|
Magazine |
|
About |
|
SUMMIT |
|
Contacts |
|
Home |
|
|
|
|
| |
|
|
 |
#3' 2004 |
print version |
|
METALS PRODUCERS ASSESS OUTLOOK FOR MARKET GROWTH |
|
ictor Pirogov, General Director, Novosibirsk Electrode Mill:
- Russias Energoprom Group has formed a system of coordination that embraces carbon raw material processing mills and mills making carbon and graphite products. Thus, the strategic program, which is effective for all mills, has emerged with the task of developing the electrode subindustry as a single complex. One of the programs clauses provides for conducting a consolidated engineering policy aimed at development, modernization and technical re-equipment of enterprises. A scientific and technological center has been set up to accumulate technological innovations, to ensure their completion and introduction at electrode-producing mills. At present, works are underway to develop new types of graphite for the construction purpose, graphitized carbon materials with improved operational characteristics. There are plans to conduct a complex of research works and develop technological time-limits for production of promising basic materials.
In our opinion, the following tasks are the most pressing:
developing the industry as a single complex capable of providing high-quality graphite products to the steel industry and the non-ferrous metallurgy, mechanical engineering industry as well as to the atomic and chemical industries, enterprises of Russias defense complex;
concentrating resources for reconstruction and technical re-equipment of electrode-producing mills;
creating a base of high-quality carbon raw materials for providing enterprises of graphitized carbon products with low-sulfur petroleum coke, increasing production of coal-tar pitch and pitch coke at by-product coking divisions of Russias metallurgical mills.
Russias production of high-quality pitch should be especially emphasized since this pitch will make it possible to manufacture graphitized carbon electrodes for metals industry that will meet the latest world requirements.
Vladimir Dunaev, General Director, Magnezit Refractory Group Management Company:
- Russias refractories industry consists of several groups of producers. The major portion of products is manufactured by 10 to 12 large specialized enterprises. From 6 to 8 mid-size enterprises as well as a small business group are quite successful in their market activity. In addition, there are refractory-producing facilities at the largest enterprises of the steel industry.
At present, Russias refractory production volume is less than half the level achieved by the early 1990s. However, it is not an indication of crisis. Rather, it is time to discus the progress of technologies. For example, reduction of steel making by the open-hearth method inevitably leads to cutting down the unit discharge of refractories. Improving quality of refractory products gives the same result. In the beginning of the 1990s the durability of refractory-brick lining of converters usually did not exceed one thousand melts but today the best producers guarantee the durability that will last from 4,000 to 5,000 melts.
The renovation of the refractories industry is being undertaken in the two main directions: reforming the organizational structure and modernizing technological processes.
In our opinion, organizational changes will become apparent in consolidation of refractory-producing enterprises. And such a consolidation has already started in Russia. Using the integrated mill Magnezit as a base we have begun to set up a holding with the Magnezit Refractory Group being a management company at the formation stage. Along with the consolidation of refractory-producing enterprises a number of mid-size producers will go down. We believe that later on refractory production facilities at integrated iron & steel mills will be transformed into independent business units because of economic reasons.
Market changes are forcing Russian refractory producers to accelerate modernization of their own production facilities. Big producers are actively introducing the advanced equipment to make periclase-carbon refractories, A number of enterprises have started producing modern types of non-molded materials that have good prospects for being used in the metallurgy. However, the need for such refractories is growing faster than their production. This problem will be partially solved before the end of 2004, when the Magnezit Refractory Group and Germanys Intocast set up a joint venture. Intocast will provide us with the up-to-date equipment and technologies that are non-existent in Russia today. Besides, the German partner expressed its willingness to arrange training of the JVs specialists so as to raise the level of their professional skill and that is in line with our personnel policy. All this allows to regard the JV as a priority project, which is strategically important for developing not just our company alone but for Russias refractories industry as a whole.
The engineering system is a separate direction of developments. The Magnezit Refractory Group has already established an engineering center responsible for servicing heat units in complex. The center offers the whole range of refractories, including those that the holdings enterprises do not make. They are provided under brokers contracts with companies in Europe and China. The center can offer to supply equipment to do refractory-lining works and servicing of heat units in one package with refractories. It maintains a stable relationship with specialists from steel-making enterprises that results in new ideas to upgrade the existing types and to create the new ones.
