|
Magazine |
|
About |
|
SUMMIT |
|
Contacts |
|
Home |
|
|
|
|
| |
|
|
 |
#4' 2003 |
print version |
|
UVZ: DOUBLE GROWTH EVERY YEAR |
|
Yevgeny Khokhlov
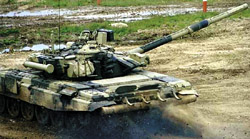 T-90 C Tank |
|
For the first time after the long break the Russian Ministry of Railways placed a major order for railroad gondola cars. The order is to be fulfilled by the Federal enterprise Uralvagonzavod (UVZ), which under the agreement will make 9,000 gondola cars. This year the enterprise will provide 3,850 of them and supplies will be completed by the middle of the next year.
All this means that the order is contributing to strengthening positions of Uralvagonzavod that in the last several years has been achieving simply fantastic rates of the production growth. Boris Mineev, the head of the public relations department and press secretary of the enterprises general director, cites the following data: in 2000 the volume of the production output amounted to 4 billion rubles, it equaled 8 billion rubles in 2001 and reached 15 billion rubles in 2002. In five months of 2003 the enterprises commodity output amounted to 11 billion rubles. (During all this period the exchange rate of the national currency has been rather stable staying at the level between 31 and 32 rubles for $1, though the ruble-strengthening tendency is becoming apparent). In the opinion of Boris Mineev, such impressive results have become possible thanks to the fact that at the height of reforms the enterprises leadership withstood the temptation to undertake hasty changes and kept the production structure intact.
RAILROAD CARS AND TANKS
The Federal State Unitary Enterprise Uralvagonzavod Production Association belongs to a special category. This is Russias one of the largest centers of producing military equipment and the enterprise has been operating in this capacity for over sixty years.
In October 1936, when Uralvagonzavod was commissioned, railroad cars were indeed its first products. But after the war started, UVZ set up tank production facilities and began making the famous T-34 tank, the best mid-size tank in time of WWII. UVZ has also taken its place in the history of military equipment as a producer of the T-72 tank, the most widely-used tank in the last thirty years of the 20th century.
The total output of the enterprises principal products in all the years of its operation is expressed in quite impressive figures: 900,000 rolling-stock units and 90,000 tanks.
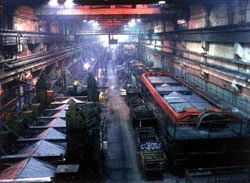 Railroad car-assembly conveyer: shop of car underframes and girders |
|
Uralvagonzavod, the construction of which started at the beginning of the 1930s, was designed by Americans. Mentioning this interesting and somewhat surprising historic action, Boris Mineev pays designers their due: the reserve of innovations turned out to be so large that even today it still has not been exhausted. The enterprises indisputable advantage is its strong infrastructure. The production association incorporates eight mills (steel mill, assembly plant, repair and construction works, tool-making plant and others). Mills are dispersed throughout a wide territory but they are relying on the unified electric power engineering and transportation network. For instance, material and component parts are transferred from one shop to another by underground conveyers. It is quite probable that precisely this technological unity did not let divide UVZ into several independent companies. But such plans were being hatched.
CRISIS YEARS
In the 1990s Uralvagonzavod experienced the most serious crisis in its history. Following the crash of the existed military doctrine, the enterprise, like many Russian arms producers, immediately lost orders from the Ministry of Defense. The Ministry of Railways, another state customer, had also to reduce to the minimum its needs. In Mineevs words, the Ministry had to stick to the principle: "we will get by with what we have: new railroad cars, rails, wheels are not needed". During that period UVZ was producing spare parts only.
Boris Mineev referred to employment figures that reflected the depth of the slump best of all. In better times Uralvagonzavod employed 36,000 people but by the mid-1990s only 26,000 of them remained. Today, there are 33,000 workers there.
As Boris Mineev believes, the enterprise managed to survive in the crisis situation thanks only to its own scientific and engineering base. UVZ means not just production. This is also a powerful design center that is leading simultaneously in several directions of the Russian industry. As Boris Mineev reminds, "we have design head offices specializing in the railroad car-building and heavy (tank) engineering. Our specialists are the leaders in a number of directions of designing, technologies and production, which are connected with space exploration, cryogenic technology and, in particular, with transporting strongly chilled gases". Precisely this scientific research-and-design potential permitted the enterprise to quickly turn itself over to the needs of the market.
