|
Magazine |
|
About |
|
SUMMIT |
|
Contacts |
|
Home |
|
|
|
|
| |
|
|
 |
#3' 2004 |
print version |
|
MANUFACTURERS OF STEEL-MAKING MACHINERY ANTICIPATE INCREASE IN RUSSIAN ORDERS |
|
ianpietro Benedetti, President and CEO, Danieli & Company:
In the opinion of Gianpietro Benedetti, the competitiveness of Russia¡¦s steel industry is based on rich natural resources, comparatively cheap energy sources, high professional skill of engineers and workers. That is why there are reasons to believe that in a few years by rates of growth Russian companies will outdistance their European rivals. In the first place, it will have an impact on export shipments of half-finished products, such as slabs and blanks, the competitiveness of which is mainly determined by the cost of energy and raw materials.
The president of Danieli believes that at present Russian steelmakers have two major tasks: to raise the efficiency through reducing production costs and to ensure the quality of metal products. It is obvious that to this end there is a need for investments in modernizing production capacities. This will contribute to the growth of competitiveness that will lead not only to increasing export shipments but also to a significant expansion of domestic demand for high-quality metal products.
Investment projects of Russia¡¦s leading companies embrace all process stages of the steel-making cycle and, as a whole, are in line with main trends of the world metallurgy development in the last 15 years, the speaker pointed out. For example, the major directions of improving the technology of the blast melting are the reduction of coke consumption and growth of productivity. At the steel-melting process stage there is a wide use of the technological converter (or electric furnace) ¡V out-of-furnace processing unit (furnace-ladle) scheme. It is inconceivable to imagine a modern production without using continuous casting machines of various modifications equipped with regulating and quality control systems. Different units are used in the rolling production to control thermo-mechanical parameters of metal deformation as well as mechanisms to raise surface quality and dimensional accuracy of rolled products, instruments of nondestructive control and flaw detection. Mills are provided with highly productive continuous lines for metal galvanizing.
By introducing and developing these technologies during the modernization process Russian companies will reach the level of the world¡¦s leading metal producers. Apparently, the next stage will deal with perfecting the industry¡¦s organizational structure, creating and rationalizing an effective system of marketing and metal supply on the basis of advanced information technologies.
In the opinion of Mr. Benedetti, the Russian steel industry has significant reserves to increase competitiveness and, besides, there are ore, coal and energy that many steel companies in the world cannot boast of. Thus, this industry is confidently advancing to logically obvious success, to commercial strength.
Georgy Skudar, President, Novo-Kramatorsk Mechanical Engineering Plant JSC, Ukraine::
- It is gratifying that Russian steelmakers are set to modernize their production facilities and have good financial conditions for it. In our opinion, the mechanical engineering has two tasks that it has to accomplish for the sake of active participation in supplying equipment to steelmakers:
1. To create competitive, highly efficient technological complexes on the basis of scientific research and engineering developments. These complexes are to introduce energy-saving and ecologically cleaner technologies making it possible to manufacture products of exceptional quality. They have to be equipped with units to automate high-level technological processes.
2. To create an engineering and production potential that will make it possible to develop and manufacture in the shortest possible time a new reliable, high-quality equipment. This equipment will be supplied in complex, with contract supervision and adjustment on the turnkey basis in order to check its conformity to required technological parameters.
The Novo-Kramatorskl Mechanical Engineering Plant wasted no time to concentrate itself on exports, aggressive marketing, flexible price policy, technical re-equipment, introduction of resource-saving technologies, production diversification and modernization of equipment being made. We developed an exceptional production potential for metallurgical, assembly and welding facilities. This allowed to considerably reduce the gap between our technological processes and those of the world level.
Georgy Skudar told about a new equipment for steel industry that was developed at the plant in the last four years. In his opinion, this equipment can successfully compete with the similar Western one. These are, above all, electric arc steel-melting furnaces of alternating current, out-of-furnace furnace-ladle steel processing installations, units for vacuum processing of steel in the VD/VOD ladle, section and slab continuous blank casting machines. After having gained an experience in making components of these machines under the Voest-Alpine technology the plant supplied this equipment to Ekostahl (Germany), LTV (the U.S.), Donawitz (Austria), NLMK (Russia).
One of the plant¡¦s traditional directions of activity is the creation of technological complexes to make flat and long-length rolled products. Among the latest developments is a three-stand mill that provides rolling a super thin strip up to 1 mm thick with cold-rolled metal properties. Besides, the plant possesses the technology of making equipment for thick-sheet mills, which is successfully operating at the largest enterprises in India, Poland, Russia.
