|
Magazine |
|
About |
|
SUMMIT |
|
Contacts |
|
Home |
|
|
|
|
| |
|
|
 |
#5' 2003 |
print version |
|
MODERNIZED STAMPING PRESS: OUTSIDE GUINNESS BOOK OF RECORDS |
|
Vitaly Dzerzhinsky
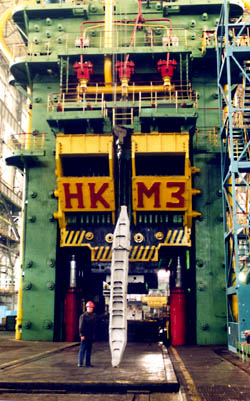 The stamping press with the force capacity of 75,000 tons continues its successful operation at VSMPO |
|
After having been modernized the stamping press, which has the force capacity of 75,000 tons and which is considered one of the worlds most powerful, has been put into operation. The unique unit has acquired new quality potentialities. When it was being tested, there was a task believed to be the top of the forge-and-press skill: a matchbox should be closed smoothly. Showing the absolute confidence in success one of the designers put his wrist-watch on the plate. Operators were amazed to see the highest accuracy, with which the cross-piece of 5,000 tons followed movements of the joystick at the control desk. The matchbox was easily closed and the designer took back his wrist-watch that suffered no damage whatsoever.
ifty years ago the development of the aircraft, space and other high-tech industries required large-dimension, wholly-stamped forgings made of high-alloy, high-temperature, titanium and other hardly-deformed metals and alloys. The two enterprises, Uralmash and the Novo-Kramatorsk machine-building plant (NKMZ) got down to developing a powerful stamping press. The press design worked out by NKMZ in cooperation with scientific research institutes won the competition over the one created at Uralmash. In 1959 the NKMZ design was used as a basis for building a gigantic stamping press with the force capacity of 75,000 tons. Every joint and every component of this unit were new and originally-made. The first gigantic stamping press as well as the second one produced in 1961 were registered in the Guinness Book of Records as the most powerful hydraulic stamping units of that time. Each of them weighed 25,000 ton and their height amounted to 37 meters. They were meant to be used at the Verkhnyaya Salda Metallurgical Production Association (VSMPO) and Samara metallurgical mill, where they have been in operation since then. The one at VSMPO is used to make stampings for aircrafts, spaceships, submarines and nuclear reactors.
In the 1990s VSMPO started actively shipping titanium products to such companies as Boeing, Rolls Royce, General Electric, Airbus Industrie and other world-leading aerospace producers. The quality standards in this area are very high. In particular, Boeing requested VSMPO to submit the complete report on the technological process of stamping each detail with all parameters specified.
Leaders of VSMPO decided to upgrade the press system of controlling technological processes. As a manufacturing plant NKMZ was entrusted with this task. While modernizing the press, the lentil-like shape of blanks being stamped should have been reduced by applying the exact portion of the technological pressure. Also, the wedging had to be eliminated through introducing the synchronizing system in the press, the accuracy of geometrical dimensions was to be improved and the high quality of metal structure was to be ensured. All this was achieved with the help of the specially designed regulator of the adaptive control.
The weight of all the assembled equipment exceeds 500 tons. The complex includes a unique emulsion gear made by NKMZ, oil systems with elemental base produced by the company Rexroth and the system of automated control with Siemens-made elemental base. This way a capability to automatically regulate speed and power parameters was created, the electronic control and diagnostics of the stamping process were secured. The monitor screen clearly shows what move and with what speed every working component of the press does. Available sensors permit to control almost 1,000 different parameters. The system registers all parameters of the technological process and, after all data are printed out, it becomes possible to completely restore each technological operation. Besides, the status of the press can be immediately diagnosed in case of its sudden stoppage due to some malfunction, even if it is just a sensor problem. Before, it took quite a long time to determine a possible trouble.
As a result of the modernization, a number of stages of the press stamping movements has been increased from 4 to 13, and today it is able to implement a wide range of technological operations in the economical mode. The precise choice of the stamping force allows to rationally consume power, to considerably raise the accuracy of produced stampings, to ensure a smaller radius of their deformations. But the most important thing is that it makes possible to provide the high quality of stampings with the required structure and properties. The thickness of metal layer is reduced by 10 % to 20 % being removed later during stampings mechanical treatment. All ideas of designers realized in the modernization project proved to be correct. VSMPO has approved the modernized press for putting it into operation.
|
|
|
|
|
current issue

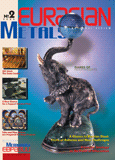
previous issue

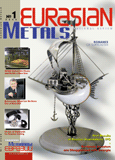
russian issue

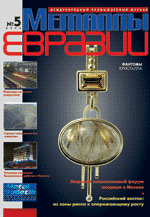
|
|