese raw materials, the procedure of Mn application in the BOF process becomes especially important. It dictates the conditions of early formation of slag and control of oxidation of the metal before tapping. For a long time, it predetermined the requirement of 0.8 to 1.0 % Mn in the hot metal, and consequently an additional input of manganese-bearing materials into the BF sinter burden which raised melting costs. But low initial Si concentration in the hot metal permits low-manganese hot metal to be made with downstream remelting in the BOF using Mn ore as a deoxidizer. The practice showed that it gives an opportunity to improve parameters of BF ironmaking (to reduce coke rate by 3 to 5 % and increase BF production capacity by 3 to 4 %) as well as BOF operations (to reduce the rate of Mn-bearing ferroalloys by 1 to 1.5 kg/ton and increase steel yield by 0.5 to 1.0 %).
Thus, the techno-economic and thermodynamic analysis of metal refining at all stages of steel production operations, including sintering, ironmaking and BOF steelmaking with ladle treatment, makes it possible to define the main parameters of start-to-finish energy- and resource-saving process of sintering, blastfurnace and BOF operations. It is viewed as a single complex of producing clean steels with a super low content of deleterious impurities, above all, S (0.001 %).
By the way, in the opinion of Japanese experts, nowadays, as compared with the classic BOF process of the 1950s and 1960s, the ratio of BOF proper in the distribution of refining functions is maximum 20 %, i.e., refining is, for the most part, performed outside the furnace.
The basic concepts of the start-to-finish process offered by TsNIIchermet (Moscow) are the differentiation of main melting and refining functions of the steel production cycle and the application of specialized units for their putting-into-practice. This process includes:
BF melting of low-manganese and low-silicon hot metal (below 0.3 % of each element) with unspecified sulfur concentration (0.3 % and more) from Mn-free burden;
hot metal desulfurizing (below 0.005 % S) in the charging ladle;
highly-effective and cost-efficient BOF conversion of clean hot metal using a low-slag process and a multi-fold application of final slag in the BOF melting proper as well as intensive dephosphorization of low-silicon and low-manganese metal with high-basicity oxidized slag in the converter vessel and melting of clean standard semi-product;
output, with the help of ladle-furnace treatment operations, of high-quality clean steel of any complex composition and rational tonnage;
The above complex process makes it possible in sintering & blastfurnace ironmaking operations:
to process lean ores without Mn-bearing raw materials applied, to expand the range of coking coals due to the involvement of grades with higher S content;
to reduce coke rate by 1 to 3 % and increase BF production rate by 3 to 5 %.
In the basic oxygen steelmaking operations this process permits:
lower (by 20 to 30 kg/ton) lime rate, reduced (by 25 to 30 %) slag rate as well as Fe losses due to slag, higher (by 1 to 1.5 %) yield and vessel production rate;
stable high quality of crude steel.
The most critical link in the full-scale implementation of this process complex is hot metal desulfurizing in the ladle. TsNIIchermet has elaborated the basic fundamentals of intensive desulfurizing of hot metal and desulfurizing reagents. A specialized joint venture (with the participation of the Solikamsk Magnesium Plant) for magnesium desulfurizers to be produced as applied to individual requirements of Russian steel works has been set up. The final stage of this process is a continuous casting machine where the metal in the tundish is heated by d.c. discharge which increases the technological flexibility of the flowsheet as a whole and makes it possible to substantially improve steel quality.
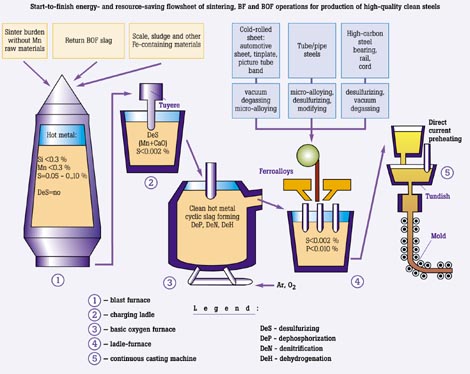 The constant growth of steel stock worldwide and the increase of scrap circulation make the problem of reprocessing of secondary metals in steelmaking operations very urgent. Its solution is connected with the energy advantages of plasma and d.c. arc discharge EAF processes to be used in BOF operations. One of the most rational directions of steelmaking development is a set-up of production complexes combining the advantages of both processes (BOF and d.c.-based EAF).
The theoretical analysis and experimental studies show that under certain conditions the "d.c. EAF-BOF" steelmaking module can be effectively applied at integrated works and mini-mills without coke- and ironmaking operations. The specific merit of this pattern is that a high-quality steel, in particular, with an ultra low nitrogen content, can be produced, thus greatly improving its ductility and workability.
Most probably, the basic oxygen furnace will not lose its value in the foreseeable future. Though this route has undergone great changes during a century and a half of its existence, it still retains a substantial reserve for technological and design improvement.
|