|
Magazine |
|
About |
|
SUMMIT |
|
Contacts |
|
Home |
|
|
|
|
| |
|
|
 |
#6' 2003 |
print version |
URAL WORKS: MONUMENT OF HISTORY |
|
Margarita Kuzovkova
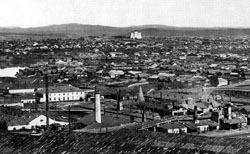 Demidovs Nizhny Tagil Iron-Smelting & Iron Works, late 19th early 20th centuries (view from Fox mountain) |
|
he Nizhny Tagil Iron-Smelting & Iron Works was founded in 1725 by manufacturer Akinfy Demidov. For the whole 18th century the works remained one of the worlds largest and technically perfect enterprises having the complete cycle of iron production. There were 18 buildings with 27 different production facilities. The works products, ball-band and bar iron of the ”Old Sable” grade, were in much demand in European markets and, above all, in England, which at the end of the 18th century accounted for about 50% of the Tagil iron.
By that time the works settlement, the future city of Nizhny Tagil, became the center of the mining and metallurgical district, the capital of the Demidovs vast industrial empire.
The works layout was finalized by the first half of the 19th century and it was typical for that time: there was a dam with extended wooden conduits and in the center, under the dam, there stood the blast-furnace factory. On both sides of the conduit coffer, over 200 m long, there were production process facilities, the third group of buildings contained metalworking shops, along the works perimeter there were n facilities and services that did not need water power.
After having been in operation for 262 years altogether, the former Demidov works finally stopped its production activity: the rolling, open-hearth and blast-furnace shops were shut down in 1961, 1978 and 1987 respectively. But since then the enterprise has started a new life, this time around as the works museum, the first and still the only one in Russia.
And the old works served as the base for the Nizhny Tagil Iron & Steel Works, one of the leaders of the Russian steel industry.
VYSOKAYA MOUNTAIN
The Vysokaya mountain that gave birth to the works contained almost pure iron ore. In 1721 the development of its southeast slope began because that was where the richest ores were located. They practically did not have sulfur and phosphorus but, instead, contained copper, which provided iron with anticorrosion properties and softness.
The ore extraction was done the most primitive way: ore was collected on the surface, piled up and, then, it was roasted for 40 days. Later, the ore deposit was developed by benches. At the beginning of the 19th century gunpowder was applied for rock rupturing. The wide use of powerful equipment started in the 20th century only.
In the years of the deposit development the volume of extracted ore totaled 223 million tons. As people in Nizhny Tagil jokingly say, the Vysokaya (high) mountain was replaced with the Deep quarry . The quarry is 800 m wide, its length by edges is 1,100 m and the depth, if measured from edges, is 200 m. In 1990 the main quarry was closed.
BLAST-FURNACE PRODUCTION
When the blast-furnace production was being developed in Urals, the experience of Europes best iron-smelting enterprises was taken into account. Foreign metallurgists, namely the British, Swedes, Germans and the Dutch, participated most actively in construction works on the blast-furnace building. Furnaces were erected in pairs, they had a circular section and only their hearths had a four-sided shape that was kept till the mid-19th century.
In those years the first blast furnaces at the Nizhny Tagil Works, which were built in 1725, were among the largest and most productive. Their height reached 13 arshines (the old Russian measure of height; 1 arshine = 0.711 m = 2 ft.4 in.) and the daily output amounted to 400 poods (the old Russian measure of weight; 1 pood = 16.38 kg) of cast iron. Developing the ferromanganese smelting was a great achievement as well. For this purpose engineer K. Frelik constructed a small blast furnace with a detachable hearth of the Scotch design. In the winter of 1875/76, for the first time in the world, the high-grade ferromanganese (between 68% and 80%) was smelted there with the use of charcoal.
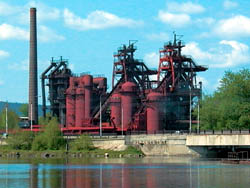 Nizhny Tagil works museum, late 1990s (view from dam) |
|
Considerable increase in cast iron output was ensured by the "elliptical" blast furnaces, which were constructed in the 1860s. This original method led to raising furnace volume without the need for corresponding boost of blowers capacity.
