|
Magazine |
|
About |
|
SUMMIT |
|
Contacts |
|
Home |
|
|
|
|
| |
|
|
 |
#1' 2004 |
print version |
TITANIUM IN POWER ENGINEERING: NEEDS ARE UP AND CLIMBING |
|
Boris Postylyakov, Anatoly Stroshkov
he industrial manufacturing of products from titanium and its alloys grew up fast half a century ago solely for using the unique properties of this structural material in developing new military equipment and weapons. As volumes of the titanium production were increasing, it became accessible to civil industries as well. At present, the titanium world consumption is about equally divided between the aerospace and military sectors, on the one hand, and the rest of consumers, on the other hand. Accordingly, the Wests leading companies that make titanium products for the aerospace economic sector are based in the U. S. while major companies of producing titanium for civil industries are located in Japan.
Table 1 shows the distribution of Japans rolled titanium among consumers in 2002. It is well known that the structure of consuming Japanese rolled titanium reflects the pattern of distribution of titanium products in the whole non-aircraft world market. As the table proves, the priority role belongs to industries that make use of titanium specific natural properties, especially the high level of its mechanical characteristics and corrosion resistance.
Table 2 shows the structure of the range of titanium rolled products made in Japan in 2002. The main products of the Japanese titanium industry are welded titanium tubes and strip billets for making them, which jointly account for more than 40% of all rolled titanium production volume.
Since the beginning of the 1970s welded titanium tubes have been widely used to produce condensers for turbines of thermal and nuclear power plants that operate on sea water as well as heat exchangers of quenching systems that use process water, water-desalinating plants, heat-exchange devices at chemical production facilities.
Heat-exchange devices made of titanium alloys have considerable advantages over similar items manufactured from copper, copper-nickel alloys and corrosion- resistant steels, which still are widely used in industry.
First, titanium alloys are highly corrosion-resistant in many aggressive mediums, particularly in sea water as well as in water and steam with high temperatures (up to 350 oC). In contrast to copper and copper-nickel tubes titanium tubes are not apt to corrosive and erosive destruction of surface by quenching water. This advantage is particularly evident in systems, where compressed quenching water is used. Thanks to the high corrosion resistance of titanium, leakages of hermetic cooling systems as well as pollution by impurities from other systems and their components are prevented. As is usually the case, emergencies because of such leakages force to reduce output power at plants or even to close them down for repairs.
Another advantage of using titanium tubes in heat-exchange equipment over others made of different materials is a considerably lower susceptibility of tubes interior surface to get overgrown with organic additives contained in quenching process water. At the same time there are systems that have been developed for continuous and effective cleaning of titanium tubes surface from dirtying by small sponge balls so as to restore characteristics of heat exchange.
As far as the use of titanium in heat-exchange devices is concerned, it has two shortcomings as compared with traditional materials: lower heat conductivity properties and high cost of titanium-made equipment. Its heat conductivity is twice as low as the heat conductivity of copper alloys. But this shortcoming is balanced off by the reduced thickness of titanium tubes walls being twice as low as the one of tubes made of other alloys that are used for these purposes. Mechanical properties of titanium permit to use in heat-exchange devices tubes with wall thickness of up to 0.5 mm. There are reports about using titanium tubes with wall thickness of 0.3 mm and 0.4 mm at one of Japans electric power plants.
The use of relatively expensive titanium-made heat-exchange equipment at thermal and nuclear power plants is justified by a considerable extension in time periods between their repairs. Japanese and American companies conducted studies of corrosion resistance of titanium tubes in operating heat-exchange devices allowed to set the duration of their service life between 40 and 50 years.
The international community has a large experience of using titanium welded tubes in condenser and heat-exchange devices. For example, Titanium Japan reports on a 20-year experience of operating titanium-made evaporators in water-desalinating plant in Al Jubayl (Saudi Arabia). There is a complete absence of corrosion of titanium tubes. It stresses the competitiveness of titanium used in these structures in terms of both economy and duration of service life. Another publication writes that for over 30 years thin-walled (0.5 mm and 0.7 mm) titanium tubes made in Japan have been in operation in condensers of nuclear and common electric power plants, chemical plants and water-desalinating plants.
