Yevgeny Khokhlov
A new plant has been built in the city of Novgorod, which will produce copper cathodes by scrap processing. Its annual production capacity amounts to 40,000 tons. The plant is drawing attention because it is the first metallurgical enterprise that has emerged in post-Soviet Russia. It proves that the countrys metallurgy is ready for innovations. In many respects the concept of the project is above the existing level of technologies and not only in the Russian copper industry.
RIGHT PLACE
Novgorod, Russias most ancient city (historically it is also called Veliky Novgorod Great Novgorod), is famous for its history, magnificent architectural monuments but it was never considered an industrial center. Having no ore base the city did not have its own metallurgical production facilities. That is why the selection of the site to build a new plant there was quite unexpected.
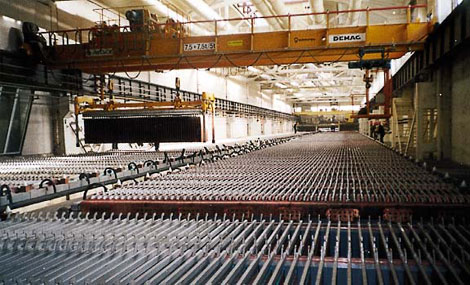 Electrolysis plant |
Andrei Vorotnev, the plants general director, says that at the beginning he was looking for a site closer to the seacoast taking into account the world experience. Precisely this way metallurgical production facilities are located, for example, in Finland. In this sense it would seem more reasonable to give preference to St. Petersburg, where Russias main Baltic commercial ports are located. Besides, in Vorotnevs words, along with Moscow this region "has the biggest metal turnover and the most considerable volumes of copper scrap".
But despite all this the subsequent investment analysis proved that the selection of Novgorod was more advantageous. Costs of ground areas, labor force and other resources in this region are much lower than in neighboring St. Petersburg. The transportation infrastructure there is well developed and, by Russian standards, being located 200 km away from the nearest seaport is just insignificant. However, as Andrei Vorotnev stresses, the most important factor in favor of choosing Novgorod had nothing to do with economy. It was the ability and willingness of the Novgorod administration to cooperate with business enterprises. Vorotnev says that investors received just "a moral support" from governor Mikhail Prusak but it was enough to prevent the local bureaucracy from impeding the project. On the contrary, it provided assistance to pass the project as fast as possible through all stages of getting necessary agreements and permissions. As a result, investors plans are being implemented much easier than it is usually done in Russia. "If the governors position was different, then, we probably would not start this project at all", notes Vorotnev.
According to Vorotnev, the total amount of investments, including expenses on construction works, acquiring equipment and technologies came to $35M. The plants shareholders did not seek borrowings and invested their own funds. Investors hope to recoup them in 5 years.
FINNS, RUSSIANS TO MAKE MAJOR BREAKTHROUGH IN METALLURGY
As its managers believe, the Novgorod Metallurgical Plant or NMZ (that is the name that the enterprise has received) signifies a major breakthrough in non-ferrous metallurgy. In Russia, which does not have a single mini-plant even in the steel industry, the setting up of such a copper production enterprise represents all the more interesting and important task.
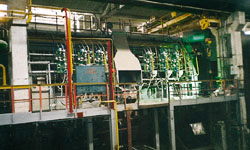 Anodic tilting furnace Maerz-Gautschi to process rich copper scrap |
|
Technologies and ideas of the project belong to the concern Outokumpu. This firm also supplies equipment and implements the whole complex of engineering works. The concepts essence is to make it possible to process raw materials with the relatively low content of copper (brass and bronze) simultaneously into cathodes and copper scrap. Both processes are combined into a single technological flow. At the same time, a stable high quality of products, efficiency of production and its ecological safety are guaranteed. If the project is successful (and its participants do not put it in doubt), Outokumpu intends to actively advance this concept to world market.
The plant itself is a comparatively small production building with compactly installed units and auxiliary equipment. The main technological links are anodic tilting furnace Maerz-Gautschi to process rich scrap (from 92 % to 99 % of copper), vertical tilting and rotating fuel-oxygen converter for secondary raw materials with the copper content from 56 % to 92 % as well as the electrolysis complex having 142 baths made of organic concrete, durable and acid-resistant material.
The plants chief engineer Yuri Venziga is highly appreciative of the available equipment. In his opinion, it really conforms to technologies of the 21st century. During the test run process each unit performed quite well. There were problems only while docking individual components and adjusting technological processes. These failures worry Outokumpus representatives a little but managers at NMZ consider them "ordinary" and do not see any connection with the quality of the projects development. As Venziga believes, the greatest problem is the shortage of qualified personnel.
It is noteworthy that only one year has passed since the signing of the contract and start-up of adjusting and commissioning works. It is not that simple in such a short time to recruit specialists, to hire and train workers of needed specialization. What is more, one should keep in mind that this campaign had to be carried out in a region that has no experience in metallurgy.