The radical reconstruction of the blast-furnace complex took place in 1930, between 1951 and 1954 as well as in 1971. All in all, in the years of their operation the Tagil blast furnaces produced 14 million tons of cast iron.
Exhibits of the blast-furnace shop date back to the period between the 1930s and 1970s. The blast furnace binding of the late 19th century also remains intact.
OPEN-HEARTH SHOP
The so-called old German bloomery method was the first technology of getting iron that was used at the works. It was barely changed for a whole century. In 1826 experiments with producing iron "the Swedish way", i.e. by the Walloon bloomery method, were conducted. However, they did not lead to the full industrial use of the new technology. In 1859 the Tagil steelmen conducted the first experiments to get Bessemer steel but due to the absence of orders for Bessemer metal this method was not further developed.
Construction of two new open-hearth furnaces with charge of 400 to 450 poods of cast iron began in 1875. These furnaces were erected along the line of French open-hearth furnaces. They processed cast iron that was preliminarily decarbonized. Carbon was burned out in Bessemer retort that was installed near blast furnace and started operating by blast-furnace blower. The portion of 250 poods of cast iron was brought to retort directly from blast furnace and was cleaned out by blowing for 8 to 15 minutes. After that the refined metal was fed into open-hearth furnace.
In order to develop the open-hearth production, it was necessary to master manufacturing dinas and producing ferromanganese, ferrosilicon and silicomanganese.
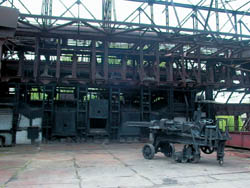 Open-hearth furnace (built in 1950), operating site (2003), Prudenkos charging machine, 1891-built shop (front). Open-hearth exposition, works museum |
|
In 1891 a new open-hearth shop with two furnaces was built. Their capacity amounted to 820 poods of cast iron; each of them provided three casts a day. Gas, which was produced by special wood-burning generators, served as their fuel.
Pouring of steel was done under the technology that in those years was considered up-to-dated. It was the siphon method with the use of steam valve and ladle. That is why, in addition to furnace aisle there was a pouring bay. Water feed to the open-hearth shop was quite original. An elevated water tank with the capacity of 1,225 cubic meters was constructed on the nearest height and the shop was connected to a cast-iron water pipe. Remnants of this tank have been kept till now.
The shops modernization in the 20th century included installing electric cranes and a charging machine (in the 1930s), increase in capacity of furnaces as well as their switch to fuel oil (in the 1950s). At present, there are walls and trusses of the building, bridge electric crane, open-hearth furnace, teeming pit with bottom plate and moulds, which are still available. But all of them need restoration.
ROLLING PRODUCTION
The Nizhny Tagil Works was one of the first to start using rolling equipment. Even the 1757 description mentions "flattening factory", which produced 4 kinds of thin strip iron. In the 1760s three fourth of all Ural "flattening iron" were manufactured precisely at the Nizhny Tagil Works.
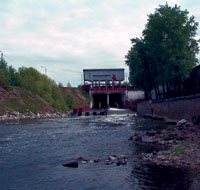 Nizhny Tagil Dam, Veshnyashy Cut (Dam: constructed in 1720, reconstructed in 1928). View from bridge |
|
In the 19th century the works made special efforts to develop sheet rolling production. Two shops were built for this purpose in the late 1820s and the early 1830s. By the 1840s the technology of rolling sheet iron was developed. Later it was called the "old Ural technology with a little littering". Iron sheets were 0.5 mm thick and 1.420 ő 710 mm in size.
In 1896 a new building for rolling production was constructed at the site of the first open-hearth furnaces. It was erected with in four lines, with arched roofs leaning on columns. In 1902 a building of the sheet-rolling shop was raised nearby. This building was for rolling and final finishing of sheet iron. It was unique because the buildings columns and overlapping trusses were a single metal structure with riveted joints. The delicacy, lightness and strength of trusses make even todays builders admire.