We think that in order to successfully carry out the modernization of Russias refractories industry it is necessary to make target investments in the following main directions:
1. Investments in developing production areas. In the first place, it has to do with deep modernization of technological processes inherited from the Soviet system of mass-scale manufacturing of products of the limited range. Today we need to create more flexible production lines that allow to quickly react to customers requirements by making both small and large batches of products of stably high quality.
2. Investments in developing the distribution system. Efforts should be concentrated on expanding the distribution network, raising the level of servicing, as well as introducing a system of servicing heat units in complex. For example, our holding is planning to complete the reorganization of the distribution network by the end of 2004. Offices of the holdings distribution network will be opened up by then in all significant consumption regions in the CIS and Eastern Europe.
3. Investments in developing the supply system. Above all, it is necessary to provide Russian producers of refractories with high-quality raw materials. In our opinion, this task is of the strategic nature. Thus, the Magnezit Refractory Group intends to make considerable investments in developing the largest field of high-quality magnesite in the Krasnoyarsk region.
4. Target investments in scientific research and experimental development works. Today they are a ‘must condition of maintaining competitiveness in the market of refractories.
5. Modernization of production facilities, introduction of complex servicing of heat units, engineering and technological innovations will never bring expected results without measures to develop systems of personnel education, certification and motivation. That is why I would call investments in personnel training the fifth important direction of target investments.
At present, all investments of the Magnezit Refractory Group are made under the long-term corporate strategy of development. This gives us a firm belief that we can consolidate the leading positions in Russias refractories industry and make the business of our partners in the metallurgy even more effective.
Yuri Mishin, Director for Marketing, Industrial-and-Metallurgical Holding Management Company:
- The Industrial-and-Metallurgical Holding management company has been set up a year and a half ago; it incorporates several enterprises in the coal business, by-product-coke production enterprises as well as enterprises that make cast iron, vanadium products, molybdenum, chromium, tungsten and items of these metals. In particular, the company Tulachermet integrated in the holding is the largest seller of cast iron accounting for approximately 20% of the world market.
We have made an attempt to assess changes in the worlds needs for metal resources to make steel. Our calculations show that last year the volume of scrap metal processing increased between 30 and 35 million tons. The share of scrap metal in the total demand equals 36% to 37% remaining more or less stable. This trend has been apparent for already quite a long time.
Those processes that have been takiung place in world market lately are, to a large extent, dependent on the situation in China. First, this country stopped major deliveries of cast iron to international market and increased imports of scrap metal and metalized raw materials up to 9 to 10 million tons and up to 1.6 to 1.8 million tons respectively. If all data are summed up, it becomes clear that China has begun to additionally bring out of international market approximately 13 to 15 million tons of metal resources annually as compared with volumes several years ago.
In the last two years there has been a cyclic development of prices and volumes of sales that, in our opinion, has been provoked by two factors. On the one hand, this an absolutely objective factor of the growing need for finished steel products and, on the other hand, this is a purely psychological factor linked to speculation processes. In the late 2002 and the beginning of 2003 the first sharp jump happened, when in literally three months prices for main kinds of metal products rose by 30% to 40%. The growth of prices for raw material components amounted to between 50% and 70%. Then, in March through April of 2003 prices went down somewhat and, later, they were stabilized. This year the situation repeated itself with the amazing accuracy but at a much higher price level. Chinas need for steel products kept growing. It seems that the anxiety of Chinese metallurgists over the coming significant deficit of raw materials played its role. As a result, from December 2003 to March 2004 there was a steep jump in prices again and it was more serious than the one last year, when prices for steel products went up by 60% to 80% and prices for scrap and cast iron rose by 100 and even more per cent.
