|
Magazine |
|
About |
|
SUMMIT |
|
Contacts |
|
Home |
|
|
|
|
| |
|
|
 |
#5' 2003 |
print version |
MINI-MILLS: EXOTICS IN RUSSIA SO FAR |
|
Nikolay Pasechnik, Dr.Sc.(Eng.), Boris Sivak, Cand.Sc.(Eng.), Anatoly Protasov, Cand.Sc.(Eng.) VNIIMETMASH
he set-up of mini-mills in the Russian steel industry is an urgent objective so far. The significance of such enterprises continues to grow worldwide. We estimate that by 2010 they will account for about 50 % of world steel tonnage.
At present, by different estimations, their number varies from 400 to 800. Such a scatter is attributed to different criteria applied in estimation. For instance, according to Danieli, a modern mini-mill features, above all, a special flowsheet an EAF, a LF, a CCM and a rolling mill of a narrow product range. However, under this classification, producers of commercial semi-products and those which use not rolling mills but other units (for example, forging machines) at the final process stage are not taken into account.
In special literature one comes across other terms:
"micro-mill", a complex producing 20,000 to 150,000 tpy of finished products,
"local mill" making products for local consumers,
"market mill" fully meeting the market requirements.
Similar complexes can be integral parts of iron & steel works as independent modular units.
A distinctive feature of a mini-mill, regardless of size and production capacity, is a closed well-balanced production route based on BF-free process. Higher importance of mini-mills in the world steel industry is due to a number of objective reasons, among them, growth of scrap reserves and depletion of ore resources, increase of share of transportation charges in steel prime cost, sharpening of ecological problems, rise in the cost of construction of industrial projects. Along with scrap-based mini-mills, enterprises using Midrex metallized pellets or Corex DRI have become well-established.
The main development trends of mini-mills are diversification of product range towards more complex and high-quality types as well as production intensification using energy-saving technologies. An average EAF heat cycle has been shortened from 3 to 1 hour (and below) due to UHP transformers, oxy-fuel burners and other up-to-date equipment. Tube molds for high-speed casting, air-and-water secondary cooling, automated control systems and other improvements permitted higher (up to 5 m/min) withdrawal speed at billet CCMs. In steelmaking consumption of power was reduced from 900 to 400 kWh/t, with that of graphite electrodes from 68 to 1.52.5 kg/t, and installed power increased from 0.30.5 to 0.81 kW/t.
The following can be considered the evident competitive advantages of mini-mills:
rather low investments $250350 per ton of steel which is 2 to 5 times lower (by different estimations) as compared with the construction of integrated works,
short construction period around 1 year instead of 34 and rapid commissioning and re-orientation of production operations,
implementation of newest achievements and science-intensive and energy-saving technologies,
location as near as possible to consumers which substantially lowers transportation charges,
prompt response to market requirements,
efficient fulfillment of orders (maximum 4 hours since receipt) and high utilization rate of facilities,
compact layout and rational management,
high labor productivity up to 1,500 tpy of rolled products per one employee,
decrease in environment contamination by 86 % in air and 76 % in water.
|
Nikolay Pasechnik,
Dr.Sc.(Eng.), 51 years of age, graduated from the Moscow Bauman High School. His career is totally connected with VNIIMETMASH where he has been General Director since 1995 till now. Laureate of Russian State Premium in Science and Technology.
|
|
| |
|
A standard mini-mill of 100,000 to 400,000 tpy capacity occupies an area of 10 to 20 hectares. At such an enterprise power consumption is 3 times lower than at an integrated works. As a rule, the mini-mill has a narrow and specialized product range, mainly, the most mass-produced types of bars and sections. In the last decade, mini-mills which made more sophisticated rolled steel, for example, thin strip, progressed rapidly.
Process block modules open up great prospects. Their specialization is various, very wide and can be rapidly changed. The promising trend is a set-up of steel complexes composed of several modules of up to 100,000 tpy of light bars and sections in capacity. The investments in the construction of such a complex can be lower than in the construction of a similar monoblock.
In terms of product specialization, mini-mills can be divided into bar/section, strip and combined. Academician A.Tselikov, a famous Russian scientist, was of the opinion that parts-rolling equipment was a necessary part of the mini-mill. It permits high processing rate to be achieved and better satisfaction of local demand for general-purpose machinebuilding parts balls, axles, sleeves, rings, etc. It would get machinebuilders more involved in the development of mini-mills.
