|
Magazine |
|
About |
|
SUMMIT |
|
Contacts |
|
Home |
|
|
|
|
| |
|
|
 |
#5' 2003 |
print version |
|
METALLIZED BRIQUETTES PLANT BUILDS UP PRODUCTION CAPACITY |
|
Yuri Adno
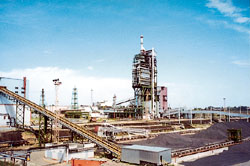 JSC "Lebedinsky Mining and Dressing Plant": metallization module |
|
omprehensive use and development of mineral resources of a particular deposit is one of the main trends of up-to-date mining operations.
JSC "Lebedinsky Mining and Dressing Plant" set up in 1967 based on the iron-ore resources of Central Russia is a mining giant and a top-ranked leader in the market of raw materials for the Russian steel industry. While processing an annual volume of over 45 million tons of run-of-mine ore, the enterprise outputs 20 million tons of iron-ore concentrate and 10 million tons of high-quality pellets. Its annual turnover is $500m.
The Lebedinsky Mining and Dres-sing Plant makes three types of products containing the following weight percentage of Fe: 6768.7 % in rough concentrate, more than 70 % in final concentrate for BF-free technologies, up to 66 % in nonfluxed pellets.
State-of-the-art technologies permitting up to 71 % Fe are applied in the dressing of ferriferous quartzites.
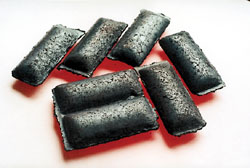 Products of metallized briquettes plant: HBI |
|
Nowadays this enterprise is Russias only maker of raw materials for direct reduction of iron and production of a new type of raw materials metallized briquettes.
One of the main development lines is the construction of a metallized briquettes (hot-briquetted iron HBI) plant at the Lebedinsky Mining and Dressing Plant. The plant is designed for a capacity of 4 million tons of briquettes per year. The decision on its construction was taken as far back as March, 1994. At that time the world steel industry had two metallization technologies Midrex and HyL-III. According to the results of the global tender, the construction was awarded to the consortium of German companies Klockner-INA and Ferrosteel with an involvement of Hylsa (Mexico). The finalized construction contract was signed in December, 1996.
The first HBI module of 1million tpy capacity was commissioned in 1999. The production trend is shown in Table 1.
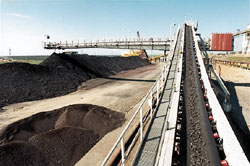 JSC "Lebedinsky Mining and Dressing Plant": conveyer at metallization plant |
|
This product type made from the raw material with a minimum concentration of deleterious impurities is a unique stock for downstream EAF melting and is used, for the most part, in the production of high-quality steels. In opposition to metallized pellets, HBI is not subject to self-ignition, being safe in open storage and transportation.
This product is not only competitive but in high demand in the raw materials markets. The main customers are from Ukraine, Poland, Austria, Spain, Turkey, China, France, Belgium, Finland, Czecia.
The direct reduction technology is HyL-III process when a steam reformer produces converted gas and oxidized pellets made from high-quality concentrate in the pelletizing department are further reduced in a shaft furnace at a pressure of 4 kg/cm2 and a temperature of the reducing gas of 930oC. The depleted gas is cooled and CO2-cleaned for downstream recycling during reduction of oxidized pellets in the shaft furnace. The waste heat recovery system applied at the metallization plant permits high-pressure steam to be produced for power generation.
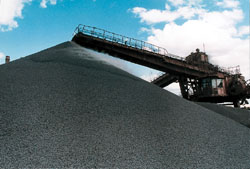 JSC "Lebedinsky Mining and Dressing Plant": ore delivery line |
|
The plant is Europes only and the worlds largest single HyL unit for HBI.
The unique highly-automated equipment, efficient technologies, among them, environment-friendly and resource-saving, ensure continuous growth of the product quality.
At present possible increase of reducing gas temperature with the help of oxygen injection is under consideration. It will lead to a 15 % rise of production rate. The construction of the second HBI module is being prepared for.
|
|
|
|
|
current issue

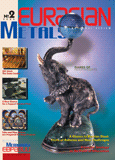
previous issue

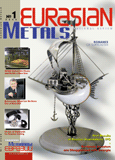
russian issue

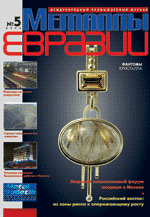
|
|