Georgy Skudar made a presentation of a batch of a new machinery for mining production: walking excavators, boring rigs, grinding-transshipping units, mine-lifting machines as well as equipment for coal mining, such as excavating machines, etc.
Alexei Evgeniev, General Director, SeverStalMontazh Company:
- It is pleasing to realize that I am reporting to the world about our business for the first time at precisely this very interesting, representative forum.
We have been developing our business for already more than four years. It was started as repair shops of the Cherepovets integrated steel mill. And today the group includes 11 companies specializing in engineering, servicing and heavy engineering. We are operating in four regions but this year we are planning to move to another two or three regions. We have over 11,000 employees. Our turnover amounts to approximately $150M and, by estimates, in 2004 it will reach from $250M to $300M. In short, the company is dynamically developing and our plans are quite aggressive.
Expenses on repairing equipment at steel-making enterprises average between 6% and 10% of products¡¦ prime cost. It is not a small piece, is it? But we are servicing equipment not only at steel industry enterprises, we are also working in the energy field, in the mining industry. And we are interested in the pipe-making industry as well.
Let us have a look at how servicing of equipment is done today. There are different levels of it. The first one is the inside system with the servicing division being the center of expenses. Usually, Russia starts with precisely such a level. The second level is more complicated; lists of defects to be eliminated are compiled and costs of operations are agreed upon. Then, contracts indicating required results and bonuses are signed. In Europe work is limited to the two last levels. And, as far as we know, although not all enterprises practice it in the U.S., there is a system, under which a services company fully takes upon itself all the responsibilities for servicing equipment, i.e. for diagnostics, supply of spare parts and all related expenses. We prefer to stick to the American way.
The main principles of servicing industrial enterprises are well known:
ƒŞ Economic efficiency of operating equipment. A customer is always interested in getting the equipment that operates with the maximum efficiency. But, as a rule, a customer¡¦s own services divisions do hardly share this desire;
ƒŞ Mutual understanding of problems connected with basic production and repair business;
ƒŞ Long-term obligations of a services company and its customer. There can be no servicing for one, two, three months. If an enterprise hires an outside services company, then, as a rule, these are sufficiently long relations;
ƒŞ Efficient use of resources of both a client and a services company;
ƒŞ Full responsibility of a services company.
When handing over the job to a services company, a customer retains control over results of its work and observance of norms of protecting labor and preventing accidents. The remaining functions are taken upon by a services organization. We had a remarkable discussion with one CEO of production enterprise. He asked: ¡§ When do you do servicing?¡¨. Under the old practice, during the capital overhaul servicing is traditionally directed by a shop superintendent. When we do servicing, this duty is assigned to our representative. ¡§And what a shop superintendent does?¡¨. He just leaves keys and goes on vacation.
We assume responsibility for our servicing work implementation according to schedule, emergency stoppages, technical servicing of equipment, assembling, dismantling, making and supplying spare parts. Today, our services list is more like a menu: a client chooses from it whatever he needs This list includes:
workers¡¦ labor;
repairs of equipment (both overhauling and current);
manufacturing equipment and spare parts;
supply of materials and spare parts;
purchase of new equipment;
diagnostics;
daily technical servicing;
technical servicing with replacement of equipment.
Depending on specialization this extends to mechanics, hydraulics, power engineering, electric field, control equipment and automatics.
How does Severstal do all this? We started our operations in 2000 and in 2001 we mainly worked on the ¡¥from-order-to-order¡¦ basis. In 2002 we signed a general contract and since 2003 our company has been doing servicing. Repair expenses per ton of manufactured products were reduced by 46%, idling of equipment went down by 36%, reduction of expenses on personnel doing overhaul repairs amounted to 62.5%.
Our group includes the company Uralmash-Steel-Making Equipment. It closely cooperates with our services enterprises. We constantly engage their engineers for raising the maintainability of units, for implementing modernization and reconstruction, for upgrading reliability. In addition, we have a strong mechanical engineering base that allows us to effectively operate in the market of spare parts.
So, we know steel-making equipment well. We have the engineering experience and we have a highly skilled personnel in this area. All our services organizations are certified according to international standards.
|
|
|
|
|
current issue

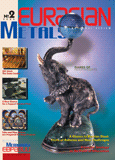
previous issue

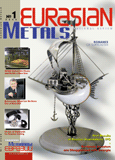
russian issue

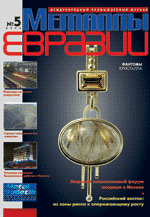
|
|