According to Siemens AG (Germany), the major producer of heat-exchange equipment, as of 1995, about 12 billion meters of titanium tubes were in operation in heat-exchange devices made by this company. Thanks to the excellent corrosion resistance of titanium, no corrosion whatsoever has been found so far in the companys heat-exchange devices. The first such devices with the use of titanium tubes were produced by Siemens AG in 1981. It presented a diagram that showed the dynamics of replacing traditional tubes made of copper-based alloys and stainless steel with titanium tubes in heat-exchange devices (Fig. 1).
The world consumption of welded titanium tubes amounts to over 7,000 tons a year. About half of this amount (up to 3,500 tons) is produced by Frances Valtimet. Founded in 1997 jointly by the French firm Valinox Welded and the American company Timet, it has become the worlds largest supplier of welded pipes made of stainless steel as well as titanium alloys for power engineering, water-desalinating plants, oil-and-gas and chemical industries. The companys production capacity amounts to approximately 9,000 tons of pipes a year. In January 2003 the U.S.-based company International Tubular Products (ITP) has been also acquired. Strip needed for making tubes is supplied to enterprises of Valtimet by Timet as well as by Japans Nippon Steel Corp. and Sumitomo Metal Industries. Another Japanese company Kobe Steel also has considerable capacities to make welded titanium tubes. The total annual production volume of these three companies amounts to approximately 2,500 tons of tubes and 4,000 tons of commercial strip.
Besides, welded titanium tubes are made in South Korea, Italy, Germany and other countries. Their total production volume is between 1,000 and 1,500 tons a year.
The supplier of seamless and welded titanium tubes in Russia is the Verkhnyaya Salda Metallurgical Production Association (VSMPO). Starting in the 1960s welded tubes with wall thickness of 1.5 mm to 2.5 mm and with 25 mm to 102 mm in diameter were made at its two tube electric forming mills mainly for enterprises of the chemical industry. The total tube production volume exceeded 18,000 tons. And although by their range and quality these tubes did not meet international standards, the experience of producing them, operations in the world market and acquaintance with its requirements made it possible to take the next step. The leadership of VSMPO decided to set up a modern tube-welding production that would meet requirements of foreign customers.
In 1997 VSMPO installed two tube electric-welding lines made by the German company Opperman. The production section was provided with checkout test equipment: ultrasonic check devices, pneumatic and hydraulic test instruments. Specialists at VSMPO developed the technology of welding tubes made of the alloys Vt1-0, Vt1-00, Ot4-0, Grade 1, Grade 2. In 1998 it started supplying welded titanium tubes that were produced in accordance with the ASTM B338 / ASME SB338 international standards. Together with expert organizations VSMPO conducted certification of the welding technology, examined properties and methods of controlling quality of welded tubes. All this made it possible to ensure the use of tubes by power engineering enterprises, including those of nuclear power engineering. The quality-control system of making welded thin-walled tubes of titanium alloys was certified by the company TUV. As a result, it became possible to get rid of Russias lagging in using welded titanium tubes as a progressive structural material.
Welded tubes produced by VSMPO are exported to markets in more than 10 countries. They are used in power engineering, chemical and oil industries. In 2001 and 2002 supplies of 360 tons of tubes were shipped for the condenser of Indias nuclear power plant Tarapur. Currently, Indias order to supply 590 tons of welded tubes for the nuclear power plant Kudankulam is being fulfilled. In 2002 tubes were shipped under contracts with the companies Permascand AB (Sweden), Ameuro Metals B.V. (Netherlands) and some others.
VSMPO also makes ready-for-use heat-exchange equipment of a wide dimension-type range, in which both seamless and welded titanium tubes are used dependent on the purpose of the given equipment.
