|
Magazine |
|
About |
|
SUMMIT |
|
Contacts |
|
Home |
|
|
|
|
| |
|
|
 |
#5' 2003 |
print version |
MAGIC OF RUSSKAYA KOVKA |
|
Vladimir Potapov
Imagination and skill, masterly handling of technology, excellent knowledge of metal peculiarities and potentialities... All these qualities are typical of craftsmen at the Lipetsk enterprise Russkaya Kovka (Russian Forging) that has been active on Russias market of forged products since 1994. The firm has won the country-wide recognition by its allegiance to traditions of the Russian school of the forging craftsmanship. By the decision of the Russian Ministry of Culture, Russkaya Kovka was included in the Register of Folk Artistic Trades.
he blacksmiths work in Russia dates back to the ancient times. This trade was highly valued and was the source of various legends. It was widely thought that blacksmiths were patronized by Svaroga, the Old Slavic God of Skies and the Father of the Sun and the Fire, that they could do salving and fortune-telling, keep off the evil spirit.
The heyday of the blacksmiths work took place between the 15th and 17th centuries. Blacksmiths started taking up their residence together by founding settlements. By the way, that is why one of Moscows streets is called Kuznetsky Most (Blacksmiths Bridge). Forging corporations emerged. Specialists are still very much amazed at swords, sickles, axes, knives, chain armor and helmets made by craftsmen of those times. What is more, forgings got decorated with traceries and ringlets. Under Ivan the Terrible (from 1530 to 1584), the Grand Duke of All Russia (since 1533) and the Russian Czar (since 1547) blacksmiths were already forging army cannons.
But, nevertheless, the technology of the Russian forging was being perfected through making mainly articles for household use: window openings were closed with fine bars to protect from desperados, fire protection was provided by solid iron shutters and doors, stone temples were decorated with richly arranged iron gates. Forged fences surrounded town manors, mansions, church courtyards. Blacksmiths began to create unique art compositions in the 17th century, when Moscow was changing from the wooden city to the stone one.
The 18th century brought about many innovations to making forged bars. If before they were produced by the strictly observed modes, this time a different style called the Russian baroque took the upper hand. They were looking like as if they were made of garlands of branches and flowers. Under Peter the Great (from 1672 to 1721), the first Russian Emperor (since 1721), Russia built a lot of armories, which were arranging foundries. Forged fences started to contain cast steel components. And cast iron foundries even replaced forging in Saint Petersburg as it was more costly.
However, under the influence of classicism of the 19th century famous Russian architects Bove, Jilyardy, Kazakov and Bazhenov got back to the originality of artistic solutions that were made possible through forging only. Thus, large spacious compositions made of forged metal appeared on balconies, fences of mansions.
By the national Russian tradition, the town-building played the major role in implementing the program of glorifying Russia. If during the epoch of Peter the Great all construction trade was transferred to the northern capital, in the years of Katherine the Great complete streets were built throughout the whole Empire. The same course was followed by all monarchs after her. The only difference was that some of them gave preference to building Orthodox temples, some favored palaces and others priority was army barracks and courthouses. But, in the bottom line, all these structures are still the pearls of Russian cities.
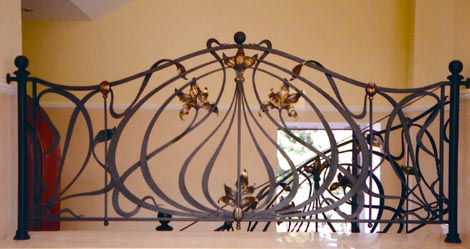 |
The next revival in the history of the Russian artistic forging started with the arrival of the modernist style on the eve of the 20th century. Forged caps of porches, roof ridges decorated unique silhouettes of buildings designed by famous architects Schusev, Shekhtel, Gypius and Goletsky.
It seemed that in the Soviet years of the mid-20th century the forging gave way to the artistic casting for good. The profession of blacksmith started to slowly fade away. Only in the last third of the 20th century the forged metal unexpectedly caused the splash of interest among sculptors since articles made of sheet metal turned out not to be so expensive as the cast ones. Ancient motifs of the forging did find use again. Even such a concept as graphic sculpture was born...
|
METHODS OF FORGING
Beginning from the earliest days till today the technique of the artistic forging has not practically changed. There is a certain number of methods but by summing them up they come to the eight basic ones.
