|
Magazine |
|
About |
|
SUMMIT |
|
Contacts |
|
Home |
|
|
|
|
| |
|
|
 |
#3' 2003 |
print version |
|
THE LAST PIECE OF SOVIET PIE CONSIDERS PRIVATIZATION |
|
Yevgeny Khokhlov
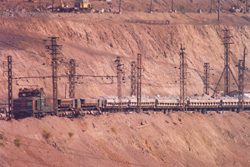 The Kalmakir copper field. The railroad, which makes ore transportation significantly cheaper, has become today an obstacle to developing the open pit |
|
The Almalyk Mining-and-Metallurgical Complex (AMMC) remains the last large producer of base metals on the territory of CIS countries, which still has not been taken over by private capital. But this ‘exclusive status of the enterprise may change soon. Uzbekistans Committee on State Property Management offered to sell a large block of AMMC shares (46.5 %) and, possibly, it will also transfer yet another state-owned 51% stake to a strategic investor for a trust management.
he mining-and-metallurgical complex, which is located in the city of Almalyk in Uzbekistans East, has 3 mines, 2 concentrating mills, 2 metallurgical plants as well as the production infrastructure and auxiliary sub-units. It produces copper, zinc, a number of rare metals, gold and silver. In 1997 AMMC was transformed into a joint stock company but today only 2.5 % of its shares belong to private persons, who are the enterprises workers themselves. The rest is owned by the State.
The Committee on State Property Management does not intend to quote shares of AMMC on the stock exchange. Instead, it would like to sell the entire stake to one owner. That is either to some company or consortium, which might be set up specifically for this purpose. The price of a 46.5 % stake reserved for selling to foreign investors is estimated at $450M to $460M. A buyer may be given an opportunity to pay out this amount in 2 to 3 years. The State will get the half of proceeds as the property owner. The second half of them will return to the complex to be reinvested in its modernization.
|
Along with producing copper and zinc, gold and silver AMMC deals with rare metals, which include molybdenum, cadmium, selenium, tellurium that traditionally are accompanying the copper-and-zinc production. Recently, there was a new development in the molybdenum production: a joint venture with Israels company Metal-Tech was set up specifically for this purpose. AMMC has been experimenting with re-processing of waste gases. There was a pilot batch of osmium-187 produced There has been an increase in extracting rhenium and there are plans to raise its production volume up to 200 kilos a year.
|
| |
|
AMMC general director Gennady Prokhorenko has problems over ways to raise the enterprises investment attractiveness. It should be admitted that this task is not that easy. For decades, as the complex was managed by the USSR Ministry of non-ferrous metallurgy, funds for its reconstruction and development were not allocated at all. Consequences of the past policy are fully felt today. The equipment is much worn out, buildings are dilapidated and a considerable part of production capacities are idle.
Despite all of these, Prokhorenko is confident that the complex will start developing and that this forward movement will finally attract a foreign investor. "In the last two years we achieved some things. The production of copper cathodes, our main products, increased 20 % and we keep raising volumes of their production", he said. In the directors words, almost all profit goes to "renewing and purchasing new equipment". Last year the largest deal was buying 12 Terex-made dump trucks.
One of the ways to make yourself known is to prove to financial markets your competence as a partner. AMMC general director is pleased to report that they are now working on a credit agreement that would provide $ 30 M. "These credits will be provided without any government guarantees, just against our export contracts", stressed Gennady Prokhorenko. Now foreign banks will get an opportunity to be certain of AMMC ability to service its debts.
As before, the chief source of funds are proceeds from selling its own products, mainly, copper, 70% of which are exported. The enterprises leaders want to raise the annual production of copper up to 90,000 tons in the coming years (in 2002 the complex produced 80,000 tons). It is quite feasible for the Almalyk Complex. As Prokhorenko said, "the capacities that we have at the concentrating and metallurgical process stages permit us to produce much more". However, the production growth is slowed down by the lagging mining sector.