Due to expanding rolling production new buildings for sheet rolling, sheet flattening and sheet cutting facilities were erected near the shop between 1928 and 1933.
In the fifties of the 20th century there were 1,000 people working at the rolling shop. The working conditions remained hard, the production itself was unprofitable and, finally, it was shut down. The equipment was removed: a part of it was transferred to neighboring works, another part was re-melted and just little was passed to the museum including columns and girders as well as the mills drive.
MECHANICAL PROCESS
Enormous distances separating Ural districts from each other as well as from Russias central regions and unreliable railroad communication forced works to manufacture most of the needed equipment themselves. The Nizhny Tagil Works was no exception. In the sixties of the 18th century already there were hammer-making and forge bellows factories, blacksmiths and joiners repair shops. Later, a machining factory was set up. It manufactured steam engines and other mechanisms not only for the works own needs but for other Ural factory owners as well. By 1875 there were over 70 different machines in the machining shop.
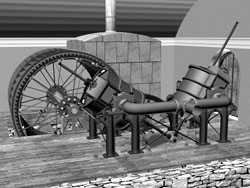 Blower, blast-furnace shop, Nizhny Tagil Iron-Smelting & Iron Works, 1856 (computer model, 2002) |
|
It was significantly restructured in 1892. Cast crane girder columns and bridge crane with hand drive were installed. Two transmissions with belt pulleys were arranged along the shop to operate machines. Since the machinery equipment was replenished all the time, by the 1930s the length of belts was measured in kilometers. Transmissions were put in operation by water turbine that was later replaced with electric drive.
The crane made in 1892 remains in the shop.
POWER FACILITIES
The construction of the Nizhny Tagil Works began with dam erection. This dam was one of the largest in Urals: its length reached 104 sazhens (the old Russian measure of length; 1 sazhen = 2 m 13 cm), the height amounted to 5 sazhens and the width in the lower part was equal to 40 sazhens. As a result, the pond was formed and today it occupies the area of 16 square kilometers and is up to 4 meter deep.
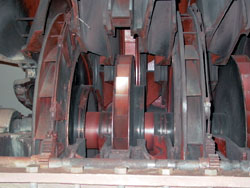 Brown-Bovery blower, blast-furnace shop, Nizhny Tagil Works, 1930. Blast-furnace production exposition |
|
There were three cuts done in the dams body. One of them was intended for adjusting water level in the pond and discharging excess flood water. Another was to ensure water supply to blowers of blast furnaces. And the third one provided water to bloomery and rolling shops. Blowers were made of long four-sided pine pipes. There was a branchy system of side pipe-bends leading directly to wheels.
In 1899 the old wooden coffer was replaced with metal water conduit having the diameter of 3.8 m and length of 260 m. The conduit was riveted from iron sheets 12 mm thick. This coffer was used till 1958 and now it is almost in the working order.
The main type of motors used in Urals in the 18th century was overshot wheels. Bloomery hammer wheels had the diameter of 12 feet; the diameter of rolling and blowing machines varied from 15 to 18 feet. The total capacity of all water wheels at the Nizhny Tagil Works amounted to 610 hp.
In the 1840s and 1850s the use of water turbines of different designs began. At present, there is one of such turbines at the works that is in the satisfactory condition, although it is significantly corroded.
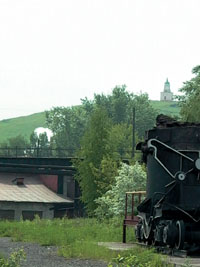 Vegetation area, works museum. Fox mountain view from works museum (Rolling-stock exposition) |
|
Steam engines happened to be used at the works somewhat earlier than water turbines but they played an auxiliary role. They were supposed to substitute for water engines during repairs or in cases of water shortage.
As it turned out, the Nizhny Tagil Works started to use electric power without getting through the steam application period. In 1895 a small electric power station was constructed with two steam engines and constant current generators. One engine of 100 hp was intended for the machining shop and the other with 75 hp provided electric light to the works and living quarter.