Upsetting. It is used to reduce the length of the blank and to increase its cross section. To this end the whole blank is heated, put on the anvil in the vertical position and, while being held strongly with pliers, the blanks upper end is mauled. It is necessary to prevent its bending and periodically make the blank straight.
Drawing-out. It is used to lengthen the blank by reducing its thickness. The red-hot blank is placed on the anvil and is mauled along the whole length turning it over from time to time. During the forging process it is necessary to turn the blank around its axis. The flattening is done in the similar way, when some part of it should be shaped as a plate.
Chopping. If the forging needs to be divided into parts, the chopping is used. The blank is heated till it becomes deep-red, it is placed on the anvil and is chopped by striking the point chisel with a hammer. After hacking three fourth of it through, the forging is turned over and the same is done underside. In the artistic forging the blank is very often not chopped all the way through but remains just notched. Then, the process goes further: notched tags can be drawn out and shaped like curls, leaves, flowers.
Bending. If it necessary to bend the blank on the angle, either the anvils edge or its opening is used for putting the blanks end into it. Only the part of the blank, which should be bent, can be heated. The arched bend can be made using the anvils horn.
Curling and twisting. So as to curl the blank one of its ends is turned around the axis in contrast to the other. The blanks end is held by the second blacksmith or is gripped in a vice. The twisting means to curl several bars. When doing the twisting, the iron should be heated till it becomes ruby or even yellow so as to avoid cracks and ruptures.
Burnishing. After the preparatory phase is completed, the blank is burnished. But not too much because dents from the hammer remaining in some places make the surface look "live", bear traces of the materials hand-processing.
Pattern indenting. This is one of the final steps in the hand forging. When the blank is heated, traits, broken lines, netting, graphic scenes can be drawn on the blank with a chisel. As this is being done, the blanks plane should remain relatively flat.
Assembling. Although at present shop welding kinds, such as arc, spot, contact and oxy-acetylene, are applied most widely, the traditional ways of fastening details are still used in the artistic forging. These are riveting, assembling with screws, forge welding.
|
| |
|
But the artistic forging has been experiencing the real boom since the 1990s, i.e. in the post-Soviet period. The restoration of ancient city mansions, ambitious out-of-town houses of nouveau riches, construction of banks and business offices, emergence of countless numbers of shops, restaurants and art galleries resulted in the growing demand for the original forgings: lanterns, staircase hand-rails, gates, fences, interior articles and even furniture. Having become accessible the world market made it possible to provide reviving forging enterprises, Lipetsks Russkaya Kovka being one of them, with modern equipment.
However, the favorable starting positions do not mean every thing. There was a need to find ones own face. The enterprise Russkaya Kovka managed to do it. As its general director Vyacheslav Khripko told Eurasian Metals, they made the stake on reviving motifs of the Russian forging handicraft (that is why the firm was named so), on developing its national tradition in modern conditions. The special attention is being paid to products quality. The enterprise is a member of the American National Ornamental & Miscellaneous Metals Association (NOMMA).
The latest technologies of processing, patina-forming and painting articles of Russkaya Kovka are capable of satisfying the most demanding taste. And the firm is used to take desires of its clients into consideration: at their service there are thousands of photos and sketches of enterprises works, consultations by highly skilled artists and craftsmen. And the price in relation to the quality is also attractive.
Today, the Russian artistic forging is going through the revival. Among the present-day articles one can often find images of flowers and plants, birds and animals, mythological creatures, such as Pegasus, griffins. Thanks to blacksmiths imagination even the most ordinary things like door-knobs, hinges, candlesticks can be made a work of art, which gladdens the eye and brings about the specific atmosphere of coming into contact with the high creativity.
Photos are provided by the enterprise Russkaya Kovka
First Frunzenskaya St. bldg. 3-A
119146 Moscow
Phone: (095) 242-2901, 246-9824
Ph./Fax: (095) 242-0470
E-mail: mail@rk.ru
|
|
|
|
current issue

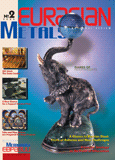
previous issue

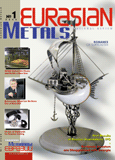
russian issue

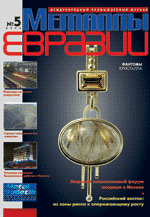
|
|