|
Magazine |
|
About |
|
SUMMIT |
|
Contacts |
|
Home |
|
|
|
|
| |
|
|
 |
#1' 2004 |
print version |
UNCONVENSIONAL RESOURCES OF ALUMINA |
|
Yuri Kustov PhD in Geology & Mining
he Closer to the Tropics the Better Bauxites
The earths crust is much more rich in aluminum than in iron. There are hundreds of minerals with aluminum inside. However, the modern metallurgy uses only those of them, which can be processed economically effectively. High-grade low silica bauxites with more than 45% of alumina and less than 5% of silica are considered the best raw material for production of aluminum. Generally, such minerals formed as a result of a so-called lateritic erosion of formations in a hot climate of moderate humidity. Tropical countries like Guinea, Brasilia, Jamaica, Venezuela and Australia, where the precious mineral grows ripe, are the main suppliers of it to the world market. Young geological formations of these regions contain about 90% of the all the bauxite reserves available in the world.
In Russia bauxites occur in more aged deposits. Compared to the tropical countries where bauxites occur next to the surface, Russian bauxites are generally buried under thick layers of sedimentary deposits. While tropical bauxites exist mainly in an easy-to-recover trihydrate modification, Russian bauxites are mostly of a monohydrate modification that makes them much more expensive to recover and process.
The bulk of alumina produced in the world is extracted from tropical bauxites using the Byers process, which implies pressure leaching of alumina, with hematite, a resultant iron-silicon compound, going to waste.
To sinter high silica bauxites a more expensive technology has to be applied. When sintering monohydrate ores consumption of power is 4.5 times more than that required for processing trihydrate bauxites by the Byers process.
Both the Byers process and, in particular, the sintering technology have a number of disadvantages, which limit the scope of their application and result in a high consumption of caustic soda, steam and fuel. Therefore, Russia likewise other CIS countries processes its high-grade bauxites using a combination of the Byers process and the sintering technology.
The most representative parameter to estimate the quality of bauxites is a so-called alumina factor that is calculated as the content of alumina (expressed in percentage) less the doubled content of silica. For tropical bauxites the alumina factor exceeds 50%. For Russian bauxites it is significantly lower: 42 to 45% for the Northern Uralsk bauxite mine, 27 to 35% for Timan bauxites and 16 to 19% for bauxites mined in the St. Petersburg area.
Though Russia has 3% of all the world bauxite reserves, these bauxites are mainly of poor quality to be processed using expensive and power consumptive methods. This is the main problem of the Russian aluminum making industry.
Alumina Production is Next to Unprofitable
6 million tons of alumina are required to load Russian aluminum smelters to their full capacity. Russia actually imports approximately 3 million tons that is half of the required volume. About 1.600 tons of aluminum can be actually extracted from Russian bauxites, with other 1.500 tons refined from nephelinic ores.
About 70% of all Russian bauxites are mined from bauxite deposits in the Severouralsk area, the Sverdlovsk region. These bauxites, the best available in Russia, contain on average 50.2% to 56 % of aluminum oxide and 2.6% to 4.8% of silica. Being developed for more than 10 years, the Severouralsk deposits still have significant reserves of bauxites. Local bauxite-bearing formations occur very deep (at a depth of more than 700 m) that makes their development unprofitable. Unfortunately, Russia has actually no other option.
Another Russian area, which has more or less serious bauxite mining potential, is the Timan region. The Central Timan bauxite mine has regularly supplied Ural aluminum plants with the raw material since 1998. Today it produces as much as 20% of all the bauxites mined in Russia. Reserves of bauxites available here are rich enough to keep their production at the same rate for more than 100 years. The problem is that only half of these reserves can be actually processed at the Ural plants. Therefore, now the Timan bauxites are considered as a source of raw materials for a new alumina refining and aluminum smelting industrial complex SUAL group intends to build next to the place of mining the bauxites. This investment project is deemed the largest one in Russia.
Significant reserves of low-grade bauxites are also available in the Onega-Tikhvin region, the St. Petersburg area. The bulk of them occur within the Ixinskoye bauxite deposit, which produces about 7% of all Russian bauxites. This raw material is in low demand as there are no economically effective methods developed to date to process such high-silica bauxites.
As a matter of fact, there are three bauxite refineries operating in Russia now, namely:
Ä the Bogoslovsky Aluminum Plant in the town of Bogoslovsk, the Sverdlovsk region, based on a combination of the Byers process and the sintering technology to use high-grade Byers bauxites (85% of the sintering mixture) and low-grade sintering bauxites (15% of the mixture);
Ä the Ural Aluminum Plant, the Sverdlovsk area, also based on a combined bauxite processing technology. Due to its technological peculiarities the smelter can process only high-grade Byers bauxites; and
Ä the Boxitogorsk Smelter in the town of Bauxitogorsk, the St. Petersburg area, which uses only the sintering technology.
Perspectives and Alternatives for Raw Materials
An economic analysis shows that assuming further expansion and modernization of the Bauxitogorsk Aluminum Smelter with hydro-chemical processing implemented, construction of a new alumina refinery and further development of bauxite mining in the St. Petersburg region can ensure a profitable production of at least 1 million tons of metallurgical alumina.
The Belgorod bauxite-mining region in the middle of Russia also has a pretty serious reserve of bauxites acceptable for metallurgy by quality (A2O3 Ä
49,5 %, SiO2 Ä 8,3 %). This regions bauxite bearing formations occur deeper than 500 m. To make their development economically advisable it is necessary to construct an alumina refinery complex next to the bauxite mines.
The Central bauxite deposit in the Krasnoyarsk area is the only bauxite mine in Siberia that is worth mentioning. This deposit can be considered only as a base for a small capacity alumina refinery (not more than 250,000 tons of alumina per year). Unfortunately, poorly developed industrial infrastructure of this region makes it difficult to mine local bauxite ore.
Thus, though strictly limited in sources of basic bauxites Russia is pretty rich in nepheline ores also suitable for aluminum production. For example, significant reserves of apatite based nepheline ore, post-processing tailings of which serve a high-grade complex of basic alumina, are concentrated in the Murmansk area. 6 bauxite deposits currently under development and 5 bauxite deposits in state reserve contain bauxites enough to keep their mining for the next 80 years. Today from this ore appatite is extracted in full, with napheline being recovered only partly.
Nepheline concentrate obtained is generally refined at the Pikalevskai mining treatment plant in the St. Petersburg region. Nepheline concentrate contains up to 28.5% of alumina, while regular bauxite ore has only 12 to 15 % of this substance. Maximum output of alumina recovered from this ore never exceeds 6%.
The Achinsk alumina refinery in the Krasnoiarsk area processes nepheline ore mined in the Kemerovo region. Deposits available in this region are rich in high-grade bauxites (alumina concentration accounts for 26 to 28%), which are mined openly with no mining treatment required.
Rich-in-nepheline ore is processed by means of sintering. Compared to bauxites, nepheline ore contains alkali in the amount that is sufficient or next to sufficient for sintering. It makes it possible to sinter such ore with limestone in revolving furnaces at a temperature of 1250 oC to 1350 oC to produce a number of by-pass products like soda, potash and gallium. Slime resultant from processing nepheline is used for cement production. Thus, all the components of nepheline concentrate can be used. With 80 % of Al2O3 extracted in the form of commodity alumina, this method requires 5 times more power than in the Buyers process so that economically this method can be justified only in terms of complex use of raw materials.
Though nepheline ores will for long remain an important source of raw material for Russian alumina industry, there is no necessity to expand their mining: processing of such ores gives too much by-pass products like cement, soda and potash which are difficult to accommodate on the market.
Possible Improvement of Technologies
Russia actively conducts research in technologies and methods for processing rich-in-aluminum ores. Though the results currently obtained allow to improve some stages of the process, none of the novelties offered to date can compete with effectiveness of the Byers process based production of alumina from high-grade bauxites.
One of the most promising inventions in this field is a method of ore refining based on acid treatment developed by Yury Sutirin. This method uses sulfuric, nitric or hydrochloric acid to treat basic ore. For this purpose the ore mined is exposed to calcining followed by leaching the calcined product under pressure with 150 g/ltr acid solution at a temperature of 150 oC to 180 oC. The resultant solution of aluminum nitrite is exposed to hydrolytic decomposition under pressure. Aluminum is extracted from the solution in the form of hydroxide, while the acid, which remains in the form of liquid, goes for regeneration. Agent used for the process does not react with silica. A volume of the agent consumed for aluminum to pass into solution is regenerated to be reused in the process.
|
|
|
|
current issue

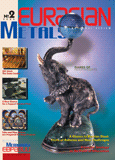
previous issue

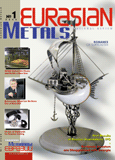
russian issue

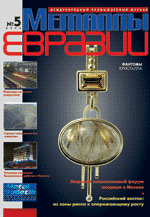
|
|