Uralvagonzavod started restoring its production facilities choosing such a new direction as manufacturing road-building machinery. It developed and brought to the market wheel and crawler-mounted excavators, compact universal loaders for transferring load weighing from 500 kg to 1,250 kg. UVZ also began to make machinery designed for emergency situations. The range of its products started to include fire-engines and the whole family of armored machinery developed on the basis of the tank engineering: repair service-and-evacuation machinery, bridge-layers, mine-clearing equipment.
Despite the absence of state orders, Uralvagonzavod has maintained its traditional specialization in tank and railroad production. Boris Mineev considers this a special merit of the enterprises management. It is hard to dispute with his opinion. The marketing structure of UVZ turned out to be more reasonable than the policy of state structures: as soon as the crisis decade was over, the main products of the military and civil types were called for again.
TUMULT AFTER BREAK
The Ministry of Railways is facing the necessity of replacing the railroad car fleet on a large-scale. The process of its degradation is rushing headlong: 65% of the rolling-stock have already been outdated. Boric Mineev is supporting this figure with his own facts. "Sometimes there is nothing available to ship products on. Railroad men are bringing echelons of drays in but there is nothing to choose from: they are all in such an unusable state that they are not subject even to restoration repair", he says. It is obvious that UVZ and its partners have an enormous market on their hands. "We have been practically doubling volumes of producing railroad car fleet. We have already started lacking metals and metal articles, especially wheels", says Mineev.
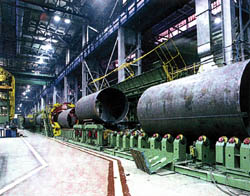 Production of railroad tank-wagons. Severstal JSC is providing a 10mm-steel sheet for this purpose |
|
By his estimates, the Russian suppliers of railroad wheels Vyksa Steel Works and Nizhny Tagil Iron & Steel Works (NTMK) satisfy only one third of needs, while the rest of wheels is imported from Ukraine. It sounds somewhat paradoxical, since the production facility territories of Uralvagonzavod and NTMK are located next to each other being divided just by the fence. Both were being built simultaneously so as to form a single production complex. NTMK was always considered a metal supplier, to UVZ in the first place. It is quite probable that their cooperation of the past will be restored, the more so, as by taking into account market conditions NTMK intends to start reconstructing its tired-wheel shop.
Boris Mineev especially stresses that in crisis years Uralvagonzavod was not just biding its time but was engaged in developing new types of products. In parallel with production of railroad cars it worked out the technology of manufacturing railroad tank-wagons for transporting heavy and light oil products. By the way, precisely these tank-wagons happened to be in demand in the first place and they were put on the production line. Market prospects for this product are estimated as very good. The share of oil in the cargo transportation on Russias territory is very high and there is hardly a reason to doubt that the need for rolling-stock for these purposes will be growing.
Apparently, manufacturing railroad cars of aluminum section will become another promising direction. Such a production is not yet existent in Russia, although there are at least two objective conditions for it: the particularly high volume of railroad cargo transportation and the excess of aluminum. Hoping for future orders designers and production engineers from UVZ have already been developing samples of such railroad cars.
|
The Russian Ministry of State Property Management is an exclusive owner of the Uralvagonzavod Production Association. Nominally, UVZ is under the Russian Agency of Conventional Weapons being its largest enterprise. |
|
CONTRACT WITH INDIA
Uralvagonzavod remains Russias only operational tank-making plant, although, according to Boris Mineev, the share of the state defense orders in the total production volume of UVZ amounts to only 1.5 %. The rest falls on civil products. That is a quite typical result of the conversion, which was implemented in the Soviet military industrial complex and which had neither a thought-out program nor funds. It reminded more of a collapse.