All these sharp jumps are influenced by the very structure of metallurgical business in China as well as by the way the purchasing operations are carried out. With the total production volume equaling 220 million tons the breakdown was as follows. Forty million tons or 18% are made at enterprises with the annual production volume less than 1 million tons. Enterprises with the volume of 1 to 3 million tons account for almost 30 million tons. So, it turns out that 70 million tons are produced by small enterprises, which never enter export and import markets independently and which buy everything through traders. There are incalculable number of trading companies in China, which, in case of market demand, become very active significantly multiplying the actual need of end consumers. And when the situation becomes more certain, traders start feeling nervous and they get rid of their reserves. This makes the situation worse.
And, finally, I would like to note the following. In todays situation China, being the largest supplier of coke, starts to show us those levers, with which the country will operate soon in international markets. At present, there are artificial bars in effect on prices for coke amounting to $420 a ton FOB. Of this amount $200 is the cost of a license, which a Chinese supplier should obtain. I think that in the future China will operate precisely this way.
Ibrahim Edilbaev, Vice President, Eurasian Industrial Association (Republic of Kazakhstan):
- Mining and melting enterprises, which are members of the Eurasian Industrial Association (EPA), are traditional suppliers of iron ore and chromium raw materials, coal and electric power to metallurgical and energy complexes in the Urals and Siberia. The Sokolovsko-Sarbaiskoe production association supplies a major part of its products, over 10 million tons a year, to the Magnitogorsk Iron & Steel Works. Kazchrom brings to Russia chromium ore and ferroalloys. Aluminum of Kazakhstan delivers annually 1.4 million tons of high-quality alumina. The Eurasian Energy Association ships coal and electric power. All enterprises are developing dynamically so as to remain reliable partners in the future.
TNK Kazchrom integrated in the Donsk ore mining and processing enterprise, Aksusky and Aktubinsk ferroalloys mills is exporting its products to 15 countries. The companys strategic goals are to retain its leading positions in the world industry of ferroalloys and, in the first place, in the chromium one. Kazchrom is actively participating in the implementation of the program Strategy of industrial and innovation development of the Republic of Kazakhstan from 2003 to 2015. In particular, realizing innovation projects will allow to double the production of ferrochromium by 2008 as well as to significantly raise the production of silicon and manganese alloys with no need to construct new ferroalloy furnaces.
A special attention is paid to the raw material base of the chromium industry. The company is optimistic about its future. The source of its optimism is the availability of large proven reserves of high-quality chrome iron ore in the Republics west, where the Donsk ore mining and processing enterprise conducts its operations. Ores are high-grade by their chemical composition. The content of chrome oxide, the useful component, fluctuates from 30% to 55%, the content of harmful components (silica, phosphorus, sulfur, calcium) is insignificant. The hypothetical resources of rich chrome ores of industrial categories amount to about 300 million tons, the hypothetical resources of poorer ores that have an exposure are also estimated at hundreds of millions of tons. Besides, TNK Kazchrom signed a contract with the government of Kazakhstan to do prospecting in the new ore-bearing area in the south-west of the Aktubinsk region, where a major ore reserve is expected.
Arkadi Vunder, Director for Foreign Economic Operations, Serovsky Ferroalloys Mill:
- In recent years there has been a significant growth of prices for metal products, including ferrochromium. Suffice it to say that in the last 2 years prices for some of its grades increased as much as over two times. Precisely this fact is forcing both ferrochromium producers and traders to try, one way or another, to forecast the future of this market.
Experts in South Africa, Kazakhstan, India and Russia did some research works and tried to look to the nearest future, although most of their works dealt with markets of just the high-carbon ferrochromium (charge-chromium). The majority of experts believe that very soon South Africa and Kazakhstan, which account for producing almost 70% of the world volume of ferrochromium, will be able to provide practically all consumers with it. This point of view is shared, to some extent, even in India, the third largest producer of ferrochromium in the world.
Nevertheless, it is necessary to take into consideration the fact that, thanks to a better quality of chromium ore used in Russia, the quality of Russian ferrochromium is higher than that in South Africa. That is why in case of favorable market conditions Russia has its own, even if small, specific niche.