Due to the growing demand for welded titanium tubes the leadership at VSMPO keeps making investments in production development. Another four tube-welding lines are being readied for commissioning. This will allow the Association to offer customers a wider range of considerably more welded tubes in 2004 (see Table 3).
At the annual international conference of ITA on titanium held in Monterey (the U.S.) in October 2003 a representative of the company Titania SpA (Italy) assessed the market of technically pure titanium. He pointed out that starting in 2004 a considerable increase in demand might be expected in this sector. According to his statement, in the next three years potential needs for rolled titanium at enterprises specializing in water-desalination will reach 1,000 to 1,300 tons and needs of electric power plants will amount to 6,500 to 7,000 tons a year. After some depression construction of chemical and petroleum chemical enterprises will be on the increase again in the next two years. All of them are the main consumers of welded titanium tubes.
It should be noted that in their estimates Western experts do not take into account prospects for Russias titanium market. It is true that until recently titanium tubes, in fact, were not used in civil industries of the Russian economy due to the lack of seamless tubes as well as the absence of the domestic welded-tube production. Tables 1 and 2 prove Russias tremendous lagging behind the West in this area and emerging potential opportunities of marketing welded titanium tubes on the recovering Russian economic space.
Along with favorable short-term predictions in the traditional areas of using titanium tubes there are reports on promising developments of ecologically clean sources of energy that interest makers of titanium tubes.
The Japanese organization Saga University has developed a power plant for processing oceanic thermal energy (OTEC) that generates energy to rotate turbines through evaporation of ammonia by hot ocean water. After that ammonia is again liquefied by cold ocean water. The company Xenesys Inc. has acquired the right to use the OTEC system and has received the Indian governments order to construct an experimental plant. The company Kobe Steel has already obtained the exclusive right to supply titanium for making these plants.
Another promising direction in power engineering that may result in a considerable demand for titanium tubes is the construction of floating nuclear power plants with small capacity
(FSCNPP), which can be built in quite a short time and which can be quickly recouped. Russia has a leading position in this area by having offered several designs of such plants to the international community. Construction of the first one in the city of Severodvinsk is stipulated in the federal target program Effective Economy. Later, floating nuclear power plants are to be built in the towns of Peveka in the Chukchi federal district and Vyluchinsk on the Kamchatka Peninsula.
Russia has one more priority goal: export shipments of floating nuclear power plants as part of nuclear water-desalinating complexes. At present, there are negotiations underway with interested countries and they are already close to signing contracts. A floating power-generating unit can provide customers with heat, electric power and fresh water. A single complex is capable of supplying fresh water to a town with the population of 1 million people. Its production capacity is from 200,000 to 400,000 cubic meters a day. This direction of the countrys activity is especially pressing since the world deficit of fresh water is quickly increasing.
In 2003 VSMPO and the American corporation Allegheny Technologies Incorporation (ATI) have set up the enterprise Uniti Titanium, a joint venture to combine potentials for raising output of products made of technically pure titanium at reduced costs as well as for expanding the use of titanium in various civil areas. In the first place, the activity of Uniti Titanium will have a positive impact on quality and volumes of making welded titanium tubes produced by VSMPO. ATI possesses the most advanced equipment to produce strip designed for welding tubes. There is no such an equipment at VSMPO. According to the technological scheme adopted by both sides, VSMPO supplies its slabs to Uniti Titanium for producing strip, which, then, returns to VSMPO for making welded titanium tubes.
Thus, this JV has a closed production cycle of manufacturing high-quality welded tubes, which is based on modern equipment and which includes all process stages, from getting ingots to making and controlling finished products. This allows to meet the demand of the developing Russian market for welded titanium tubes and also gives VSMPO a chance to become one of the major suppliers of high-tech products in the world market.
|
|
|
|
current issue

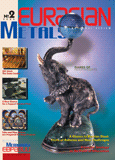
previous issue

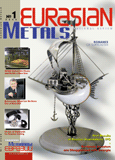
russian issue

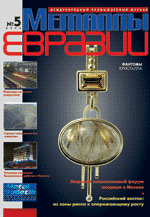
|
|