That is the way things are with other producers of armored machinery. The Kirovsky plant (St. Petersburg) stopped making heavy tanks completely. For the second year in a row the Omsk plant has been bankrupt and has to sell its equipment. In contrast to UVZ this plant could not be saved as a single production complex and, assumingly, it is now to restructure the plant preserving the viable production facilities, especially the foundry. The tank-making direction remains curtailed: the design office and two shops. If necessary, this base may be used for making between 40 and 50 tanks by using components and units that are still available since the Soviet times. The case in point is the T-80 tank, which was developed more than 10 years ago. In the opinion of specialists, there is nothing more can be done in Omsk, if not to begin reconstructing the plant anew.
The Russian tank-making industry managed to stay in the arms market thanks to a major order from India. In 2002 Uralvagonzavod provided the Indian armed forces with 310 advanced tanks of the T-90 C type.
As Boris Mineev insists, "this contract allowed our enterprise to revive. And not only to revive: we received an impulse for a new development". Last year $32M were allocated for technical re-equipment and investments in the current year are planned to increase 1.5 times as much, Mineev says. He stresses that UVZ itself accounts for 98% of these investments. Not only individual types of equipment but complete technological lines are also purchased. For example, a molding line was bought in Italy, Austria sold a radially forging machine, Germany and Switzerland provided the most advanced processing machines. Right now Uralvagonzavod is considering proposals of Japanese companies to re-tool its machinery equipment. Boris Mineev calls these proposals "interesting enough". Many Russian enterprises, of course, are also among suppliers of equipment but, in the words of Boris Mineeev, they can match the level of todays requirements at best, while Western samples "really represent technologies and machinery of tomorrow".
WILL PRODUCTS OF UVZ BREAK THROUGH INTO EUROPE?
In the epoch of the Cold War Europeans were frightened with scary images of a tank attack from the East. Of course, tanks made at Uralvagonzavod formed a considerable part of these thousands and thousands armored vehicles prepared to fight the NATO armies. Today this threat is absolutely non-existent. But it cannot be ruled out that products with the UVZ trademark will, nevertheless, turn out to be in Europe.
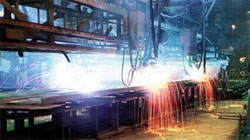 Plasma-cutting installation |
|
The enterprise has already had export orders for road-building machines and railroad cars. So far its export shipments are going, mainly, in the Asian direction. "Just recently we sent excavators to Vietnam and earlier there were supplies to Iran", says Boris Mineev. "We are selling railroad rolling-stock, spare parts for railroad cars to CIS member countries: we have set up joint ventures in Kazakhstan, Uzbekistan, Estonia". But, general director of Uralvagonzavod Nikolai Malykh, according to his press secretary, "is setting a more serious task: to enter European markets". The enterprise is doing some preparatory work. Products of UVZ have already been certified by European auditing associations in Germany and Switzerland. Like most Russian products, they have problems of the double nature: while having good performance characteristics, they are lagging behind by design, ergonomics...
Market successes of Uralvagonzavod have a positive impact on other Russian enterprises, including the metallurgical ones. The cost of metal that this engineering giant consumes every month is estimated at $10M. Along with NTMK the major suppliers of steel rolled stock to UVZ are the Magnitogorsk Iron & Steel Works and Severstal. "The wide range of our works is tied up to the use of metal. In addition to the high-capacity metal-working and foundry production facilities we are also dealing with powder metallurgy, the technology of casting non-ferrous metals", explains Boris Mineev.
In its turn, UVZ is starting to meet requirements of metallurgists. Recently, it manufactured a copper-wire rolling mill to the order from one of the non-ferrous metallurgy enterprises. While implementing the project, UVZ was applying its own developments and original engineering solutions. When telling about this project, Boris Mineev draw attention to the reaction of Chinese specialists, who were among the customers representatives. In his words, the Chinese "were amazed", when they saw this mill. They were shocked by its "crazy productivity" coupled with a good quality of the finished product.
|
|
|
|
|
current issue

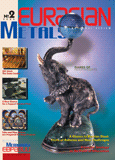
previous issue

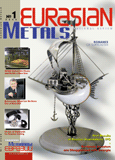
russian issue

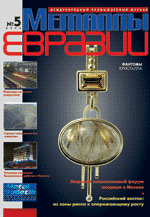
|
|