In CIS countries with a developed steel industry mini-mils have not gained any evident progress. Presently only three long products plants with a classical set of equipment are in operation. They are the steel plants built in the Soviet era the Oskol Electric Steel Works (OEMK), the Belorussian Steel Plant and the Moldova Steel Works which have undergone reconstruction later on and are now operating successfully. The Moldova Steel Works is a kind of polygon for tuning new design solutions. Tube molds for high-speed casting, an energy-saving electromagnetic stirring system and other innovations of VNIIMETMASH design were introduced for the first time at the CCM here.
In Russia the Moscow Serp i Molot (Sickle and Hammer) Plant and Elektrostal (in the Moscow Region), which has a unique casting-and-rolling plant with a planetary mill for hard alloys, can be considered mini-mills only conditionally.
|
VNIIMETMASH named after Academician A.I.Tselikov is a state scientific center of Russia, a joint-stock holding company. It has at its disposal a scientific-and-production base due to which a complete cycle of creating metallurgical equipment, from fundamental and applied studies till complex supply and services, is carried out. It also conducts work for other sectors aerospace and air craft together with nuclear industries plus automobile making. In Russia and CIS on the whole, VNIIMETMASH equipment is used for production of up to 60 % of BOF steel, 70 % of rolled products, 50 % of hot-rolled and 30 % of welded tubes/pipes, more than 80 % of balls and aluminum wire rod. The VNIIMETMASH trade mark is well-known in the US, Japan, UK, Germany, France and other countries where the equipment developed by VNIIMETMASH, large BOFs, light-gage tube/pipe mills, unique pressing and arts-rolling machines, operate. The staff numbers more than 1000 persons, among them, 16 doctors and more than 100 candidates of sciences.
|
| |
|
Meantime there are no flat products mini-mills either in Russia or other CIS countries. A pilot thin-slab casting machine set up by VNIIMETMASH has never reached a commercial level of operation since this project was not financed. However, based on these experiments, a specially designed mold for a thin-slab CCM was developed (ordered by Nucor).
The situation with casting-and-rolling plants based on twin-roller machines is slightly better. After some break, the investigations of casting at a pilot twin-roller machine were resumed. Now the machine is being modernized, trial heats are cast with intensive studies carried out. It can be anticipated that casting-and-rolling plants with twin-roller machines for hot-rolled strip will compete with thin-slab CCM-based route. The advantages are minimum outline dimensions and comparatively low investments, improved mechanical properties of strip and fairly high production capacity up to 400,000 700,000 tpy.
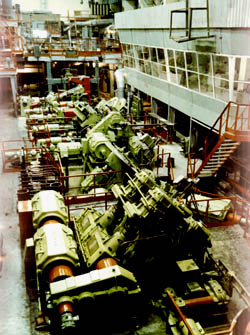 Unique bar casting-and-rolling plant with planetary mill at Elektrostal Plant |
|
In our opinion, now Russia has all prerequisites for the development of mini-mills. It is induced by rapid growth of railway tariffs connected with necessary long-distance transportation of steel products. In the conditions of the start of business expansion, there grows the demand of local markets for steel products of a fairly wide range to be supplied by small lots. This country has vast scrap reserves. Many enterprises need re-orientation of production operations. All the above motivates the necessity of long products mini-mills of up to 200,000 tpy capacity to be located in the areas of largest scrap accumulation and/or intensive consumption of steel products.
Set-up of mini-mills does not contradict development of integrated works. Moreover, some modules can be successfully incorporated into the structure of a steel giant. We think that it is viable to set up pilot modules of different application in several regions. For example, to build a rebars-and-rods mini-mill in Siberia, a light bars mini-mill in Central Russia and a light bars-and-machinebuilding parts mini-mill with a hot-strip module based on a twin-roller casting machine in Ural.
Russia has accumulated the practice of set-up and operation of all components of bars/sections casting-and-rolling plants of different types. VNIIMETMASH elaborated technical offers, business plans and projects for more than 20 variants of mini-mills of different capacity. Now bars/sections casting-and-rolling plants of 200,000 tpy capacity are being engineered for CIS enterprises. The equipment for a light-bars casting-and-rolling plant of 50,000 tpy capacity has been made and is being erected.
|
|
|
|
current issue

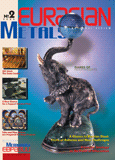
previous issue

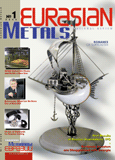
russian issue

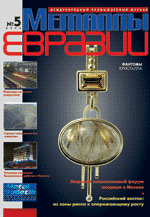
|
|