Their major headache is Kalmakir. This vast open pit (for its size it is considered the largest in CIS non-ferrous metallurgy) produces copper-porphyry ores. Having low content they are, however, easily concentrated. Usually between 75% and 80% of copper are extracted there, while the technologies of its further processing do not require special expenses and permit to obtain a final product of high purity. Reserves of raw materials are sufficient for securing AMMC operations for many decades to come.
The scheme of the mining process arrangement looks very suitable: there are railroad lines laid right in the pit, which connect it with the nearby concentrating mill. However, precisely these lines have now become a insurmountable obstacle. "They are tying our hands up, not letting us develop", said Gennady Prokhorenko describing the essence of the problem.
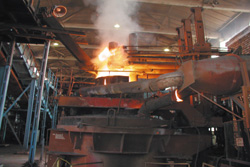 AMMC copper-smelting mill: the smelting process stage |
|
There is a program to further develop this open pit. Explaining this program AMMC chief engineer Kuvandyk Sanakulov said that the old scheme of ore excavation would still remain at the first stage but there were plans to renew the pits equipment and transportation means. Excavators, dump trucks, locomotives and box cars will be replaced with the more powerful, load-lifting and efficient ones. In the words of Sanakulov, "the first step" toward implementing the new program was the acquisition of Terex-made tucks at the end of last year.
After that the reconstruction of the open pit will start by switching over to the so-called cyclic assembly-line technology. It is noteworthy that this method is well known to AMMC chief Gennady Prokhorenko. Not so long ago he headed the gold-extraction complex Muruntau, where a similar scheme is used: the rock mass is brought to a certain level, where it is preliminarily crushed and, then, transported to the surface by a conveyer.
At present, the annual volume of ore produced at Kalmakir amounts to 27 million tons. "In the future we will raise the production capacity of the open pit up to 42 million tons", said Sanakulov. Accordingly, there will be a need to reconstruct the concentrating mill by installing crushing mills and floatation machines with higher unit power. On the whole, in the words of Sanakulov, the annual productivity of the ore-reprocessing mill should be increased from todays 29 million tons to 40 million tons. "This way we will be able to start getting about 120,000 tons of copper concentrate and fully load the existing capacities of the copper-smelting plant. We will use 115,000 tons of copper for producing cathodes", continued the chief engineer.
The complete program of reconstruction and engineering re-equipment of the Almalyk Mining-and- Metallurgical Complex is to last till 2010. By that time all planned indicators should be reached. Sanakulov thinks that the program is quite rational: production volumes will be constantly on the rise and investments are planned in such a way "as to avoid freezing them at any stage and to get quick payoffs from invested funds". Is this possible in the mining production, which is traditionally noted for an especially long investment cycle? Yes, says the chief engineer of the complex affirming that capacities of the concentrating cycle exceed the productivity of the open pit by 2 million tons of ore a year. Precisely this factor determined the amount of investments of the first stage. Almost all available funds are directed to the engineering re-equipment of the pit and that will help increase volumes.
|
Gennady Prokhorenko
The general director of the Almalyk Mining-and-Metallurgical Complex (AMMC) was born on June 26, 1949, in Ukraine but his life was mainly connected with Uzbekistan, where he graduated in engineering, from the Tashkent Polytechnic Institute. From 1968 to 2001 worked at the Muruntau field, where the largest gold-mining complex has been in operation, and, later became its director. From 2001 has been with AMMC.
He keeps constantly engaged in applied studies and regards science as the chief potential for production development. At present, has been introducing the new cold-zincing technology and working on using the cyclic assembly-line production technology at the Kalmakir open pit that fundamentally differs from the Muruntau pit.
He is furthermore interested in nontraditional directions in science, and has, for instance, increased the yield capacity of wheat seeds.
