|
Magazine |
|
About |
|
SUMMIT |
|
Contacts |
|
Home |
|
|
|
|
| |
|
|
 |
#1' 2003 |
print version |
|
THE SIBERIAN BEAR IS CATCHING UP WITH PROGRESS |
|
Yuri Adno
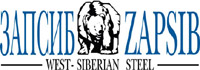 he trade mark of West-Siberian Steel Corporation depicts the bear looking heavy and awkward. But today this symbol is more reminiscent of invincible power. West-Siberian Steel Corporation (ZSMK or Zapsib, the acronym most used in Russia) incorporated into the structure of EvrazHolding managing company is the biggest steel works located in Siberia. In production tonnage, ZSMK ranks fifth in Russia and 30th in the steel industry.
The story of this works, like a drop of water, reflects all the contradictions of the development of the Russian economy in the preceding decades. ZSMK was the last integrated iron & steel works built in the Soviet epoch. For a number of reasons, the works was put on stream without the most critical production stage continuous casting of steel. This stage was planned to be set up later on, as the production tonnage grew. But this good intention failed to be implemented.
On the start of market reforms in Russia, ZSMK, like other steel producers, was privatized and put into the hands of private shareholders. Because of the lack of its assets and with extra high-interest credits, the works payables built up rapidly. This period ended in bankruptcy. In its function as a crisis manager, EvrazHolding was successful. The companys management did well in stabilizing the production cycle, strengthening the market position of the works and paying the debts. The bankruptcy procedure was terminated in 2002, and now West-Siberian Steel Corporation continues its work under the management of the holding as one of its enterprises.
In main technical and economic indicators, Zapsib belongs to the best enterprises of the Russian steelmaking complex. It is the leader in the output of building and engineering rolled products. Its share of the world rolled steel market is more than 0.5 %, that of the Russian and CIS markets is 10 and over 5 %, respectively. In this product line, rebar and wire rod account for over 45 and 50 % of the Russian output, respectively, and reinforced wire, about 70 %. In the opinion of Aleksandr Lavrik, the first deputy managing director, the works products are in stable demand which is, above all, the result of the continuous work on the improvement of engineering level of production and quality of finished products.
The new stage of the development of the Siberian flagship starts in the conditions of not a very favorable situation. The effect of the ruble devaluation in August-1998 when export became highly-profitable has been virtually exhausted. External factors, like antidumping sanctions, redundant facilities, unstable world prices for steel products, seem to be more and more negative now.
But internal problems, above all, the lagging of engineering level, present the greatest difficulty so far. In the world steel industry, the continuous casting ratio is about 86 % in crude steel production. An integrated steel works without continuous casting is a technological anachronism. That is why ZSMK faces the task of completing as soon as possible transition to an up-to-date casting process, and the settlement of this task has become the core of the forthcoming modernization.
A transition to 100-% continuous casting will permit a 1516 $ lower prime cost of one ton of steel because a cumbersome energy-intensive primary reduction stage (the blooming with two reheating pits) is to be phased out, and the ingot mold and mold fleet preparation shop to be eliminated. Steel loss will be 1520 % lower (no ingot crop). The continuous casting process will upgrade the steel mix through a step-by-step transition to more expensive killed steel grades. It is estimated that with an existing steel production tonnage at the works (about 5.5 million ton per year), the introduction of continuous casting can bring about a total annual saving of up to $100M.
The technical and economic advantages of continuous casting were vividly demonstrated by the recent commissioning of the Danieli CCM, world No.1 in capacity, in BOS-2 of the works. Due to it, the works got a unique proving ground for the development of this production stage.
The production modernization program has been elaborated with due regard to the fact that West-Siberian Steel Corporation is viewed as the leading steel enterprise of EvrazHolding in Siberia. In this region, the holding also incorporates the enterprises formed on the basis of Kuznetsk Steel Corporation (KMK) and the Kuzmin Novosibirsk Steel Works.
The program is to be implemented in several stages. The first stage (2004-2005) includes three billet CCMs and two LFs to be installed in BOS-1, with one LF in BOS-2. A slab CCM in BOS-2 and the revamped 250-mm mill are to come on stream at the second stage (2006). The third stage is dedicated to the construction of a wide strip mill with a strip finishing department. Finally, the fourth stage (2009-2010) involves the completion of the coke-oven battery and putting-into-practice of strip rolling facilities.