The situation in the market of low- and medium-carbon ferrochromium, where Russia is the largest player accounting for almost 40% of the world market, is entirely different. There are significantly more participants and their shares are distributed more evenly. The position of Russian producers do not look flawless but there are possibilities to consolidate it. To this end the following steps are being taken:
1. Creating their own ore base. The Serovsky Ferroalloys Mill became the first one in Russia, which started to produce ferrochromium from its own ore (today it produces up to 150,000 tons of ore a year). Not long ago the Chelyabinsk Integrated ElectroMetallurgical Mill became an owner of a big and promising chromium field on Yamal. The similar operations in that same area are conducted by the Serovsky Ferroalloys Mill, which, besides, obtained 3 mines in Turkey. Thus, there appears a scheme, under which expenses of Russian producers on ore are being reduced significantly. Also, according to this scheme, ore will be supplied for the price equaling its prime cost and that is several times lower than the market price.
2. Establishing mutually acceptable tariffs on electric power through negotiations with its suppliers. The possibility of getting its own sources of power supply is not ruled out as well.
3. Logistics is being improved. With switching over to container transportation the cost of transporting ferrochromium is significantly reduced, losses are minimized, the ‘just in time system is introduced.
4. Extending the processing of slag heaps (there are about 8 million tons of slag in Serov that contain from 4% to 6% of ferrochromium). At present, various investment projects are being considered so as to considerably increase the return of the metal from slag.
5. The first results of briquetting small-sized and less scarce chromium ores have come in.
6. Certifying production according to the standards of the ISO 9000 system is nearing completion. It will significantly raise the quality level of Russian ferrochromium.
7. The organization of production is changing, holdings are set up, production, economic and financial relations are optimized. These relations allow to considerably reduce expenses of each enterprise.
In our opinion, taking into account the impact of the above-mentioned measures the expert assessments of Russian producers will be significantly better in 2005 and 2006. We believe that during this period Russia will get closer to its rivals in the market of low- and medium-carbon ferrochromium.
Yevgeny Pankov, VMS Holding:
- The Podolsk Mill of Secondary Metals and Alloys integrated in the VMS holding is among the first five Russian producers of secondary aluminum. Its key products are cast aluminum-silicon alloys for the automotive industry as well as deoxidizer in the form of small ingots or small shapes. Before the end of 2004 our enterprise intends to start producing aluminum rod.
Both in the West and in Russia the ever growing attention is being paid to the out-of-furnace processing of steel. The more accurate dosing of deoxidizer allows to more accurately regulate steel quality. We did a comparative analysis of using different forms of deoxidizer. Traditionally, an ingot is used for this purpose. It has a sufficiently low degree of assimilation, i.e. less than one third of aluminum goes for deoxidizing while two thirds are burnt out turning into alumina and going to slag. The consumption averages 2 kg per ton of steel. Before ingot is inserted, it should be crushed into pieces so as to improve the contact surface and the degree of assimilation. And that means additional man-hours.
Aluminum in the form of small shapes bullets, granules, cones, half-spheres is more effective and its consumption is less than the one with using ingot. But in order to insert the smallest shapes it is necessary to have quite sophisticated means. Not long ago pressed tablets or briquettes made of a cheaper material, i.e. crushed cans, chips, appeared in the market. Having low consistence these briquettes float to the surface faster and provide even a smaller degree of aluminum assimilation.
Lately enterprises of the steel industry have started using rod more widely. To use it for deoxidizing not only makes more sense technologically but it is much more advantageous from the financial point of view. In case of using ingot its intake amounts to 0.5 kg to 2.5 kg per ton of steel and expenses on deoxidizing vary from $0.8 to $4. When using rod, expenses may be lower by as much as 2 to 3 times. On average, savings may reach $1 a ton of steel. It means that by using rod our colleagues in the steel industry can additionally get up to $1 million in profit from each million tons of steel.
|
|
|
|
|
current issue

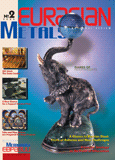
previous issue

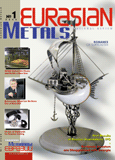
russian issue

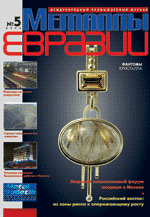
|
|