Gennady Prokhorenko has two sons who work at Muruntau, three daughters and two grandchildren. They have all encouraged him to take up digital photography as a hobby.
|
|
| |
|
AMMC management does not regard reconstruction of the copper-smelting plant as a pressing matter. The metallurgical cycle was originally arranged quite successfully. For example, there are no blister copper ingots around: the transfer from one technological process stage to another is done without this intermediate product. And although the basic installations are outdated, their operation is still quite reliable. In the opinion of AMMC chief engineer, the major problem is ecological. "We still have reverberatory furnaces in operation, which produce enormous emissions of noxious gases", says Sanakulov. "We will replace the half of installations at the copper-smelting plant and, besides, the sulfuric acid production facilities are to be reconstructed. The implementation of this program will allow to reduce emissions by 12 times".
Attempts to find ways of reprocessing man-caused waste, such as rejects of concentrating mills and copper-smelting production slag, can be considered a double-purpose production and ecological task. Specialists from AMMC are trying to accomplish this task mostly on their own. As Sanakulov stresses, the enterprise has its own research base that includes not only laboratories but testing production installations as well. One of the promising directions in this respect may turn out to be the biochemical method, which will permit to reach a higher degree of extracting copper than through the classical schemes of waste reprocessing.
The plans for producing zinc, the second most important direction of AMMC activity, are not so definite. In this case lagging in preparation of its raw material base happened to be much more considerable and so far there is no possibility to overcome it.
AMMC zinc-producing plant operates on tolling terms offering its services for minimal prices. Loaned raw materials are supplied from Kazakhstan but shipments are being reduced. "Our potential zinc capacities amount to125,000 tons. Last year we produced 80,000 tons but this year we have contracts just for 60,000 tons", admits Gennady Prokhorenko. He connects problems of getting zinc concentrate with the fact that the corporation Kazakhmys is building a high-capacity zinc-producing plant in Kazakhstan and is holding back raw materials because it is going to start testing the plant in about six months time.
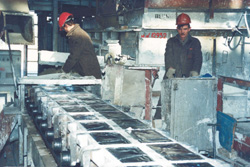 Today AMMC zinc mill has a considerable reserve of capacities |
|
But is it quite possible that the future of AMMC zinc production will be determined before Kazakhmys plant operates at full capacity. As Prokhorenko said, intensive works are now underway in Uzbekistan, where with the participation of the British company Oxus Mining, efforts are being made to start developing the rich zinc deposit Khandiza in the southern part of the country. Ores extracted from this deposit contain 8.5 % of zinc. As soon as its production starts there, AMMC will get its own raw material base, which, in the words of Prokhorenko, "will be supplying 52,000 tons of zinc a year".
When comparing AMMC strategy with plans of other companies of CIS non-ferrous metallurgy, one fundamental difference automatically comes to mind. While other large copper producers, such as, for example, the Ural Mining-and-Metallurgical Company or Kazakhmys, are seeking to reprocess their metal and put out products with higher prices (cables, rolled stock, radiators, powdered articles, etc), AMMC managers so far do not consider building a new plant to process non-ferrous metals. The copper rod shop was even closed down. The technology was outdated and did not have a chance to withstand competition. There is a cable-producing plant operating nearby. The plant makes copper rods of sufficiently good quality using the Southwire technology. So, cathodes are brought there. These volumes are quite sufficient for local needs.
The lack of working capital and credit resources does not allow AMMC to simultaneously implement engineering re-equipment and set up production facilities for thoroughly processing metals. Besides, significant expenses are in store to arrange reprocessing waste of the main production. Works to construct new facilities will start after the completion of engineering re-equipment. These works are to be financed with proceeds from increased sales of copper.
|
|
|
|
|
current issue

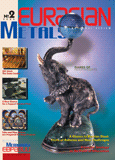
previous issue

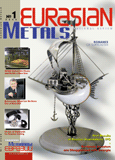
russian issue

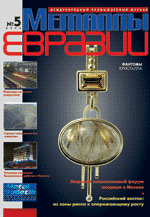
|
|