"It is, of course, impossible to form a team with one attempt", concedes Andrei Vorotnev. "In the forming process the weeding out is unavoidable. But the skeleton has already been formed", he adds. The number of the enterprises personnel is comparatively small: from 400 to 450 people at most. Vorotnev notes that it is 10 times less than at the Kyshtym Electrolytic Copper Plant, which has the volume of producing copper cathodes only twice as much. Thus, by the main index of efficiency NMZ is obviously breaking away from the most Russian enterprises and reaching the level of achievements by the worlds metallurgy.
ECOLOGISTS REMAIN VIGILANT
The new plants construction was accompanied by protests. "Copper compounds and other dangerous substances emitted into the atmosphere can harm the environment and peoples health, cause destruction of historic monuments". That is the general theme of statements made by independent ecologists that is picked up by mass media and some of Novgorods public. The general director of NMZ takes them in stride as something unavoidable but transient. "In any region any production project meets resistance of ecologists", says Andrei Vorotnev. He reminds that there were protests in Novgorod against constructing a chocolate factory, which was being built by the company Cadburry, as well as against an enterprise to produce the Dirol chewing gum. In the opinion of Vorotnev, in cases like these the best response is a qualified ecological examination.
The plant has received positive expert judgment by the State nature-conservation service and results of an independent public examination. In both cases it has been stated that the impact of NMZ on the environment is close to zero.
Tatiana Filippova, the press secretary at NMZ, suggests to look at ecological tasks from the point of view of business interests. For example, just a simple operation makes slag from the copper-smelting production a marketable product. It has customers as is the case with solid substances of waste gases. And the warm purified air is used for heating premises. All these are "additional sources of profit used to recoup the project", says Filippova adding that the plant "does not intend to discard them".
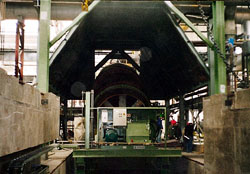 Tilting and rotating fuel-oxygen converter to process scrap with the copper content between 56 % and 92 % |
|
The ecological service at NMZ does a regular monitoring of the environment. The analytical laboratory, which is equipped with a modern complex of equipment supplied by the companies SouthWire and Thermo Elemental, is capable of conducting over 67 hours of making different definitions a day.
In the opinion of NMZs general director, the period, when it was possible to make unfounded speculations about ecological dangers of the new production facilities, has already passed. "I think this question has been settled", says Andrei Vorotnev. "The enterprise is already in operation now and those, who still doubt the objectivity of our data, can check them in practice".
READY TO COMPETE IN OPEN MARKET
As far as Russia is concerned, the project of the plant based exclusively on resources of secondary raw materials is a rather risky venture. Volumes of copper scrap formation are limited and, according to experts predictions, they will not be increasing. The market is already experiencing its deficit, the struggle against tough impact on competitors and the use of protectionist measures is still going on. Export shipments of non-ferrous metal scrap, including copper scrap, are now being restrained by high export duties that are reaching 30 %. And what will happen, if they are not removed?
"As a matter of fact, this is one of the reasons that prompted us to build precisely such a plant and precisely here, at this site", says Andrei Vorotnev. "We know that sooner or later the market will be opened and scrap will be shipped abroad. And our task is to be competitive in this market".
The general director of NMZ is confident that the plant will be completely provided with raw materials. In his words, the estimated volume of raw material supplies is to amount to 50,000 tons a year or a little more while the copper scrap/brass and bronze ratio will be 2:1. Vorotnev thinks that it is not too much on the national scale, especially so, if one compares NMZ with such a large consumer as Uralelektro-med (affiliated with the Ural Mining & Metallurgical Company or UMMC).
In Vorotnevs words, the projects investors hope to use the existing commodity and raw material flows to their advantage. At present, the bulk of copper scrap in the countrys European part, where the main centers of using copper products are located and where their utilization is concentrated, is brought for processing to the Ural enterprises Uralelektromed and Kyshtym Electrolytic Copper Plant. The finished products, copper cathodes, are mostly brought back. Thus, the transportation extent turns out to be unreasonably large.
The scheme of processing secondary raw materials at NMZ looks preferable not only due to significant reduction of transportation expenditures. "The task of our enterprise is to optimize all expenses", says Andrei Vorotnev, and, in his opinion, to this end all options are available: "the enterprise is compact, mobile and, as preliminary calculations show, very sound economically".
Forming the new enterprise has one peculiarity. The trading structure, which earlier was a supplier of copper scrap for UMMC and an affiliate of this company, became the plants shareholder and investor. Now it is becoming an independent market player and immediate rival of UMMC.
However, Andrei Vorotnev believes that there will be no copper war and that the rivalry will stay within bounds of a healthy competition. "Scrap suppliers have no corporate attachments", notes Vorotnev. "They bring their scrap to those, who offer a higher price for it. Accordingly, enterprises are vying for those, who can pay more. And after that pure economic considerations, such as production costs, expenses, start playing their role. The one, who is the most sound economically, always wins".
Already in December 2003 the Novgorod Metallurgical Plant, as the general director says, will reach its design capacity. The quality of copper cathodes is high enough: their copper content amounts to 99.967 %. The plants specialists are confident that these products packaged by European standards will successfully pass the certification procedure at LME and will be in high demand among Russian customers as well as in world market.
|