In 1913 an electric power plant with a higher capacity was built. It was equipped with steam boilers supplied by the British company Sterling. These boilers are in good state and they are still providing heat to a part of the city.
WORKS MUSEUM: YESTERDAY, TODAY, TOMORROW
For over two centuries the Nizhny Tagil Works had been building up the industrial fame of the Russian Empire. Its metal contributed to the economic upsurge not only of Russia but of many countries in Europe as well.
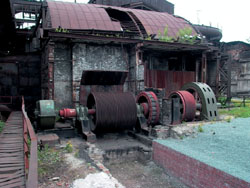 Transmission line, rolling mill, 1924 (small pulley with electric engine, fragment). Rolling production exposition, works museum |
|
During years of its operation the works underwent reconstruction and changed its look. The works main production area formed by the end of the 19th century has been kept intact till today. There are elements of different time periods:
From the 1720s to 1730s: water system (dam, pond, riverbed);
From the 1820s to 1840s: the works office, forge shop, stable, part of rod building walls, wall of the blast-furnace shop, part of the bloomery building walls, storage facilities;
From the mid-19th century to the beginning of the 20th century: the machining, open-hearth, sheet-rolling and copper-boiler shops, electric power station, water coffer, rail brace shop;
Between the 1920s and 1930s: the blast-furnace and sheet-cutting shops, lock device, casting machine.
All production facilities have equipment intact.
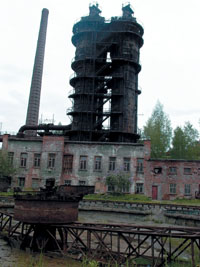 Gas purification, blast-furnace shop, 1955. Front: slurry pond, gas purification building, two scrubbers |
|
All of them are registered in the State books as historic monuments. They make it possible to precisely and fully illustrate the history of a typical Ural works. Thanks to the citys favorable social and economic environment and, above all, to sponsors assistance, the Tagil Iron & Steel Works, the works museum has a chance of being preserved for future generations in its original shape.
However, there are also complications in keeping this unique historic monument:
the presence of functioning production facilities on the museum territory;
the degree of individual units safety taking into account their age differences;
metallurgical units after years of operation under high temperatures are now in the "hostile environment", i.e. they are influenced by natural factors;
areas that need conservation are large and they require big financial investments;
Urals harsh climate does not allow to keep the historic museum open all the year round.
After analyzing the situation it was decided: to preserve the oldest, most interesting and informative part of the works as a reserve zone with the minimal use. The rest of the territory will be used as a recreation area and it will become part of the future historic reserve infrastructure.
Here are some examples of how some of these ideas are to be implemented: there are plans to use the 1950 blast furnace that has the volume of 247 cubic meters and is in a rather satisfactory state as a shaft furnace for metalizing pellets. The infrastructure zone with the stable being in a bad state is to be restored and used as stable of a race track that will be built on the territory, which is now vacant.
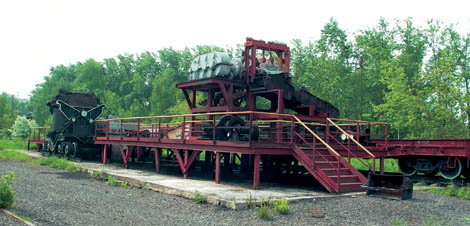 Equipment exhibit, works museum territory, casting machine, 1930 |
The Nizhny Tagil works museum is a unique monument of Russias industrial heritage as well as a unique place to preserve and use it in Nizhny Tagil and all over the country. In order to attract investments to keep, restore and use the monument, it is expected to make it the center of the Russian metallurgy.
|
|
|
|
current issue

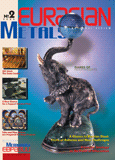
previous issue

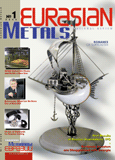
russian issue

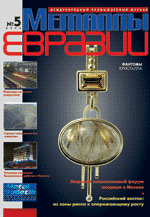
|
|