|
Magazine |
|
About |
|
SUMMIT |
|
Contacts |
|
Home |
|
|
|
|
| |
|
|
 |
#5' 2003 |
print version |
|
SCANDOIUM AND YTTRIUM FROM RED MUD |
|
Valery Diev Cand, Sc. (Eng.) Nail Sabirzyanov Cand. Sc. (Chem.) Sergey Yatsenko Dr. Sc. (Chem.), Prof. Chemistry of Solids Institute, Ural Division of Russian Academy of Sciences
n Ural there are two primary aluminum plants — UAZ (Ural Aluminum) and BAZ (Bogoslovsky Aluminum). Both plants with captive alumina production operations are incorporated into SUAL Group. For production of one ton of alumina, 2.6 t of bauxite containing hydroxides and oxides of aluminum, iron, silicon, titanium, etc., 60—100 kg of caustic alkali, 30 kg of limestone are consumed. Here about 1.3 t of raw materials goes to waste comprised of concentrated slurry named ”red mud”.
Up to now the dominating viewpoint is that accumulation of this waste inevitably accompanies alumina production operations. That is why waste dumps are provided for in construction projects. Meantime as early as a century ago, Dmitry Mendeleev, a famous Russian chemist and the author of the periodic table, noted that the very term of "waste" was incorrect. He suggested to view waste as unused raw material. Nowadays when developing metallurgical and chemical technologies modern scientists hold the opinion that complete recovery of mineral resources is not only possible but compulsory.
Red mud is removed from alumina sand as slurry with inwash on a special site in the form of a long truncated pyramid of 2026 m in height. Alumina production growth and low-quality bauxites involved into processing bring about a constant increase of waste tonnage. It is assessed that by 2010 accumulated red mud will be over 2.5 times more while already today its quantity is awesome.
For 60 years of operation of the UAZ alumina shop, 63m tons of red mud have been accumulated, with three dumps built for storage. Their construction cost millions of dollars and the area occupied by red mud is larger than the production site of the plant. Dump No.1, of 80 hectares in area, has been recultivated, covered with a 0.5m-thick layer of good soil and grassed. Dump No.2 occupies 190 hectares, with 90 hectares filled up to 26 m in height. The recultivation of this area has already begun. The inwashed pyramid is covered with rubbish, barren material from stone quarry, treated sewage sludge and good soil taken from the construction site of Dump No.3. The new dump area is 247 hectares to be filled in 3035 years. One can note that the storage area grows in progression: 60, then 190 and at last 247 hectares! Approximately the same situation is at BAZ where mud. fields occupy over 400 hectares with more than 40m tons of red mud
The mud dumps are a constant threat of possible toxic drain. That is why the environment control departments have to continuously monitor the condition of dump fields. But despite of environment control measures, air, water and soil around the plants are substantially contaminated.
Red mud accounts for at least half of entry bauxite ore from which only aluminum compounds, and not completely, are extracted. A lot of valuable components iron and aluminum share is up to 40 and 16 %, respectively goes to waste. Moreover, there are calcium, silicon, titanium, zirconium, niobium, gallium, gold, rare-earth metals scandium (80120 gr/ton) and yttrium (300400 gr/ton).
Scandium is used as an alloying element. It afforded the development of aluminum alloys for large-size structures of complex geometry applied in most critical equipment, including missiles and aircrafts. AvtoVAZ, the leader of the Russian car industry, also tries to produce parts from such alloys. The tests of the parts proved that they are promising. But in general more extended application of scandium-containing alloys is limited by high cost of Al-Sc alloying compositions.
Neither Russia nor other CIS countries have processors of lean scandium raw material. It is the waste of alumina production which is most promising and profitable for extraction of scandium. The mud after dressing gives an opportunity to produce concentrate containing up to 360 gr of scandium oxide per ton, and additional chemical activation raises it to 400 gr/ton. For comparison: under the project of Ashurst Technology (US), this content is several times lower in the Australian concentrate.
Yttrium is also applied as an alloying additive thus substantially improving mechanical properties and corrosion resistance of iron and steel. An addition of 0.1 % of yttrium doubles wear resistance of iron. In different yttrium-containing steel grades oxidation rate shows a 11-fold decrease.
At present various technologies of red mud processing are available. A pyrometallurgical process is oriented to high-capacity recovery of iron. It is labor-intensive, power-consuming and expensive. A complex nitrate flowsheet of red mud processing with the production of 5% scandium concentrate, nitrogen fertilizer and ferrous cake has been experimentally tested by the Moscow State Institute of Steel & Alloys. The tests revealed such a heavy drawback as high consumption of nitric acid.
Chemistry of Solids Institute of Ural Division of Russian Academy of Sciences jointly with Uralaluminum JSC have developed a chemical hydrology technique for red mud processing. In our view, its advantage against other techniques is obvious. The distinctive feature is pre-dressing of red mud by magnetic separation and chemical activation. As a result, the content of yttrium and scandium increases by 2.5 times (to 360 and 500 gr/ton, respectively) which drastically raises profitability of downstream processing. In the process flowsheet, dressing is followed by break-up of magnetic concentrate with sulfuric acid, with further leaching and hydrolysis, extractive or ion-exchange selective concentration with deposition of scandium and yttrium from eluates of rich concentrates and salts. At the same time iron oxide pigments, acidic Fe-Al coagulants, are produced from mud. The trial of the coagulants at the neutralization plant showed that it is possible to intensify the operation of effluent treatment facilities by 1.5 time with an improvement of treatment quality. The Sverdlovsk Region alone where UAZ and BAZ are located will need tens of thousands of tons each year.
A cementation technique developed by the institute as well was used to produce an Al-Sc alloying composition from industrial scandium oxide (9899 %) and high-purity yttrium oxide from yttrium concentrate for production of phosphors.
The new production process is a combination of blocks. Different schemes can be employed to make different products: Al-Ca and Fe-containing concentrates, scandium or yttrium, joint output of both metals as a function of market situation. It drastically reduces investments in setting up full-scale production operations.
The feasibility studies confirmed the expediency of complex processing of bauxites and set-up of pilot plants at UAZ and BAZ. The plants will use red mud to reclaim 0.5 ton of scandium oxide, 3.5 tons of yttrium oxide, 500 tons of pigment and 2,000 tons of Fe-Al coagulant per year. The prime cost of scandium oxide made according to this process will be $200/kg, with $24/kg maximum for the 2 % Al-Sc alloying composition. About one million dollars with a payback period of one year will be required to set up a red mud processing section. The main thing is that this section will greatly reduce alumina production waste.
|
|
|
|
|
current issue

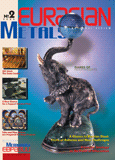
previous issue

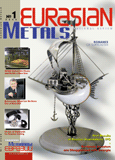
russian issue

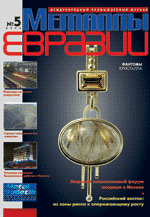
|
|