The first modernization stage costs $100M, in consideration of civil-and-erection works. The investments as foreign bank credits are intended to be involved. Since the bankruptcy procedure was terminated the solvency of West-Siberian Steel Corporation substantially increased. This potential is supported by the high reputation of EvrazHolding as well. Financial risks of the works crediting are quite reasonable. Recently ZSMK JSC introduced the world standard of finance-and-accounts records into its practice, making its activities fairly transparent. Technical, financial and legal audits carried out by Roland Berger, Ernst & Young, McLellan, Studio Legate Tributario confirmed the above.
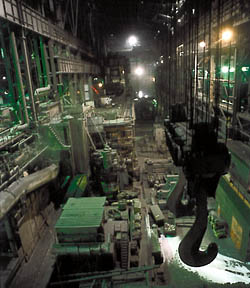 BOS-1: here begins the modernization to cover Zapsib at large. |
|
In November, 2002 a tender connected with the forthcoming modernization of Zapsib was held. The leading metallurgical equipment makers Danieli, Voest-Alpine, SMS Demag, Novo-Kramatorsk Machine-Building Plant (Ukraine), United Machine-Building Plants (Uralmash, Russia) participated in it, thus pointing to the high attractiveness of the project. As stated by Sergey Nosov, the managing director of ZSMK, the holdings and works managers were very careful in the selection of the offered equipment and technologies: "We were carrying out an in-depth, multi-aspect analysis engineering level, prices, time of manufacture, supply and erection of equipment, quality of products, manpower and environment control". As stressed by Nosov, "the technical solutions that will govern the production efficiency at least till the middle of the century are being laid at present".
The modernization will require a correction of the marketing policy. Nowadays the key output product of the works is long products from plain steel grades of building and constructional application; billets, the cheapest item of the products, account for around 40 %. When continuous casting is introduced into practice the works will be able to widen the commercial product range by value-added rolled products. On commissioning the slab CCM in 2006, Zapsib intends to enter the market with higher-value strip entry stock and ultimately set up own thin strip production operations (if funds are available). It will secure a firmer market standing. It may be the way to compensate an anticipated reduction of billet exports to China the country that is now intensively developing its own steelmaking facilities.
|
In 1999 EvrazHolding came to manage ZSMK when it was in the state of bankruptcy. The new management normalized the business operations, in particular, through optimizing financial and material flows. In 2001 an amicable settlement was reached between the works and the creditors. In February, 2002 all managing bodies of West-Siberian Steel Corporation JSC were restored at the extraordinary shareholders meeting. |
|
In Sergey Nosovs words, the presentday situation allows a fairly free choice of technical innovations modernization of certain operations can start from zero point (a greenfield project), in a certain sense. For example, an interesting innovation is to use a casting-and-rolling module in the future strip rolling operations with the casting of thin slabs, similar to the highly-effective CSP (Compact Strip Production) process. Now more than 20 plants of similar type operate worldwide. In Russia there is no similar production process as yet, and Zapsib can be a pioneer in its development. In this case one metric ton will cost $100 less than in the traditional production process. Thus, the investments would be repaid much earlier.
This modernization gains special importance in consideration of the cooperation with the other enterprises of EvrazHolding. Having redundant facilities, Zapsib will become the main supplier of pig iron and steel for Kuznetsk Steel Corporation located nearby (both enterprises are in the same city of Novokuznetsk) where the obsolete production operations can be step-by-step phased out. Accordingly, the local raw materials base will be fully employed by the BF operations at ZSMK. In the long run, supplies of slabs to Kuznetsk Steel Corporation and the Kuzmin Novosibirsk Steel Works must substantially grow. Therefore it is quite logical that the idea of a single strategic program for the development of the steelmaking complex incorporated into EvrazHolding appears.
The main factor in the forthcoming modernization of ZSMK is the policy of EvrazHolding, the company that was able to positively settle the property issues which ensured the investment attractiveness, confidence of financial partners and possibility of directing investments to re-equipping of the works.
|
|
|
|
|
current issue

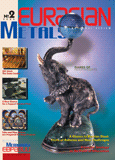
previous issue

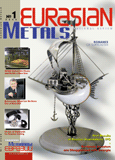
russian issue

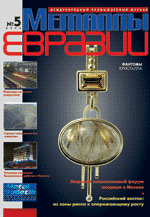
|
|